Файл: Физикотехнологические основы получения композиционных материалов.doc
ВУЗ: Не указан
Категория: Не указан
Дисциплина: Не указана
Добавлен: 07.11.2023
Просмотров: 294
Скачиваний: 4
СОДЕРЖАНИЕ
Физико-технологические основы получения композиционных материалов
1.1. Характеристика композиционных материалов
1.2. Классификация композиционных материалов
1.3. Требования, предъявляемые к армирующим и матричным материалам
Изготовление изделий из металлических композиционных материалов
2.3. Способы получения полуфабрикатов и готовых изделий
3.2. Краткая характеристика порошковых материалов
3.3. Приготовление смеси и формообразование заготовок
3.4. Спекание и окончательная обработка заготовок
4. Изготовление деталей из полимерных композиционных материалов
4.3. Способы формообразования деталей в высокоэластичном состоянии
5. Получение деталей из композиционных пластиков
7. Технологические особенности проектирования и изготовления деталей из композиционных материалов
7.1. Технологические требования к конструкциям изготовляемых деталей
7.2. Технологические особенности дополнительной механической обработки заготовок
5. Получение деталей из композиционных пластиков
С технологической точки зрения удобно использовать отдельные пластмассы, находящиеся в жидком состоянии при нормальной температуре. В первую очередь это относится к производству крупногабаритных деталей из композиционных пластиков. Пластики состоят из связующей смолы, наполнителя и в некоторых случаях отвердителя и ускорителя отверждения. В качестве связующего предпочтительнее использовать полиэфирные и эпоксидные смолы. Эти смолы характеризуются высокой адгезией к наполнителю и способностью отверждаться при нормальной температуре за счет добавления к ним отвердителей и ускорителей отверждения (перекиси бензола, нафтената, кобальта, полиэтиленполиамина и др.).
Высокая прочность композиционных пластиков зависит от применяемых наполнителей (стеклоткани и стекловолокна, хлопчатобумажные ткани и волокна, металлическая сетка и проволока, волокна углерода и бора, нитевидные кристаллы и т.п.). Тип наполнителя зависит от требуемых свойств создаваемого материала. В отдельных случаях в состав пластика вводят пластификаторы и красители.
Как отмечалось ранее, в последние годы широкое применение находят углепластики. Они характеризуются низкой плотностью, высокими прочностными характеристиками и способностью выдерживать высокие температуры. Для получения особо термостойких КМ в качестве связующего используют углеродсодержащие термореактивные фенольные и фурфуриловые смолы, пеки из каменноугольной смолы или нефти. Армирующими материалами являются углеродные волокна, нити, жгуты и ткани. После предварительного формообразования заготовка подвергается высокотемпературной обработке (карбонизации). В процессе карбонизации происходит термодеструкция связующего, сопровождающаяся удалением испаряющихся смолистых соединений, газообразных продуктов и образованием твердого кокса с высоким содержанием углерода. По такой схеме получают углерод-углеродные КМ. Эти материалы являются наиболее перспективными для изготовления изделий, работающих при высоких температурах.
К основным способам изготовления деталей из композиционных пластиков относятся контактная формовка, автоклавная формовка, стирометод, вихревое напыление, центробежная формовка, намотка и др.
Контактной формовкой изготовляют крупногабаритные детали с наполнителями из стеклотканей, стекломатов и т.д. Применяют формы из дерева, гипса и легких сплавов. Форма должна точно воспроизводить наружный или внутренний контур детали.
Перед формовкой на рабочие поверхности формы наносят разделительный слой (поливиниловый спирт, нитролаки, целлофановую пленку и др.), предотвращающий прилипание связующего к поверхности формы. По разделительному слою наносят слой связующего, затем слой предварительно раскроенной ткани, которую тщательно прикатывают резиновым роликом к поверхности формы. Этим достигаются плотное прилегание ткани к поверхности формы, удаление пузырьков воздуха и равномерное пропитывание ткани связующим. Затем снова наносят связующее, ткань и т.д. до получения заданной толщины. Отверждение происходит при нормальной температуре в течение 5 - 50 ч в зависимости от вида связующего. Время отверждения сокращают увеличением температуры до 60 - 120°С. После отверждения готовую деталь извлекают из формы и в случае необходимости подвергают дальнейшей обработке (обрезке кромок, окраске и т.д.).
Особенности контактной формовки -простота оснастки и возможность получения деталей любых размеров и форм. Однако этот метод малопроизводителен, качество получаемых деталей недостаточно высокое из-за неравномерной укладки наполнителя и связующего. К нему предъявляют определенные требования по технике безопасности. Поэтому контактную формовку применяют в опытном и единичном производствах.
Автоклавную формовку применяют при выпуске деталей большими сериями. Форму с деталью накрывают резиновым чехлом и помещают в герметичный резервуар (автоклав). С помощью пара или воды в автоклаве создают определенное давление.
Стирометодом изготовляют крупногабаритные детали из композиционных пластиков с замкнутым полым профилем (полые рамы, диски, кронштейны и т.д.). На тонкостенный поливинилхлоридный чехол, размеры которого соответствуют размерам изготовляемой детали, наматывают волокно. Заготовку укладывают в разогретую до температуры 100 - 120°С пресс-форму. Под действием давления воздуха, разогретого внутри шланга, заготовка растягивается до размеров полости пресс-формы. В пространство между чехлом и пресс-формой за счет создания вакуума засасывается связующее.
Приведенные способы формовки используют в основном для изготовления деталей из пластиков с длинноволокнистыми наполнителями. При применении измельченных наполнителей процесс изготовления деталей удается механизировать. Наполнитель и связующее подают под давлением сжатого воздуха.
Вихревым напылением изготовляют крупногабаритные детали из стеклопластиков (кузова легковых и грузовых автомобилей, корпуса лодок, емкости и др.). Стекловолокно и смолу с отвердителем и ускорителем отверждения наносят на форму специальным пульверизатором. Смола смачивает стекловолокно в вихревом потоке, образованном сжатым воздухом. Стекловолокно со связующим, нанесенные на форму, вручную уплотняют роликом.
Высокой степенью механизации отличается напыление с помощью передвижной установки, в которой смонтированы режущее устройство для стекловолокна, вентилятор для подачи сжатого воздуха, распылитель и емкости для связующего, отвердителя и ускорителя. Стекловолокно разрезают на отдельные куски длиной 10 - 90 мм. Распылитель имеет три сопла: центральное для подачи стекловолокна и два боковых (одно служит для подачи связующего и отвердителя, другое - связующего и ускорителя отверждения). Смешение компонентов происходит на поверхности формы или перед нею в потоке сжатого воздуха.
Центробежной формовкой получают детали больших габаритных размеров, имеющие форму тел вращения, толщиной 2 - 15 мм, диаметром до 1 м и высотой до 3 м.
Стекловолокно и связующее равномерно подают во вращающуюся форму. После формовки в форму помещают резиновый мешок, с помощью которого создается давление на заготовку. В таком состоянии происходит отверждение композиции при определенной температуре.
Намоткой получают трубы и сложные по форме оболочки из композиционных пластиков. Основным элементом технологической оснастки является металлическая оправка, на которую перед намоткой укладывают пленку, облегчающую снятие изделия. При намотке оправка совершает вращательное и возвратно-поступательное движения. Волокно или тканевую ленту смачивают связующим. Отформованную заготовку покрывают защитной целлофановой пленкой и отправляют в камеру для отверждения.
Основной недостаток изготовления крупногабаритных деталей из пластиков -невысокая производительность труда, повышение которой возможно за счет механизации и автоматизации технологического процесса.
6. Изготовление резиновых технических деталей
6.1. Состав и свойства резиновых технических материалов
В производстве резиновых технических деталей основным видом сырья являются натуральные и синтетические каучуки. Натуральные каучуки не нашли широкого применения, так как сырьем для их получения является каучукосодержащий сок отдельных сортов растений. Сырьем для получения синтетических каучуков являются нефть, нефтепродукты, природный газ, древесина. Каучук в чистом виде в промышленности не применяют. Каучук превращают в резину вулканизацией. В качестве вулканизирующего вещества обычно используют серу. Количество серы определяет эластичность резиновых деталей. Например, мягкие резины содержат 1 - 3 % серы, твердые (эбонит) до 30% серы. Процесс вулканизации происходит под температурным воздействием (горячая вулканизация) или без температурного воздействия (холодная вулканизация). Для улучшения физико-механических и эксплуатационных свойств резиновых технических деталей и снижения расхода каучука в состав резиновых смесей вводят различные компоненты.
Наполнители уменьшают расход каучука, улучшают эксплуатационные свойства деталей. Наполнители подразделяют на порошкообразные и тканевые. В качестве порошкообразных наполнителей применяют сажу, тальк, мел и др. К тканевым наполнителям относят хлопчатобумажные, шелковые и другие ткани. В некоторых случаях для повышения прочности деталей их армируют стальной проволокой или сеткой, стеклянной или капроновой тканью. Количество наполнителя зависит от вида выпускаемых изделий.
Мягчители (парафин, стеариновая кислота, канифоль и др.) служат для облегчения процесса смешения резиновой смеси и обеспечения мягкости и морозоустойчивости. Для замедления процесса окисления в резиновые смеси добавляют противостарители (вазелины, ароматические амины и др.). Процесс вулканизации ускоряют введением в смесь оксида цинка, свинцового глета и др. Красители (охра, пятисернистая сурьма, ультрамарин и др.) вводят в смесь в количестве до 10% от массы каучука.
Высокая эластичность, способность к большим обратимым деформациям, стойкость к действию активных химических веществ, малые водо- и газопроводность, хорошие диэлектрические и другие свойства резины обусловили ее применение во всех отраслях народного хозяйства. В машиностроении применяют разнообразные резиновые технические детали:- ремни -для передачи вращательного движения с одного вала на другой; шланги и напорные рукава - для передачи жидкостей и газов под давлением; сальники, манжеты, прокладочные кольца и уплотнители - для уплотнения подвижных и неподвижных соединений; муфты, амортизаторы - для гашения динамических нагрузок; транспортерные ленты - для оснащения погрузочно-разгрузочных устройств и т.д.
6.2. Способы изготовления резиновых технических деталей
Технологический процесс изготовления резиновых технических деталей состоит из отдельных последовательных операций: приготовления резиновой смеси, формования и вулканизации. Процесс подготовки резиновой смеси заключается в смешении входящих в нее компонентов. Перед смешением каучук переводят в пластичное состояние многократным пропусканием его через специальные вальцы, предварительно подогретые до температуры 40 - 50 °С. Находясь в пластичном состоянии, каучук обладает способностью хорошо смешиваться с другими компонентами. Смешение проводят в червячных или валковых смесителях. Первым из компонентов при приготовлении смеси вводят противостаритель, последним - вулканизатор или ускоритель вулканизации.
Многие технологические процессы переработки резиновых композиций в детали (выдавливание, прессование, литье под давлением и др.) подобны тем, которые были рассмотрены при формообразовании деталей из пластмасс. Специфичным является лишь процесс получения листовых заготовок (каландрование).
Каландрование применяют для получения резиновых смесей в виде листов и прорезиненных лент, а также для соединения листов резины и прорезиненных лент (дублирование). Операцию выполняют на многовалковых машинах - каландрах. Валки каландров снабжают системой внутреннего обогрева или охлаждения, что позволяет регулировать температурный режим. Листы резины, полученные прокаткой на каландрах, сматывают в рулоны и используют затем в качестве полуфабриката для других процессов формообразования резиновых деталей. Во избежание слипания резины в рулонах ее посыпают тальком или мелом при выходе из каландра. В процессе получения прорезиненной ткани в зазор между валками каландров 3 (рис. 18) одновременно пропускают пластифицированную резиновую смесь 4 и ткань 2. Резиновая смесь поступает в зазор между верхним и средним валками, обволакивает средний валок и поступает в зазор между средним и нижним валками, через который проходит ткань. Средний валок вращается с большей скоростью, чем нижний. Разница скоростей обеспечивает втирание резиновой смеси в ткань. Толщину резиновой пленки на ткани регулируют, изменяя зазор между валками каландра. Многослойную прорезиненную ткань получают при пропускании определенного числа листов однослойной прорезиненной ткани через валки каландра. Полученную ткань наматывают на барабан 1 и затем вулканизируют.
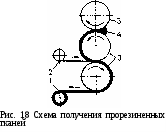
Непрерывное выдавливание используют для получения профилированных резиновых деталей (труб, прутков, профилей для остекления). Детали непрерывным выдавливанием изготовляют машинами червячного типа. Таким способом покрывают резиной металлическую проволоку.
Прессование является одним из основных способов получения фасонных деталей (манжет, уплотнительных колец, клиновых ремней и т.д.). Прессуют в металлических формах. Применяют горячее и холодное прессование. При горячем прессовании резиновую смесь закладывают в горячую пресс-форму и прессуют на гидравлических прессах с обогреваемыми плитами. Температура прессования 140 - 155 °С. При прессовании одновременно происходят формообразование и вулканизация деталей. Высокопрочные детали (например, клиновые ремни) после формования подвергают дополнительной вулканизации в специальных приспособлениях-пакетах. Холодным прессованием получают детали из эбонитовых смесей (корпуса аккумуляторных батарей, детали для химической промышленности и т.д.). После прессования заготовки отправляют на вулканизацию. В состав эбонитовой смеси входят каучук и значительное количество серы (до 30% от массы каучука). В качестве наполнителей применяют размельченные отходы эбонитового производства.
Литьем под давлением получают детали сложной формы. Резиновая смесь поступает под давлением при температуре 80 - 120°С через литниковое отверстие в литейную форму, что значительно сокращает цикл вулканизации.
Вулканизация является завершающей операцией при изготовлении резиновых деталей. Вулканизацию проводят в специальных камерах-вулканизаторах при температуре 120 - 150°С в атмосфере насыщенного водяного пара при небольших давлениях. В процессе вулканизации происходит химическая реакция серы и каучука, в результате которой линейная структура молекул каучука превращается в сетчатую, что уменьшает пластичность, повышает стойкость к действию органических растворителей, увеличивает механическую прочность.
При массовом производстве резиновых деталей все технологические операции выполняют с помощью высокопроизводительного и автоматизированного оборудования.