Файл: Физикотехнологические основы получения композиционных материалов.doc
ВУЗ: Не указан
Категория: Не указан
Дисциплина: Не указана
Добавлен: 07.11.2023
Просмотров: 289
Скачиваний: 4
СОДЕРЖАНИЕ
Физико-технологические основы получения композиционных материалов
1.1. Характеристика композиционных материалов
1.2. Классификация композиционных материалов
1.3. Требования, предъявляемые к армирующим и матричным материалам
Изготовление изделий из металлических композиционных материалов
2.3. Способы получения полуфабрикатов и готовых изделий
3.2. Краткая характеристика порошковых материалов
3.3. Приготовление смеси и формообразование заготовок
3.4. Спекание и окончательная обработка заготовок
4. Изготовление деталей из полимерных композиционных материалов
4.3. Способы формообразования деталей в высокоэластичном состоянии
5. Получение деталей из композиционных пластиков
7. Технологические особенности проектирования и изготовления деталей из композиционных материалов
7.1. Технологические требования к конструкциям изготовляемых деталей
7.2. Технологические особенности дополнительной механической обработки заготовок
Односторонним прессованием получают заготовки простой формы с отношением высоты к диаметру меньше единицы и заготовки типа втулок с отношением наружного диаметра к толщине стенки меньше трех.
Д
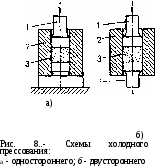
вустороннее прессование (рис. 8, б) применяют для формообразования заготовок сложной формы. В этом случае необходимое давление для получения равномерной плотности снижается на 30 - 40 %. Давление прессования зависит от заданной плотности, формы прессуемой заготовки, вида прессуемого порошка и других факторов. Использование вибрационного прессования позволяет в десятки раз уменьшить прилагаемое давление.
В процессе прессования частицы порошка подвергаются упругой и пластической деформации, в результате чего в заготовке накапливаются значительные напряжения. После извлечения заготовки из пресс-формы размеры ее увеличиваются в результате упругого последействия.
Режимы прессования, величина упругого последействия приведены в справочной литературе.
При горячем прессовании технологически совмещаются процессы формообразования и спекания заготовки. Температура горячего прессования составляет обычно 0,6 - 0,8 температуры плавления порошка для однокомпонентной системы, или ниже температуры плавления матричного материала композиции, в состав которой входят несколько компонентов. Благодаря нагреву процесс уплотнения протекает гораздо интенсивнее, чем при обычном прессовании. Это позволяет значительно уменьшить необходимое давление прессования. Методом горячего прессования можно получать материалы, характеризующиеся высокими прочностью, плотностью и однородностью структуры. Этот метод применяют для таких плохо прессуемых и плохо спекаемых композиций, как тугоплавкие металлоподобные соединения (карбиды, бориды, силициды).
Основная сложность горячего прессования заключается в выборе материала пресс-формы, который должен иметь достаточную прочность при температурах прессования, не реагировать с прессуемым порошком, быть дешевым. При температурах прессования 500 - 600°С в качестве материала применяют жаропрочные стали на основе никеля, при температурах 800 - 900°С - твердые сплавы. В случае более высоких температур прессования (до 2500 - 2600°С) единственным материалом для пресс-форм служит графит. Однако низкая производительность, малая стойкость пресс-форм (10 - 12 прессовок), необходимость проведения процесса в среде защитных газов ограничивают применение горячего прессования и обусловливают его использование только в тех случаях, когда другие методы порошковой металлургии не имеют успеха.
С целью повышения производительности процесса и увеличения стойкости пресс-форм в настоящее время проводят исследования и разрабатывают образцы промышленного оборудования, в которых нагрев осуществляется путем пропускания электрического тока непосредственно через прессуемый порошок.
Изостатическое (всестороннее) формование применяют для получения заготовок из композиций с порошковыми и волокнистыми наполнителями. Отсутствие потерь на внешнее трение и равномерность давления со всех сторон дают возможность получать необходимую плотность заготовок при давлениях, значительно меньших, чем при прессовании в закрытых пресс-формах.
В настоящее время применяют три основных вида изостатического формования.
-
Гидростатическое формование, при котором на порошок 3 (рис. 9), заключенный в эластичную оболочку 2, передается давление с помощью жидкости, находящейся в сосуде 1 высокого давления. В качестве рабочей жидкости используют масло, глицерин, воду и т.д. -
Ф
ормование с помощью толстостенной эластичной оболочки, вставленной в стальную пресс-форму, с целью получения крупногабаритных заготовок типа труб. Оболочка в данном случае изолирует порошок от стенок инструмента и служит средой, которая передает давление на прессуемые изделия. В качестве материала для оболочек используют парафин, воск, резину.
3. Горячее формование, позволяющее технологически совместить процессы формообразования и спекания. В качестве среды, передающей давление, применяют инертный газ, расплавленные металл или стекло. Прессуемую заготовку помещают в эластичную металлическую оболочку.
Прокатка - один из наиболее производительных и перспективных способов переработки порошковых материалов. Характерными особенностями являются высокая степень автоматизации и непрерывность процесса прокатки. Порошок (рис. 10, а) непрерывно поступает из бункера 1 в зазор между валками. При вращении валков 3 происходят обжатие и вытяжка порошка 2 в ленту или полосу 4 определенной толщины. Процесс прокатки может быть совмещен со спеканием и окончательной обработкой получаемых заготовок. В этом случае лента проходит через печь для спекания, а затем снова подвергается прокатке для получения листов заданных размеров. Ленты, идущие на приготовление фильтров и антифрикционных деталей, большей частью не подвергают дополнительной прокатке.
Число обжатий, необходимое для получения беспористой ленты, зависит от пластичности композиции и режимов прокатки. Технологически можно получать ленту из различных материалов (пористых, фрикционных, твердосплавных и др.). Применяя бункера с перегородкой (рис. 10, б), изготовляют ленты из разных материалов (двуслойные). Прокаткой получают ленты толщиной 0,02 - 3,0 мм и шириной до 300 мм. Применение валков определенной формы позволяет получать прутки различного профиля, в том числе и проволоку диаметром от 0,25 мм до нескольких миллиметров.
С
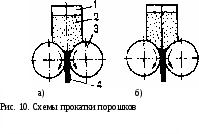
пособом выдавливания изготовляют прутки, трубы и профили различного сечения. Сущность процесса получения заготовок заключается в выдавливании порошка через калиброванное отверстие пресс-формы. В порошок добавляют пластификатор массой до 10 ... 12 % от массы порошка, улучшающий процесс соединения частиц и уменьшающий трение порошка о стенки пресс-формы. Профиль изготовляемого изделия зависит от формы калиброванного отверстия пресс-формы. Полые профили получают с применением рассекателя. В качестве оборудования используют механические и гидравлические прессы.
3.4. Спекание и окончательная обработка заготовок
Спекание проводят для повышения прочности предварительно полученных заготовок прессованием или прокаткой. В спрессованных заготовках доля контакта между отдельными частицами очень мала и спекание сопровождается ростом контактов между отдельными частицами порошка. Это является следствием протекания в спекаемом теле при нагреве следующих процессов: восстановления поверхностных оксидов, диффузии, рекристаллизации и др. Протекание этих процессов зависит от температуры и времени спекания, среды, в которой осуществляется спекание, и других факторов.
При спекании изменяются линейные размеры заготовки (большей частью наблюдается усадка - уменьшение размеров) и физико-механические свойства спеченных материалов. Температура спекания обычно составляет 0,6 - 0,9 температуры плавления порошка для однокомпонентной системы, или ниже температуры плавления материала матрицы для композиций, в состав которых входят несколько компонентов.
Время выдержки после достижения температуры спекания по всему сечению составляет 30 - 90 мин. Увеличение времени и температуры спекания до определенных значений способствует увеличению прочности и плотности в результате активизации процесса образования контактных поверхностей. Превышение указанных технологических параметров может привести к снижению прочности в результате роста зерен кристаллизации.
Проведение спекания в условиях, когда входящий в композицию легкоплавкий компонент образует при спекании жидкую фазу, активизирует усадку и обеспечивает получение заготовок с малой или даже нулевой пористостью, с высокими физико-механическими свойствами. С этой же целью, например, применяют пропитку тугоплавких материалов серебром или медью при производстве электроконтактных деталей.
К атмосфере спекания предъявляют требования безокислительного нагрева заготовок. В большинстве случаев спекание проводят в восстановительной атмосфере, способствующей удалению оксидов, или в вакууме. Для спекания используют электропечи сопротивления или печи с индукционным нагревом.
После спекания заготовки в ряде случаев подвергают дополнительной обработке в целях повышения физико-механических свойств, получения окончательных размеров и формы, нанесения декоративных покрытий и защиты поверхности детали от коррозии.
Для повышения физико-механических свойств спеченных заготовок применяют следующие виды обработки: повторные прессование и спекание, пропитку смазочными материалами (антифрикционных деталей), термическую или химико-термическую обработку.
Повторные прессование и спекание позволяют получать детали с более высокой плотностью. Промежуточные отжиги, снимая наклеп в зернах заготовки, способствуют дальнейшему их уплотнению при относительно небольшом давлении. Процесс повторного прессования осуществляют в тех же пресс-формах или в пресс-формах с повышенной точностью изготовления формообразующих деталей. В производственных условиях, как правило, ограничиваются двукратными прессованием и спеканием.
Спеченные материалы можно подвергать ковке, прокатке, штамповке при повышенных температурах. Обработка давлением позволяет снизить пористость материалов и повысить их пластичность.
Пропитку заготовок обычно выполняют погружением их в масляную ванну с температурой 70 - 140°С. Длительность пропитки колеблется от 15 мин до 2 ч. Степень заполнения пор при этом составляет 90 - 95%. Более высокое заполнение пор маслом достигается при применении вакуумной пропитки.
Основными видами термической обработки являются отжиг и закалка. Операцию отжига используют для повышения технологических свойств при производстве деталей из тугоплавких металлов. Отжиг снижает прочностные характеристики и в несколько раз повышает пластичность материала, что облегчает дальнейшую обработку давлением (ковку, протяжку, прокатку и т.д.). Наличие пор в материалах делает их чувствительными к окислению при нагреве и к коррозии при попадании закалочной жидкости в поры при закалке. В качестве охлаждающих сред необходимо выбирать жидкости, не представляющие опасности с точки зрения коррозии в процессе хранения и эксплуатации закаленных деталей.
В некоторых случаях детали из железного порошка подвергают науглероживанию методами химико-термической обработки - нагреву в ящиках с карбюризатором или в газовой науглероживающей атмосфере. Процесс насыщения углеродом протекает значительно быстрее вследствие проникания газов внутрь пористого тела.