Файл: 1. Конструктивные особенности лопаток турбины 5 Материалы, применяемые при изготовлении лопаток турбины 9.docx
Добавлен: 07.11.2023
Просмотров: 405
Скачиваний: 5
ВНИМАНИЕ! Если данный файл нарушает Ваши авторские права, то обязательно сообщите нам.
материалов является то, что расплавленные частицы порошка, деформируясь при ударе о поверхность детали, образуют структуру покрытия с минимальной пористостью. Как локальный источник нагрева, он в достаточной мере отвечает требованиям, которые накладывают на него металлургические и технологические свойства сплавов типа ЖС6У и особенности ремонтируемых деталей и узлов ГТД [12].
На заводе ММПП «Салют» (Москва, Россия) отработана технология восстановления титановых лопаток компрессора газовой турбины, имеющих местные повреждения, превышающие допустимые нормы [33]. Процесс заключается в приварке цилиндрических вкладышей, изготовленных из того же материала, что и лопатка. Поврежденный участок лопатки удаляют фрезерованием. Затем изготовляют вкладыш соответствующего диаметра и подгоняют по месту фрезерования пера лопатки. Вкладыш закрепляют на лопатке специальным приспособлением и вместе с лопаткой помещают в вакуумную камеру электронно-лучевой установки. Сварка проводится в условиях глубокого вакуума, рисунок 1.11 [12].
Сложность получения качественного сварного соединения с минимальными деформациями лопаток заключается в том, что лопатки имеют переменную толщину, при этом наиболее сложными участками являются входная и выходная кромки лопаток. Перегрев этих участков может вызвать нежелательные последствия, такие как провисание шва и коробление кромки. Во избежание подобного рода дефектов необходимо обеспечить равномерное
перемещение электронного луча по стыку и минимальную литую зону сварного соединения [12].
Рисунок 1.11. Схема проведения ремонта титановых рабочих лопаток компрессора газовой турбины с применением технологии электронно-лучевой сварки [12].
После сварки осуществляют визуальный контроль сварного шва, затем вкладыш отрезают параллельно кромке лопатки электроимпульсным способом, шлифуют и полируют с обеих сторон для получения нужного профиля. Далее проводят рентгеновский контроль сварного шва, термическую обработку в виде отпуска по стандартному режиму для снятия внутренних напряжений, окончательную полировку и виброгалтовку пера лопатки [12].
На фотографии ниже приведен еще один пример восстановительного ремонта лопатки компрессора из сплава титана, рисунок 1.12.
Рисунок 1.12. Лопатка из сплава Ti6Al4V с приваренной вставкой электронно-лучевым методом (Precision Technologies, Inc)
Для восстановления поверхности лопаток компрессора ГТД ряд авторов предлагают использовать технологию электронно-лучевой наплавки [34], [35]. Несмотря на преимущества данной технологии, схожие с преимуществами лазерной наплавки, способ имеет ограничения по габаритным размерам восстанавливаемых заготовок, зависящих от размеров вакуумной камеры, на создание вакуума в которой также требуется время [1].
Первый промышленный ремонт лопаток наземной турбины лазерной сваркой был проведен в 1994 году [36]. Был использован метод с подачей порошка, результаты оказались обнадёживающими.
Наиболее интересными являются работы, в которых приведён сравнительный анализ результатов ремонта лопаток с использованием различных технологий. Так в работе [37], автор описывает результаты восстановления лопаток турбостартера авиационного винтового двигателя НК-12МП, изготовленных методом литья из сплава ЖС6К (ТУ 1 -809-1025-98) с использованием технологий вакуумной пайки и импульсной лазерной
наплавки самофлюсующегося высокотемпературного припоя ВПР24 с дисперсностью 100-315 мкм, а также технологий аргонодуговой наплавки и импульсной лазерной наплавки сварочной проволоки ХН60ВТ. Результаты восстановления лопаток: их внешний вид и микроструктура - представлены на рисунке 1.13.
По результатам исследования микроструктуры, измерения твёрдости металла наплавленных слоёв и прилегающего к нему основного металла, а также с учётом коэффициента линейного расширения металла наплавленных валиков автор отдаёт предпочтение технологии импульсной лазерной наплавки самофлюсующегося припоя ВПР24. Выбор объясняется низкой дисперсностью структуры наплавленного металла, наивысшими значениями и равномерным распределением твёрдости наплавленных слоёв благодаря равномерному распределению упрочняющих интерметаллидов, а также высокой производительностью процесса.
Рисунок 1.13. Результаты восстановления лопаток турбостартера: а – аргонодуговая наплавка с присадочной проволокой ХН60ВТ; б – вакуумная печная пайка с припоем ВПр24;
в – лазерная импульсная наплавка с присадочной проволокой ХН60ВТ; г – лазерная импульсная порошковая наплавка с припоем ВПр24 [37].
Касательно других методов восстановления необходимо отметить, что технология аргонодуговой наплавки показала себя с наихудшей стороны из-за широкой ЗТВ, низкой производительности, а также низкой твёрдости наплавленного материала. При восстановлении лопаток с использованием технологии вакуумной пайки получена крупнодисперсная структура наплавленных слоёв, склонная к охрупчиванию из-за высокого содержания интерметаллидов. При импульсной лазерной наплавке с использованием присадочной проволоки ХН60ВТ отмечается наличие мелкодисперсной структуры с размерами зерна 3-6 мкм, а также низкие значения твёрдости наплавленного слоя и низкая производительность процесса.
Результаты исследования технологических характеристик слоёв, образованных при лазерной и аргонодуговой наплавке порошковых материалов на никелевой основе Inconel 625 и Rene 142 на подложку, в качестве которой также использовали никелевые сплавы C1023, Inconel 792, Rene 80, Rene 125, DS Rene 142, используемые при изготовлении лопаток ГТД, описаны в работе [38]. В качестве источника лазерного излучения использовали CО2-лазер фирмы Rofin Sinar мощностью 1 кВт. Авторы отмечают снижение сварочных деформаций, однородное распределение твёрдости как вдоль, так и поперёк наплавленного слоя, наличие переходной
зоны меньшей толщины, а также минимальное количество внутренних дефектов при лазерной наплавке.
Преимуществами технологии металлопорошковой лазерной наплавки перед технологиями аргонодуговой, плазменной и электронно-лучевой наплавки также являются минимальный припуск под последующую механическую обработку (около 100 мкм), узкая зона термического влияния (до 100 мкм), наличие мелкозернистой структуры наплавленного слоя, минимальный (локальный) энерговклад, увеличение ремонтной площади поверхности лопатки ГТД, отсутствие необходимости последующей термической обработки, а также повышенные механические характеристики наплавленного слоя [1], [39], [40].
В работе [40] также приведены результаты экспериментального исследования влияния времени воздействия и мощности лазерного излучения при наплавке порошка Stellite 6L на хромоникелевый сплав 12CrNi на структуру, твёрдость и долю участи основного металла в наплавленном слое. В качестве источника лазерного излучения использовали СО2-лазер. По результатам эксперимента авторы отметили увеличение твёрдости, уменьшение размера зерна структуры, а также снижение доли основного металла в наплавленном слое при снижении времени воздействия и мощности лазерного излучения.
Результаты обработки торца пера лопатки импульсной лазерной наплавкой, с использованием импульсно-периодического твердотельного Nd:YAG лазера, в составе лазерного комплекса HTS-Mobile 300 (ОКБ
«Булат»), представлены в работах [1], [41]. Подачу присадочной проволоки диаметром 0,4 мм в процессе наплавки осуществляли вручную. Наплавку выполняли с
-
Электронно-лучевые технологии ремонта лопаток
На заводе ММПП «Салют» (Москва, Россия) отработана технология восстановления титановых лопаток компрессора газовой турбины, имеющих местные повреждения, превышающие допустимые нормы [33]. Процесс заключается в приварке цилиндрических вкладышей, изготовленных из того же материала, что и лопатка. Поврежденный участок лопатки удаляют фрезерованием. Затем изготовляют вкладыш соответствующего диаметра и подгоняют по месту фрезерования пера лопатки. Вкладыш закрепляют на лопатке специальным приспособлением и вместе с лопаткой помещают в вакуумную камеру электронно-лучевой установки. Сварка проводится в условиях глубокого вакуума, рисунок 1.11 [12].
Сложность получения качественного сварного соединения с минимальными деформациями лопаток заключается в том, что лопатки имеют переменную толщину, при этом наиболее сложными участками являются входная и выходная кромки лопаток. Перегрев этих участков может вызвать нежелательные последствия, такие как провисание шва и коробление кромки. Во избежание подобного рода дефектов необходимо обеспечить равномерное
перемещение электронного луча по стыку и минимальную литую зону сварного соединения [12].
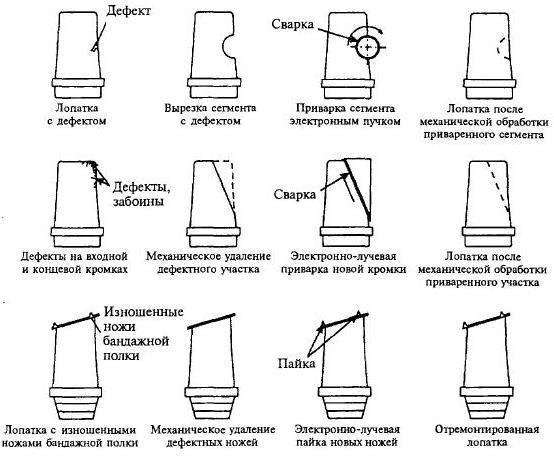
Рисунок 1.11. Схема проведения ремонта титановых рабочих лопаток компрессора газовой турбины с применением технологии электронно-лучевой сварки [12].
После сварки осуществляют визуальный контроль сварного шва, затем вкладыш отрезают параллельно кромке лопатки электроимпульсным способом, шлифуют и полируют с обеих сторон для получения нужного профиля. Далее проводят рентгеновский контроль сварного шва, термическую обработку в виде отпуска по стандартному режиму для снятия внутренних напряжений, окончательную полировку и виброгалтовку пера лопатки [12].
На фотографии ниже приведен еще один пример восстановительного ремонта лопатки компрессора из сплава титана, рисунок 1.12.
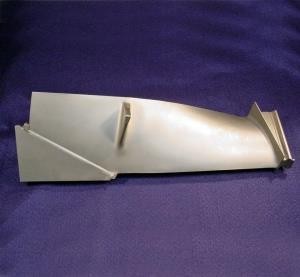
Рисунок 1.12. Лопатка из сплава Ti6Al4V с приваренной вставкой электронно-лучевым методом (Precision Technologies, Inc)
Для восстановления поверхности лопаток компрессора ГТД ряд авторов предлагают использовать технологию электронно-лучевой наплавки [34], [35]. Несмотря на преимущества данной технологии, схожие с преимуществами лазерной наплавки, способ имеет ограничения по габаритным размерам восстанавливаемых заготовок, зависящих от размеров вакуумной камеры, на создание вакуума в которой также требуется время [1].
4.6. Лазерные технологии ремонта лопаток
Первый промышленный ремонт лопаток наземной турбины лазерной сваркой был проведен в 1994 году [36]. Был использован метод с подачей порошка, результаты оказались обнадёживающими.
Наиболее интересными являются работы, в которых приведён сравнительный анализ результатов ремонта лопаток с использованием различных технологий. Так в работе [37], автор описывает результаты восстановления лопаток турбостартера авиационного винтового двигателя НК-12МП, изготовленных методом литья из сплава ЖС6К (ТУ 1 -809-1025-98) с использованием технологий вакуумной пайки и импульсной лазерной
наплавки самофлюсующегося высокотемпературного припоя ВПР24 с дисперсностью 100-315 мкм, а также технологий аргонодуговой наплавки и импульсной лазерной наплавки сварочной проволоки ХН60ВТ. Результаты восстановления лопаток: их внешний вид и микроструктура - представлены на рисунке 1.13.
По результатам исследования микроструктуры, измерения твёрдости металла наплавленных слоёв и прилегающего к нему основного металла, а также с учётом коэффициента линейного расширения металла наплавленных валиков автор отдаёт предпочтение технологии импульсной лазерной наплавки самофлюсующегося припоя ВПР24. Выбор объясняется низкой дисперсностью структуры наплавленного металла, наивысшими значениями и равномерным распределением твёрдости наплавленных слоёв благодаря равномерному распределению упрочняющих интерметаллидов, а также высокой производительностью процесса.
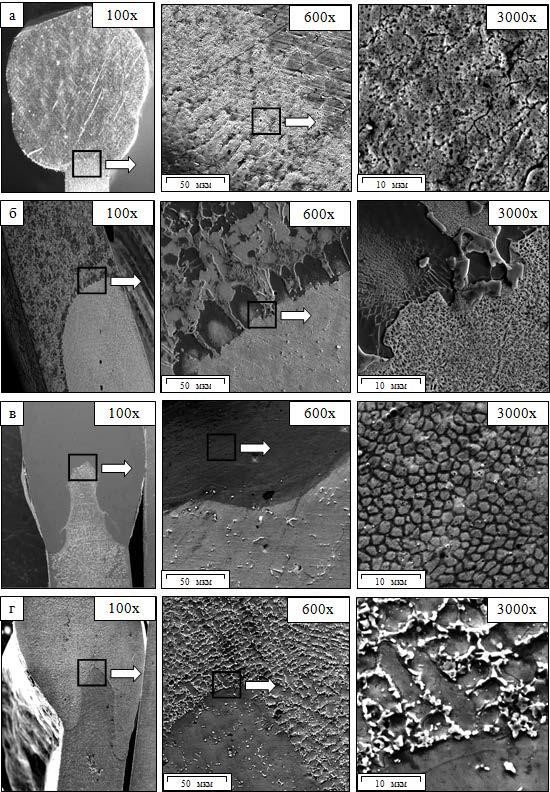
Рисунок 1.13. Результаты восстановления лопаток турбостартера: а – аргонодуговая наплавка с присадочной проволокой ХН60ВТ; б – вакуумная печная пайка с припоем ВПр24;
в – лазерная импульсная наплавка с присадочной проволокой ХН60ВТ; г – лазерная импульсная порошковая наплавка с припоем ВПр24 [37].
Касательно других методов восстановления необходимо отметить, что технология аргонодуговой наплавки показала себя с наихудшей стороны из-за широкой ЗТВ, низкой производительности, а также низкой твёрдости наплавленного материала. При восстановлении лопаток с использованием технологии вакуумной пайки получена крупнодисперсная структура наплавленных слоёв, склонная к охрупчиванию из-за высокого содержания интерметаллидов. При импульсной лазерной наплавке с использованием присадочной проволоки ХН60ВТ отмечается наличие мелкодисперсной структуры с размерами зерна 3-6 мкм, а также низкие значения твёрдости наплавленного слоя и низкая производительность процесса.
Результаты исследования технологических характеристик слоёв, образованных при лазерной и аргонодуговой наплавке порошковых материалов на никелевой основе Inconel 625 и Rene 142 на подложку, в качестве которой также использовали никелевые сплавы C1023, Inconel 792, Rene 80, Rene 125, DS Rene 142, используемые при изготовлении лопаток ГТД, описаны в работе [38]. В качестве источника лазерного излучения использовали CО2-лазер фирмы Rofin Sinar мощностью 1 кВт. Авторы отмечают снижение сварочных деформаций, однородное распределение твёрдости как вдоль, так и поперёк наплавленного слоя, наличие переходной
зоны меньшей толщины, а также минимальное количество внутренних дефектов при лазерной наплавке.
Преимуществами технологии металлопорошковой лазерной наплавки перед технологиями аргонодуговой, плазменной и электронно-лучевой наплавки также являются минимальный припуск под последующую механическую обработку (около 100 мкм), узкая зона термического влияния (до 100 мкм), наличие мелкозернистой структуры наплавленного слоя, минимальный (локальный) энерговклад, увеличение ремонтной площади поверхности лопатки ГТД, отсутствие необходимости последующей термической обработки, а также повышенные механические характеристики наплавленного слоя [1], [39], [40].
В работе [40] также приведены результаты экспериментального исследования влияния времени воздействия и мощности лазерного излучения при наплавке порошка Stellite 6L на хромоникелевый сплав 12CrNi на структуру, твёрдость и долю участи основного металла в наплавленном слое. В качестве источника лазерного излучения использовали СО2-лазер. По результатам эксперимента авторы отметили увеличение твёрдости, уменьшение размера зерна структуры, а также снижение доли основного металла в наплавленном слое при снижении времени воздействия и мощности лазерного излучения.
Результаты обработки торца пера лопатки импульсной лазерной наплавкой, с использованием импульсно-периодического твердотельного Nd:YAG лазера, в составе лазерного комплекса HTS-Mobile 300 (ОКБ
«Булат»), представлены в работах [1], [41]. Подачу присадочной проволоки диаметром 0,4 мм в процессе наплавки осуществляли вручную. Наплавку выполняли с