Файл: 1. Конструктивные особенности лопаток турбины 5 Материалы, применяемые при изготовлении лопаток турбины 9.docx
Добавлен: 07.11.2023
Просмотров: 411
Скачиваний: 5
ВНИМАНИЕ! Если данный файл нарушает Ваши авторские права, то обязательно сообщите нам.
присадочного материала применяли сферический порошок гранулометрического состава 45–75 мкм, полученный методом газоструйного распыления заготовки из материала Ti6Al4V в среде инертного газа [49]. Металлографические исследования показали наличие чёткой границы раздела основного и наплавленного металла, отсутствие внутренних дефектов и наличие мелкоигольчатой структуры наплавленного слоя, свидетельствующей о высоких скоростях охлаждения. К преимуществам используемого метода авторы относят, в том числе, его адаптивность, что актуально для различно изношенных поверхностей лопаток. В качестве недостатков можно указать на использование импортного оборудования [1].
Результаты лазерного восстановления лопаток из сплава Inconel 738 для газоперекачивающих станций с применением присадочных порошков на никелевой основе Inconel 625 и Inconel 738, приведены в работе [50]. В качестве источника лазерного излучения использовали твердотельный лазер с длиной волны 1,07 мкм. В обоих вариантах получены качественные валики, при этом в случае использования материала Inconel 738 дополнительно применяли последующую термическую обработку зоны наплавки, позволившую получить наплавленные слои равнопрочные с ОМ. При использовании порошка
Inconel 625 механические характеристики наплавленных слоёв отличались меньшими значениями прочностных характеристик по сравнению с ОМ. Также авторы отмечают преимущества использования волоконного лазера перед СО2-лазером благодаря лучшему поглощению излучения материалом и простоте доставки лазерного луча в зону обработки [1].
Результаты исследования возможности использования установки LENS 850R (Optomec) для устранения дефектов, образованных при литье и ремонта компонентов авиационных двигателей, изготовленных из сплавов на
никелевой основе (718 и Waspaloy), описаны в работе [51]. В рамках экспериментальных исследований в качестве присадочного материала использовали порошки с одноимёнными названиями. Наплавку осуществляли при варьирования мощности лазерного излучения в диапазоне 150-990 Вт, диаметра пятна лазерного излучения - 0,69 до 2 мм и скорости наплавки - 0,15 до 1,5 м/мин. По результатам исследований в случае использования сплава 718 были получены качественные валики с высокой технологической прочностью и незначительным количеством пор. При лазерной наплавке сплава Waspaloy, чувствительного к трещинообразованию, качественные наплавленные слои были получены при минимальном значении погонной энергии.
Chromalloy HIT and Siemens-Westinghouse Power Corporation создали исследовательскую группу по отработке методов лазерной наплавки сварки IN738 и направленно кристаллизовавшегося сплава Mar-M002 [52]. Использовались достаточно высокие температуры предварительного нагрева
(9000С). Испытания показали минимальный уровень пористости; уровень усталостной прочности равнялся 70-80% данного показателя ОМ.
EPRI Repair & Replacement Applications Center (RRAC) провели двухгодичное исследование по применению ремонтной технологии лазерной сварки для сплава IN738 [53]. Использовались присадочные материалы – IN625, IN738, IN939. Удачные результаты были достигнуты с IN625 и IN939. Свободное от трещин сварное соединение с применением IN738 как присадочного материала было также получено, но уровень твердости не соответствовал требованиям. IN625 использовался только для того, чтобы продемонстрировать возможность применения процесса лазерной сварки для γ'- упрочненных сплавов. В ходе исследований было установлено, что IN939 может быть нанесен на IN738 без образования трещин. Прочность соединения составляла 80 процентов от прочности основного материала. Ремонтная технология восстановления лопаток из сплава IN738 с применением присадочного материала IN939 была коммерциализирована в 2001 году.
Honeywell Laser Technology Services использует порошковую лазерную наплавку для ремонта IN738LC [54]. В качестве присадочного материала используется материал, схожий по составу с ОМ. В соединении отсутствуют поры и трещины, оно обладает удовлетворительной прочностью, малой зоной проплавления и узкой зоной термического влияния. Этот процесс также применяется для наземных турбин.
В рамках восстановления рабочих монокристаллических лопаток ГТД, изготовленных из литейного жаропрочного сплава на никелевой основе CMSX-4, были проведены исследования влияния скорости кристаллизации
на схему роста кристаллов наплавленных слоёв [55]. Лазерную наплавку порошка идентичного химического состава с дисперсностью 25-75 мкм выполняли с использованием диодного лазера с длиной волны 940-980 нм, максимальной выходной мощностью 680 Вт и диаметром пятна 0,86 мм. Скорость кристаллизации расплава сохраняли в требуемом диапазоне с помощью индуктора мощностью 3 кВт с динамическим контролем частоты от
70 до 450 кГц и пропорционально-интегрально-дифференцирующего регулятора температуры ванны расплава, регулирующего мощность лазерного излучения. Лопатку располагали на водоохлаждаемом основании с температурой 18°С. В результате проведённых исследований были получены наплавленные слои без внутренних дефектов, пор и трещин, с эпитаксиальной кристаллизацией. Схожие результаты восстановления лопаток из монокристаллитного никелевого сплава NiCrAlY описаны в работе [56].
Интересен также опыт контроля температуры ванны расплава в процессе лазерной наплавки [57]. При восстановлении лопаток, изготовленных из никелевого сплава, использовали порошок идентичного состава дисперсностью 45-105 мкм, перемещение коаксиальной лазерной наплавочной головки осуществляли манипулятором на базе 4-х осевой установки с ЧПУ-управлением. В качестве источника лазерного излучения
использовали твердотельный Nd:YAG лазер (HL3006D) непрерывной
генерации электромагнитного излучения оптического диапазона с максимальной мощностью 3 кВт.
Контроль геометрии наплавленных слоёв осуществляли с помощью регулирования температуры ванны расплава. С этой целью была изготовлена система контроля, состоящая из германиевого фотодиода и ПИД-регулятора температуры ванны расплава. Фотодиод, интегрированный в лазерную наплавочную головку, принимал электромагнитные волны, исходящие от ванны расплава, в диапазоне длин 1300-1600 нм.
Лазерную наплавку осуществляли при мощности лазерного излучения 300 Вт, скорости перемещения 500 мм/мин и массой подаваемого порошка 1,5 г/мин.
Основная технологическая проблема, возникшая при ремонте гребешков бандажной полки лопатки, и для устранения которой авторы изготовили систему контроля температуры ванны расплава, – низкая технологическая прочность (рисунок 1.21в) по причине образования легкоплавких эвтектик по границам зёрен, а также увеличение поперечного сечения в начале и конце наплавленных слоёв (рисунок 1.21б).
ИК-температурный и
лазерный сигналы, В
Рисунок 1.21. Восстановление гребешка бандажной полки лопатки без контроля температуры ванны расплава: а – результаты измерения температуры ванны расплава в ИК-диапазоне при постоянном сигнале ПИД-регулятора источнику лазерного излучения (Р = 300Вт); б – скос и увеличение поперечного сечения наплавленных слоёв; в – трещинообразование в наплавленных слоях [57].
Для устранения возникших технологических
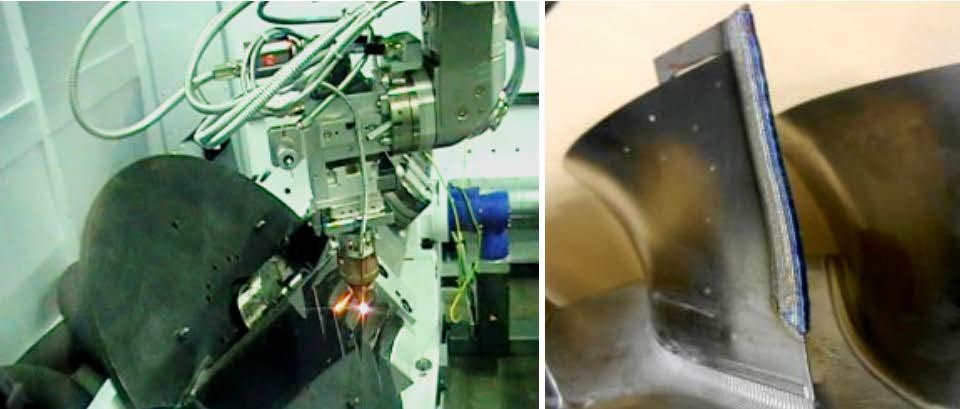
а) | б) |
Рисунок 1.20. Процесс восстановления входной кромки лопатки ГТД: а - восстановление входной кромки; б - сектора моноколеса. |
Результаты лазерного восстановления лопаток из сплава Inconel 738 для газоперекачивающих станций с применением присадочных порошков на никелевой основе Inconel 625 и Inconel 738, приведены в работе [50]. В качестве источника лазерного излучения использовали твердотельный лазер с длиной волны 1,07 мкм. В обоих вариантах получены качественные валики, при этом в случае использования материала Inconel 738 дополнительно применяли последующую термическую обработку зоны наплавки, позволившую получить наплавленные слои равнопрочные с ОМ. При использовании порошка
Inconel 625 механические характеристики наплавленных слоёв отличались меньшими значениями прочностных характеристик по сравнению с ОМ. Также авторы отмечают преимущества использования волоконного лазера перед СО2-лазером благодаря лучшему поглощению излучения материалом и простоте доставки лазерного луча в зону обработки [1].
Результаты исследования возможности использования установки LENS 850R (Optomec) для устранения дефектов, образованных при литье и ремонта компонентов авиационных двигателей, изготовленных из сплавов на
никелевой основе (718 и Waspaloy), описаны в работе [51]. В рамках экспериментальных исследований в качестве присадочного материала использовали порошки с одноимёнными названиями. Наплавку осуществляли при варьирования мощности лазерного излучения в диапазоне 150-990 Вт, диаметра пятна лазерного излучения - 0,69 до 2 мм и скорости наплавки - 0,15 до 1,5 м/мин. По результатам исследований в случае использования сплава 718 были получены качественные валики с высокой технологической прочностью и незначительным количеством пор. При лазерной наплавке сплава Waspaloy, чувствительного к трещинообразованию, качественные наплавленные слои были получены при минимальном значении погонной энергии.
Chromalloy HIT and Siemens-Westinghouse Power Corporation создали исследовательскую группу по отработке методов лазерной наплавки сварки IN738 и направленно кристаллизовавшегося сплава Mar-M002 [52]. Использовались достаточно высокие температуры предварительного нагрева
(9000С). Испытания показали минимальный уровень пористости; уровень усталостной прочности равнялся 70-80% данного показателя ОМ.
EPRI Repair & Replacement Applications Center (RRAC) провели двухгодичное исследование по применению ремонтной технологии лазерной сварки для сплава IN738 [53]. Использовались присадочные материалы – IN625, IN738, IN939. Удачные результаты были достигнуты с IN625 и IN939. Свободное от трещин сварное соединение с применением IN738 как присадочного материала было также получено, но уровень твердости не соответствовал требованиям. IN625 использовался только для того, чтобы продемонстрировать возможность применения процесса лазерной сварки для γ'- упрочненных сплавов. В ходе исследований было установлено, что IN939 может быть нанесен на IN738 без образования трещин. Прочность соединения составляла 80 процентов от прочности основного материала. Ремонтная технология восстановления лопаток из сплава IN738 с применением присадочного материала IN939 была коммерциализирована в 2001 году.
Honeywell Laser Technology Services использует порошковую лазерную наплавку для ремонта IN738LC [54]. В качестве присадочного материала используется материал, схожий по составу с ОМ. В соединении отсутствуют поры и трещины, оно обладает удовлетворительной прочностью, малой зоной проплавления и узкой зоной термического влияния. Этот процесс также применяется для наземных турбин.
В рамках восстановления рабочих монокристаллических лопаток ГТД, изготовленных из литейного жаропрочного сплава на никелевой основе CMSX-4, были проведены исследования влияния скорости кристаллизации
на схему роста кристаллов наплавленных слоёв [55]. Лазерную наплавку порошка идентичного химического состава с дисперсностью 25-75 мкм выполняли с использованием диодного лазера с длиной волны 940-980 нм, максимальной выходной мощностью 680 Вт и диаметром пятна 0,86 мм. Скорость кристаллизации расплава сохраняли в требуемом диапазоне с помощью индуктора мощностью 3 кВт с динамическим контролем частоты от
70 до 450 кГц и пропорционально-интегрально-дифференцирующего регулятора температуры ванны расплава, регулирующего мощность лазерного излучения. Лопатку располагали на водоохлаждаемом основании с температурой 18°С. В результате проведённых исследований были получены наплавленные слои без внутренних дефектов, пор и трещин, с эпитаксиальной кристаллизацией. Схожие результаты восстановления лопаток из монокристаллитного никелевого сплава NiCrAlY описаны в работе [56].
Интересен также опыт контроля температуры ванны расплава в процессе лазерной наплавки [57]. При восстановлении лопаток, изготовленных из никелевого сплава, использовали порошок идентичного состава дисперсностью 45-105 мкм, перемещение коаксиальной лазерной наплавочной головки осуществляли манипулятором на базе 4-х осевой установки с ЧПУ-управлением. В качестве источника лазерного излучения
использовали твердотельный Nd:YAG лазер (HL3006D) непрерывной
генерации электромагнитного излучения оптического диапазона с максимальной мощностью 3 кВт.
Контроль геометрии наплавленных слоёв осуществляли с помощью регулирования температуры ванны расплава. С этой целью была изготовлена система контроля, состоящая из германиевого фотодиода и ПИД-регулятора температуры ванны расплава. Фотодиод, интегрированный в лазерную наплавочную головку, принимал электромагнитные волны, исходящие от ванны расплава, в диапазоне длин 1300-1600 нм.
Лазерную наплавку осуществляли при мощности лазерного излучения 300 Вт, скорости перемещения 500 мм/мин и массой подаваемого порошка 1,5 г/мин.
Основная технологическая проблема, возникшая при ремонте гребешков бандажной полки лопатки, и для устранения которой авторы изготовили систему контроля температуры ванны расплава, – низкая технологическая прочность (рисунок 1.21в) по причине образования легкоплавких эвтектик по границам зёрен, а также увеличение поперечного сечения в начале и конце наплавленных слоёв (рисунок 1.21б).


ИК-температурный и
лазерный сигналы, В
Рисунок 1.21. Восстановление гребешка бандажной полки лопатки без контроля температуры ванны расплава: а – результаты измерения температуры ванны расплава в ИК-диапазоне при постоянном сигнале ПИД-регулятора источнику лазерного излучения (Р = 300Вт); б – скос и увеличение поперечного сечения наплавленных слоёв; в – трещинообразование в наплавленных слоях [57].
Для устранения возникших технологических