ВУЗ: Не указан
Категория: Не указан
Дисциплина: Не указана
Добавлен: 09.11.2023
Просмотров: 101
Скачиваний: 2
СОДЕРЖАНИЕ
Описание конструкции оборудования и принцип действия оборудования
Производственный цикл в котором участвует обрабатывающий центр Integrex 300-IV ST
Перечень документов для проведения ремонтных работ.
Предварительная дефектная ведомость :
Технология ремонта оборудования.
Наименование и краткая характеристика выявленных дефектов зубчатого колеса.
Термическая обработка закалка и отпуск
Наименование и краткая характеристика выявленных дефектов вала
РЕГУЛЯРНЫЙ ОСМОТР И ТЕХНИЧЕСКОЕ ОБСЛУЖИВАНИЕ
Список мероприятий технического осмотра:
Осмотр во время работы (после подачи питания)
Еженедельный техосмотр или через 60 часов работы
Раз в полгода или через 1500 часов работы
Ежегодный или через 3000 часов работы
Соблюдение правил ТБ при проведении технического обслуживания
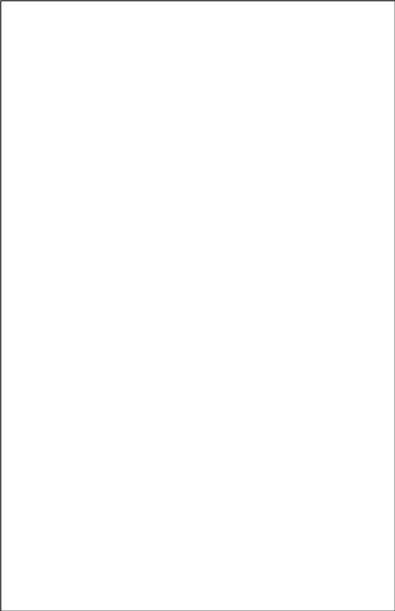
МИНИСТЕРСТВО ОБРАЗОВАНИЯ И НАУКИ ПЕРМСКОГО КРАЯ
государственное бюджетное профессиональное образовательное учреждение
«Пермский химико-технологический техникум»
(ГБПОУ «ПХТТ»)
МИНИСТЕРСТВО ОБРАЗОВАНИЯ И НАУКИ ПЕРМСКОГО КРАЯ
государственное бюджетное профессиональное образовательное учреждение
«Пермский химико-технологический техникум»
(ГБПОУ «ПХТТ»)
КУРСОВАЯ РАБОТА
| Работу выполнил: Специальность: 15.02.12 «Монтаж техническое обслуживание и ремонт промышленного оборудования» Руководитель: |
Пермь 2023
Оглавление
1
Введение. 7
Описание конструкции оборудования и принцип действия оборудования 10
Принцип работы 13
Производственный цикл в котором участвует обрабатывающий центр Integrex 300-IV ST 16
Техническое обслуживание и планово-предупредительный ремонт проектируемого оборудования. 17
Перечень быстро изнашиваемых узлов оборудования 17
Смазка станка 18
Организация ремонтных работ. 22
Перечень документов для проведения ремонтных работ. 23
Приём оборудования в ремонт 27
Дефектная ведомость 28
Предварительная дефектная ведомость : 30
Рабочая дефектная ведомость : 32
должна ясно показывать, какие детали и в какой последовательности по узлам заменяются новыми: Указываются способы сочленения старых деталей с новыми. В ней должны быть перечислены все работы вплоть до снятия станка с фундамента, разборки, транспортировки в ремонтный цех и всех сопутствующих работ, ремонта всех ограждений и кожухов, испытания на стенде и на производстве, монтажа на месте после ремонта с установкой электропроводки и сдачей станка ОТК и цеху. 32
Технология ремонта оборудования. 33
Наименование и краткая характеристика выявленных дефектов зубчатого колеса. 36
Наплавка 37
Термическая обработка отжиг 40
Зубофрезерование. 41
Термическая обработка закалка и отпуск 42
Контрольно-измерительная 45
Наименование и краткая характеристика выявленных дефектов вала 46
Токарная обработка 47
Наплавка 48
Токарная обработка 50
Шлифовка 51
Контрольно-измерительная 52
Монтаж оборудования. 53
Меры предосторожности при установке станка 54
Порядок подъема станка. 55
Выбор и расчет грузовых строп для перемещения грузов. 58
Перемещение станка в цеху. 62
Установка станка 64
РЕГУЛЯРНЫЙ ОСМОТР И ТЕХНИЧЕСКОЕ ОБСЛУЖИВАНИЕ 67
Список мероприятий технического осмотра: 68
Ежедневный техосмотр 68
Осмотр во время работы (после подачи питания) 69
Осмотр по окончании работы 70
Еженедельный техосмотр или через 60 часов работы 70
Раз в полгода или через 1500 часов работы 71
Ежегодный или через 3000 часов работы 72
Соблюдение правил ТБ при проведении технического обслуживания 73
Заключение 77
Введение.
Металлорежущие станки являются основным видом заводского оборудования, предназначенного для производства всех современных машин, приборов, инструментов и других изделий, поэтому количество металлорежущих станков, их технический уровень в значительной степени характеризует производственную мощность страны.
Существенное место занимает ускорение научно-технического прогресса на базе технического перевооружения производства, создание высокопроизводительных машин и оборудования большой единичной мощности, внедрение новой техники и материалов, прогрессивной технологии и систем машин для комплексной механизации и автоматизации производства.
Ведущее место в дальнейшем росте экономики страны принадлежит отраслям машиностроения, которые обеспечивают материальную основу технического прогресса всех отраслей народного хозяйства.
Разработка новых синтетических сверхтвёрдых инструментальных материалов позволило расширить не только диапазон режимов резания, но и спектр обрабатываемых материалов. Повышение точности станков было достигнуто введением в их конструкцию узлов, реализующих новые принципы (например, использование бесконтактных измерительных систем).
В настоящее время развитие станкостроительной отрасли идёт в направлении повышения производительности металлорежущих станков, их надёжности и точности на базе применения автоматизированных процессов, унифицированных станочных модулей, роботизированных технологических комплексов и вычислительной техники.
Современные станки проектируют и изготовляют по особым законам, обеспечивающим в первую очередь универсальность принятия такого оборудования в производстве. Аналогичные закономерности лежат в основе создания специальных станков.
Станочное оборудование обладает такими замечательными качествами, как универсальность, мощность, точность, быстроходность, прочность. Каждое из таких качеств оценивается соответствующим расчетом.
Металлорежущий станок – важнейшая составная часть технологической системы. Вместе с совершенствованием станков становятся более совершенными и другие части системы: инструменты, приспособления и собственно заготовки. При этом в равной степени в технологических системах используют механические элементы, электронику, гидравлику, пневматику и их разнообразные сочетания.
Всё большее внимание обращают на достижение высокого качества изделий, которое многократно контролируют в ходе обработки и сборки. Современные станки могут иметь столь совершенные конструкции, что способны контролировать свою деятельность. Логичным продолжением развития современных металлорежущих станков является их объединение в соответствующие системы. Такие системы, как правило, работают автоматически.
Проблемой рациональной организаций ремонта технического оборудования тесно связано со сферой производства машин, как и со сферой ремонта.
Ремонт машин должен восстанавливать их производительность и
первоначальную точность, но и обеспечивать длительную работу.
Служба ремонта технического оборудования машиностроительного
предприятия – это комплекс подразделений, занимающихся надзором за
эксплуатацией и ремонтом технического оборудования.
Основными задачами этой службы является:
-
Обеспечение нормального технического состояния технического
оборудования и его бесперебойной работы;
-
Сокращение простоя оборудования в ремонте и потерь в производстве, связанных с выполнением ремонтных работ; -
снижение расходов на ремонт
Описание конструкции оборудования и принцип действия оборудования
Новейшие токарные центры с ЧПУ мирового класса объединяют в себе передовые технологии, высокую производительность и качество, отвечающие нуждам абсолютно любого заказчика. Широкое разнообразие доступных технических характеристик – от 2-х до 4-х осевых моделей до токарных центров с ЧПУ, оборудованных вторым шпинделем и приводным инструментом, позволяют осуществить обработку детали за один установ.
Серия INTEGREX – наиболее широко используемые многоцелевые станки в мире. Станки данной серии 4-го поколения отличаются большим количеством инноваций. Возможность многоцелевой обработки на станках серии INTEGREX IV позволяет полностью завершить процесс обработки (от исходной заготовки до готовой детали) за одну установку.
Таблица 1 - Технические характеристики станка Integrex 300-IV-ST:
Параметр | Значение |
Размер патрона | 10-дюймовый |
Максимальный обрабатываемый диаметр (верхняя/нижняя головка) | 760 мм / 420 мм |
Перемещение по осям X/Y/Z/B (верхняя головка) | 630/230/1585 мм/225° |
Перемещение по осям Х2/Z2 | 230/15030 мм |
Главный шпиндель | 4000 об/мин / 30 кВт перем.тока (40 л.с) |
Второй шпиндель (при 30-мин. цикле) | 4000 об/мин / 26 кВт перем. тока (35 л. с.) |
Фрезерный шпиндель | 12 000 об/мин / 18.5 кВт перем.тока (25 л.с) |
| |
Продолжение таблицы 1
Кол-во одновременно управляемых координат станка (осей) | 5 |
Привод исполнительного звена станка (тип) | Шарико-винтовая пара (ШВП) |
Расстояние между центрами станка - РМЦ, мм | 0.70...4.16 мм/об |
Максимальная длина заготовки (ДО), мм | 1 550 |
Требуемая площадь | 5110 x2479 мм |
Масса | 12000 кг. |
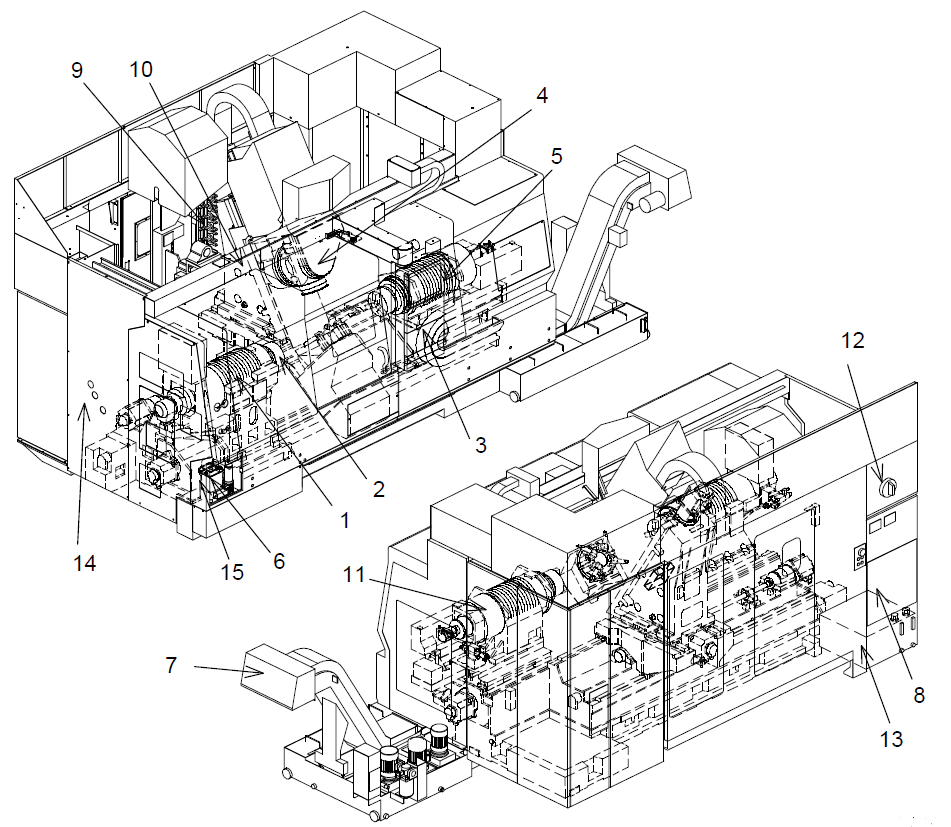
Рисунок 1 – общий вид Integrex 300-IV ST
Таблица 2 – главные узлы станка
№ | Наименование детали |
1 | Передняя бабка |
2 | Зажимной патрон |
3 | Пульт управления |
4 | Фрезерная головка |
5 | Задняя бабка или контршпиндель |
6 | Маслобак |
7 | Транспортер для сбора стружки (поставляется по специальному заказу) |
8 | Контроллер комбинированного блока смазки и управления (гидростанция) |
9 | Инструментальный магазин |
10 | Устройство автоматической смены инструмента (АСИ) |
11 | Электрошкаф |
12 | Главный рубильник |
13 | Бак СОЖ |
14 | Пневмоблок |
15 | Бак для консистентной смазки |