ВУЗ: Не указан
Категория: Не указан
Дисциплина: Не указана
Добавлен: 09.11.2023
Просмотров: 110
Скачиваний: 2
СОДЕРЖАНИЕ
Описание конструкции оборудования и принцип действия оборудования
Производственный цикл в котором участвует обрабатывающий центр Integrex 300-IV ST
Перечень документов для проведения ремонтных работ.
Предварительная дефектная ведомость :
Технология ремонта оборудования.
Наименование и краткая характеристика выявленных дефектов зубчатого колеса.
Термическая обработка закалка и отпуск
Наименование и краткая характеристика выявленных дефектов вала
РЕГУЛЯРНЫЙ ОСМОТР И ТЕХНИЧЕСКОЕ ОБСЛУЖИВАНИЕ
Список мероприятий технического осмотра:
Осмотр во время работы (после подачи питания)
Еженедельный техосмотр или через 60 часов работы
Раз в полгода или через 1500 часов работы
Ежегодный или через 3000 часов работы
Соблюдение правил ТБ при проведении технического обслуживания
Контрольно-измерительная
После проведения восстановительных операций зубчатого колеса, проведем контрольные замеры всех ремонтируемых частей детали.
При контроле зубчатого колеса используем штанген инструмент.
В итоге получили следующие размеры:
1. Ширина зубчатых колес (поверхность А) 7,85 мм;
Наименование и краткая характеристика выявленных дефектов вала
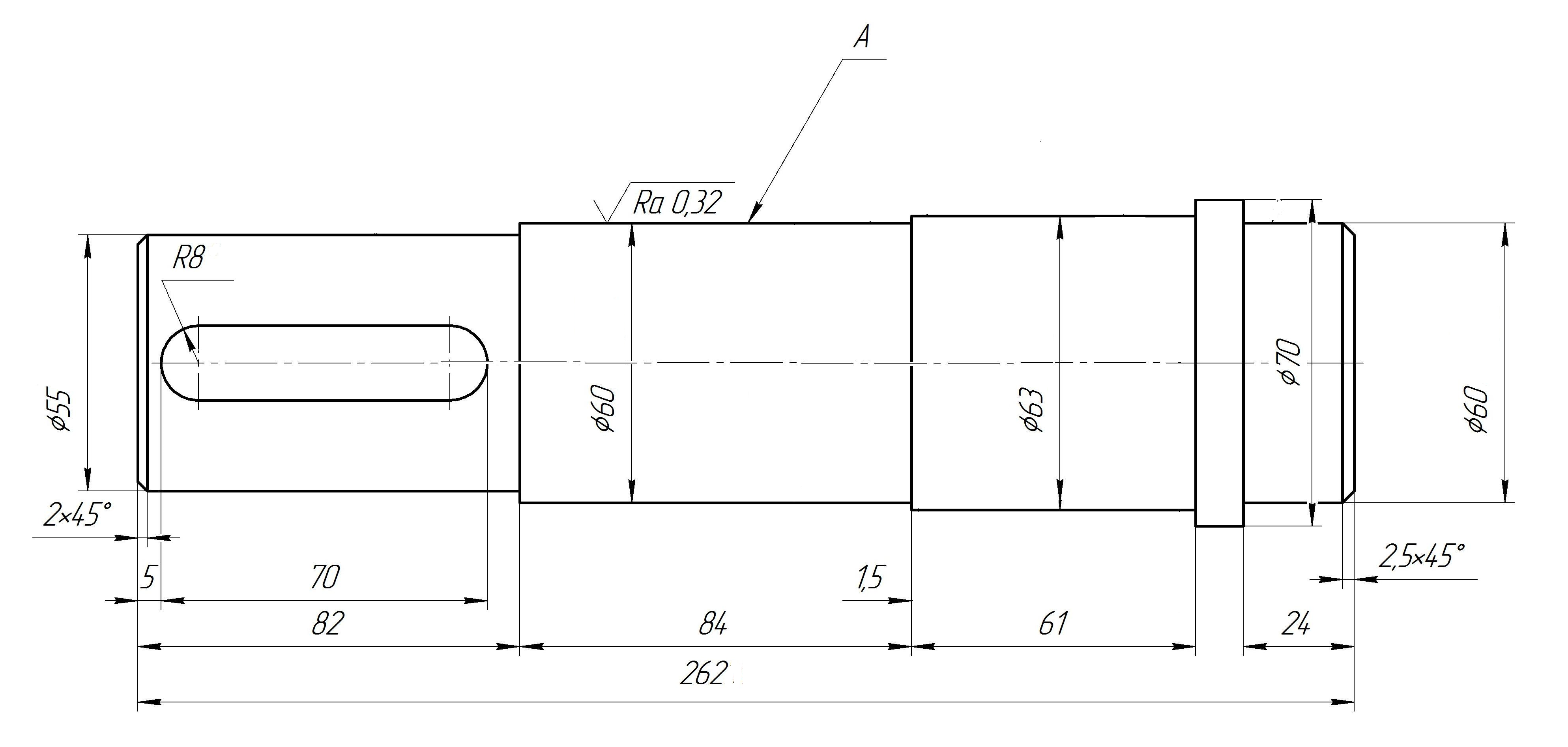
Рисунок 7 – Дефекты вала
Таблица 8 – Карта дефектов вала
Наименование дефекта | Размеры, мм | Способ устранения | ||
Возможный | Принятый | |||
А | Износ шейки вала по диаметру | 59,5 | Наплавка под слоем флюса; Наплавка в среде углекислого газа. | Наплавка под слоем флюса |
Токарная обработка
Токарная обработка производится в центрах на токарно-винторезном станке 1К62. Резец проходной упорный ГОСТ 18879-73 из твердого сплава Т15К6.
Припуск на обработку на сторону шейки вала равен: Z = 0,5 мм.
Припуск снимается за 1 проход, поэтому глубина резания будет равна:

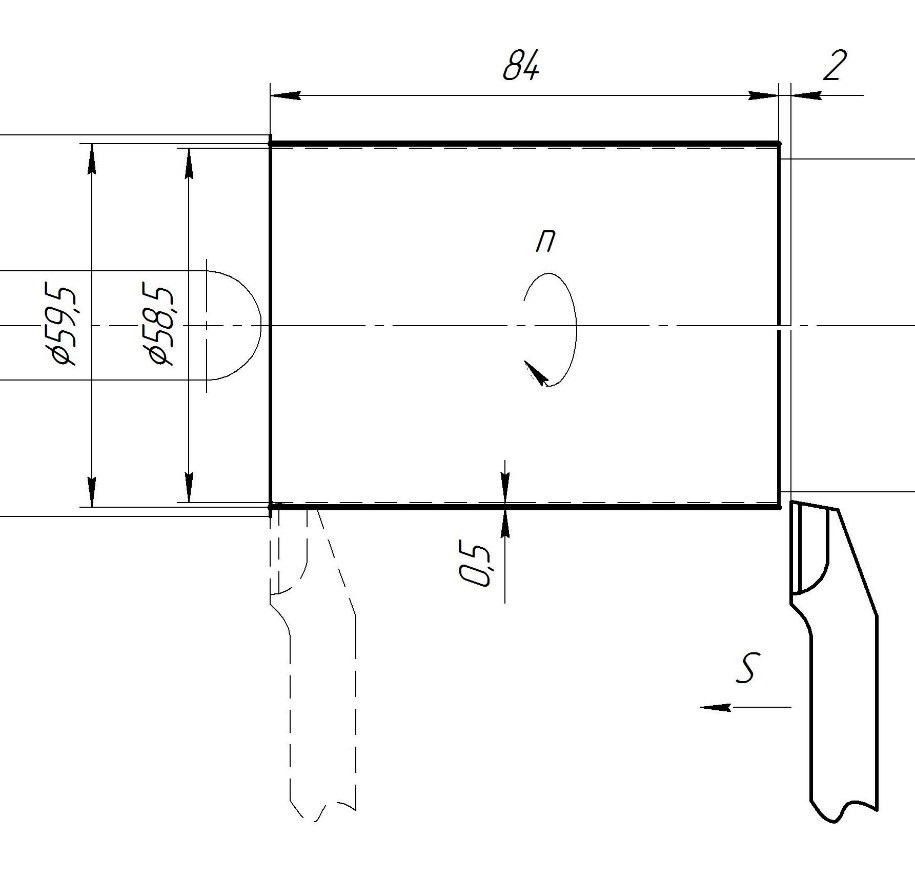
Рисунок 8 – Эскиз токарной операции
Наплавка
Для наплавки шеек вала используем проволоку марки Сталь 45 ГОСТ 2246-70 диаметром d= 1,6 мм.
Выбираем наплавочный аппарат марки A-580 c параметрами: ток наплавки J = 150 А; скорость подачи проволоки: v = 0,8 м/мин; напряжение наплавки U = 28 В;
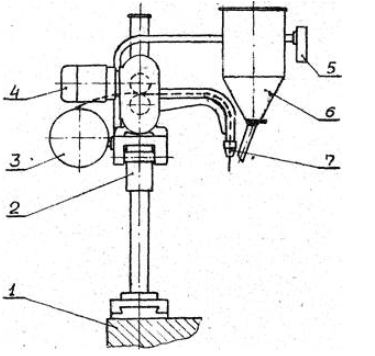
Рисунок 9 – аппарат А-580
Наплавочный аппарат 2 устанавливают на суппорте 1 токарно-винторезного станка, получающем продольное перемещение от коробки подач. Наплавляемую деталь закрепляют в шпинделе станка, частота вращения которого изменяется с помощью коробки скоростей. Наплавочная проволока от кассеты 3 с помощью подающих роликов 8, которые получают вращение от электродвигателя 4 через сменных шестерен подающего механизма, через медный мундштук 7 подается в зону горения дуги. Туда же из бункера 6 подается флюс. Управляют наплавочной установкой при помощи кнопок расположенных на пульте управления 5.
Шаг наплавки: S= 4 мм/об.
Вылет электрода: δ = 1,6 мм.
Смещение электрода: l = 0,1 мм.
Скорость наплавки выбираем из табличных данных: vн = 24 м/ч.
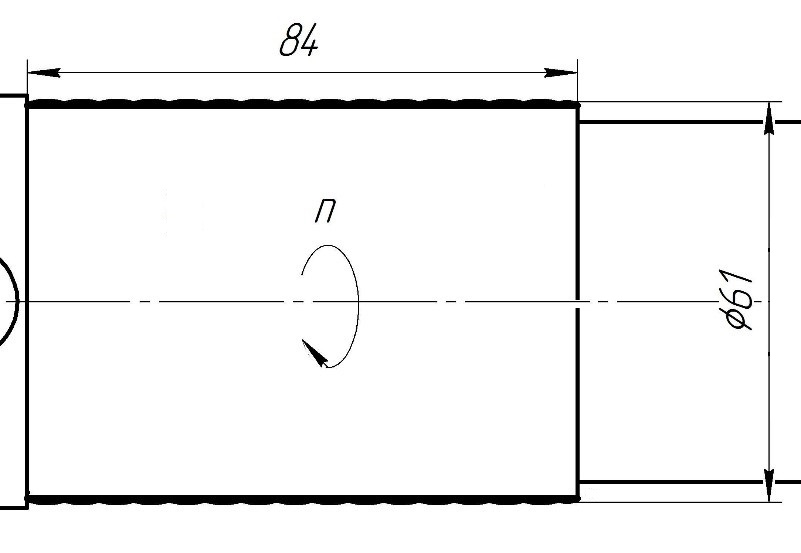
Рисунок 10 – Эскиз наплавочной операции
Токарная обработка
Токарная обработка производится в центрах на токарно-винторезном станке 1К62. Резец проходной упорный ГОСТ 18879-73 из твердого сплава Т15К6.
Рассчитаем режимы резания:
Припуск на обработку на сторону шейки вала равен: Z = 0,425 мм.
Припуск снимается за 1 проход, поэтому глубина резания будет равна:

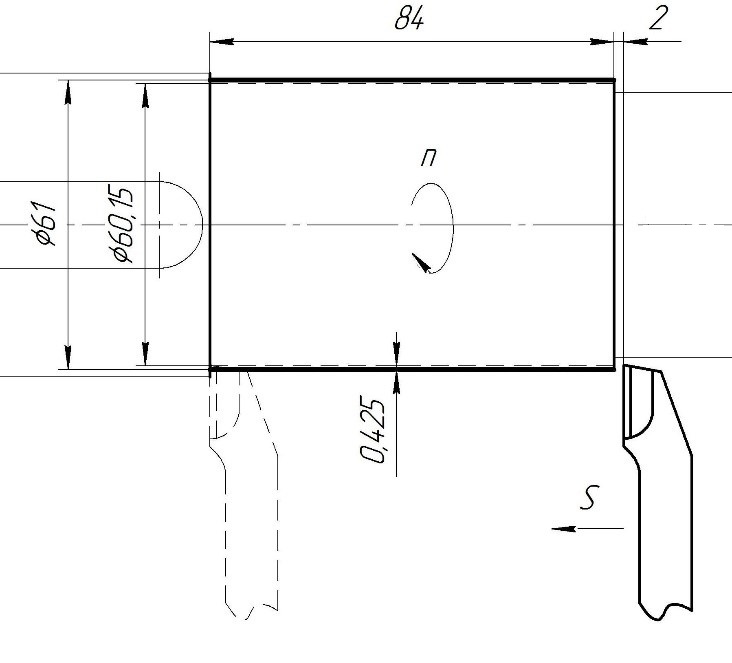
Рисунок 11 – Эскиз токарной операции
Шлифовка
Используем кругло-шлифовальный станок 3160А. Применяем круг шлифовальный плоский прямого профиля ПП ГОСТ 2424-67 с параметрами:
D = 50 мм, Н = 30 мм, d = 15 мм.
Для круглого наружного шлифования:
Скорость круга: vk = 40 м/с;
Скорость заготовки: vз = 20 м/мин;
Глубина резания: tрез = 0,015 мм;
Продольная подача:

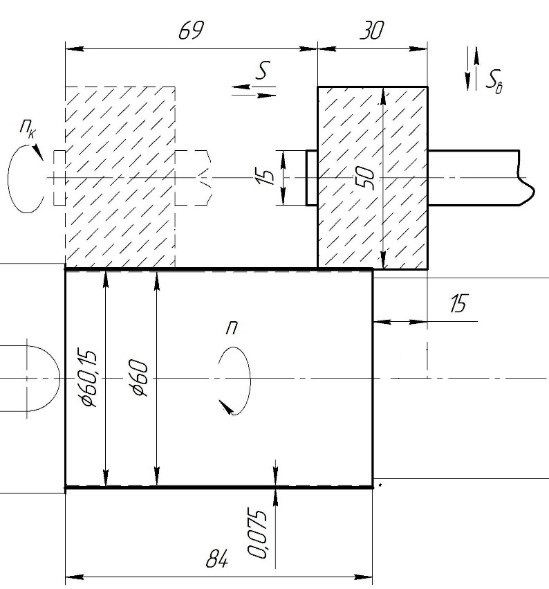
Рисунок 12 – Эскиз шлифовальной операции
Контрольно-измерительная
После проведения восстановительных операций вала, проведем контрольные замеры ремонтируемых частей детали.
При контрольно-измерительной операции вала используем штанген инструмент и микрометр.
В итоге получили следующие размеры:
1.Диаметр шейки вала (поверхность А) 60 мм;
Монтаж оборудования.
Точность обработки режущим инструментом зависит от правильности установки станка.
Однако как бы хорошо ни были обработаны поверхности скольжения, точность обработки значительно снизится при неправильной установке. Это наиболее частая причина неточности в обработке.
Необходимо четко следовать заводским инструкциям по установке оборудования; это – гарантия точности обработки.
Меры предосторожности при установке станка
- Не переносить тяжелые предметы в одиночку. Использовать подручных.
- К работе на подъемнике или кране, а также строповке станка
допускаются только лица, имеющие соответствующую квалификацию.
- При работе на подъемнике или кране следует соблюдать осторожность, чтобы не повредить другие предметы.
- Использовать тросы или стропы соответствующей грузоподъемности
- Проверить тросы, стропы, подъемное устройство и другое подъемное оборудование перед эксплуатацией. Не использовать неисправные тросы/стропы или подъемное
оборудование.
- Правильно поднимать станок. Сначала следует слегка приподнять станок, чтобы убедиться в правильности его балансировки.
- Угол наклона троса или стропа не должен превышать 60°.
- При подъеме станка с использованием подручных их действия должны
координироваться с помощью сигналов
- Во время подъема не допускать тряски станка, УЧПУ или электрошкафа.
- Перед подъемом станка убедиться в надежной фиксации узлов, а также в
отсутствии на станке инструментов и других предметов.
Устройство подачи СОЖ можно транспортировать отдельно.
Порядок подъема станка.
При транспортировке, подъеме станка его подвижные части фиксируются с помощью транспортировочных фиксаторов,
Рисунок 13 - Расположение транспортировочных фиксаторов, ось Х
Рисунок 14 - Расположение каждого транспортировочного фиксатора, оси Yt и Z
Рисунок 15 - Расположение транспортировочных фиксаторов, револьверная головка и контршпиндель.
- Подъем станка осуществляется за четыре крюка на основании станка.
- Зацепить тросы за крюк крана.
Установить деревянные бруски или прокладки между станком и тросами во избежание повреждения станка.
Рисунок 16 – строповка Integrex 300 IV
Выбор и расчет грузовых строп для перемещения грузов.
Выбор стропов начинают с определения массы груза и расположения его центра тяжести. Если на грузе таких обозначений нет, то необходимо уточнить эти параметры у лица, ответственного за производство грузоподъемных работ.
Во всех случаях необходимо убедиться в том, что груз, подлежащий перемещению, может быть поднят имеющимися в вашем распоряжении грузоподъемными средствами. Определив массу поднимаемого груза и расположение центра тяжести, затем определяют число мест строповки и их расположение с таким расчетом, чтобы груз не мог опрокинуться или самостоятельно развернуться. Из этого расчета выбирают строп или подходящее грузозахватное приспособление. Одновременно следует учитывать длину выбираемого многоветвевого стропового грузозахватного приспособления.
При выборе длины стропа следует исходить из того, что при малой длине угол между ветвями строп будет больше 90°, а при большой длине — теряется высота подъема груза и возникает возможность его кручения. Оптимальные углы между ветвями строп находятся в пределах 60 – 90° .
При выборе строп следует также определить, из каких элементов должна состоять гибкая часть стропа (стальной канат или цепь, или другой вид жестких строп и т. п.) и какие концевые и захватные элементы целесообразнее использовать для подъема конкретного груза.
Рисунок 17 – принцип строповки.
Стропа для груза рассчитывается по формуле :
S = (9.8*m)/(M*K*cos(∝))
Где :
m – Масса станка
M – количество ветвей
К – до 4 используется значение коэффициента 1, а когда 4 ветви и более, применяется 0,75
∝ - угол отклонения ветвей от вертикальной оси.
S = (9,8*12000)/(4*0,75*0,7) = 56 000 Н
Грузоподъемная сила, приходящаяся на одну ветвь стропа, равна
56 кН.
Нагрузка, приходящаяся на одну ветвь стропа, прямо пропорциональна углу между ветвями стропа и обратно пропорциональна числу ветвей. Таким образом, для подъема того или иного груза имеющимся стропом необходимо проверить, чтобы нагрузка на каждую ветвь стропа не превышала допустимой, указанной на бирке, клейме или в паспорте. В соответствии с действующими правилами Ростехнадзора грузоподъемность стропов, имеющих несколько ветвей, рассчитывают с учетом угла между ветвями 90°. Поэтому, работая групповыми стропами, необходимо лишь следить, чтобы угол α не превышал 45°.
При строповке груза групповым стропом нагрузка на его ветви, если их более трех, в большинстве случаев распределяется неравномерно, поэтому необходимо стремиться, так зацепить груз, чтобы все ветви стропа после зацепления и натяжения имели по возможности одинаковую длину, симметричность расположения и одинаковое натяжение.
Таким образом, при данной нагрузке на стропу разумно будет использовать стропу с грузоподъёмностью в 5800 кг.
Перемещение станка в цеху.
Для доставки станка внутрь помещения цеха линейные размеры входного проема должны превышать габаритные размеры станка
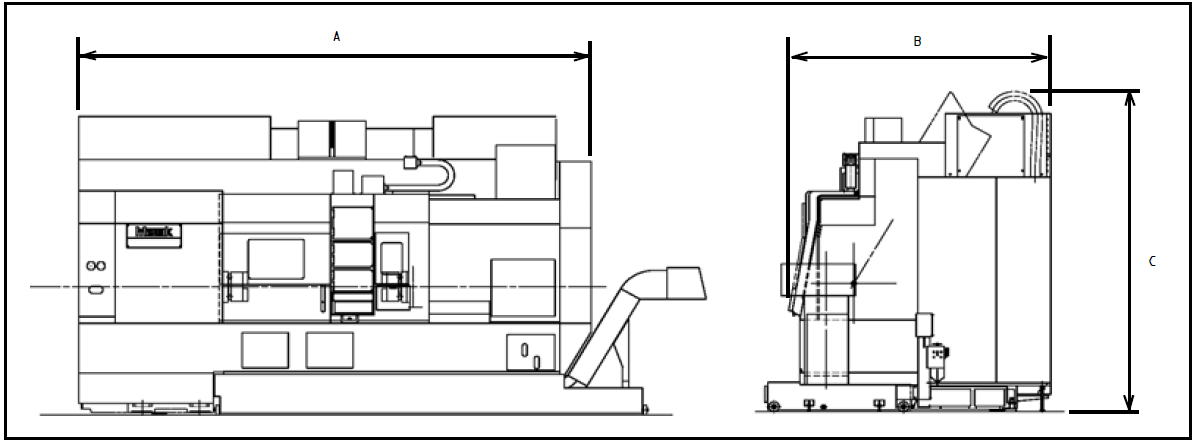
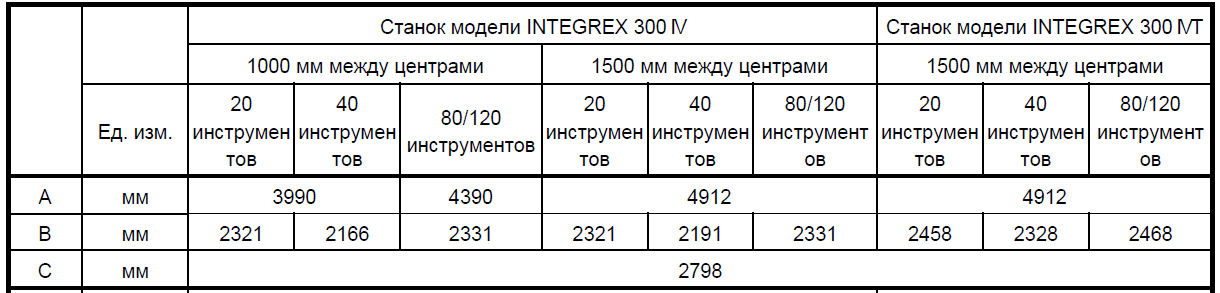
Рисунок 18 – таблица габаритных размеров станка
Лучшее средство перемещения оборудования и конструкций— мостовые краны и кран-балки. В пределах обслуживаемой ими зоны они позволяют выполнять любые операции по вертикальному и горизонтальному перемещению грузов, вес которых не превышает их грузоподъемности. Поэтому при всех условиях нужно стремиться к тому, чтобы прежде всего смонтировать крановое оборудование.
При отсутствии кранов в цехе, а также при монтаже самих кранов вопросы перемещения оборудования внутри цеха решают применением различных такелажных средств.
Установка станка
При выборе места для установки станка следует избегать:
- мест, подверженных воздействию прямого солнечного света, находящихся вблизи
источников тепла или подверженных чрезмерным перепадам температуры;
- мест с повышенной влажностью;
- пыльных мест;
- мест рядом с оборудованием, создающим вибрацию;
- мест со слабым грунтом.
Точность обработки режущим инструментом зависит от правильности установки станка.
Однако как бы хорошо ни были обработаны поверхности скольжения, точность обработки будет, по-прежнему, будет невысокой при неправильной установке станка. Иногда можно наблюдать, что новый станок не может обеспечить требуемую точность обработки. Среди многих возможных причин неточности в обработке, неправильная установка станка является одной из наиболее распространенных.
Примечание 1. Если станок устанавливается вблизи оборудования, производящего вибрацию, вокруг фундамента станка необходимо устроить траншею для защиты от вибрации.
Примечание 2. Если грунт слабый, усилить его, забив сваи, для предотвращения оседания или уклона грунта после установки станка.
1) Перед установкой анкерных болтов убедиться