ВУЗ: Не указан
Категория: Не указан
Дисциплина: Не указана
Добавлен: 09.11.2023
Просмотров: 113
Скачиваний: 2
СОДЕРЖАНИЕ
Описание конструкции оборудования и принцип действия оборудования
Производственный цикл в котором участвует обрабатывающий центр Integrex 300-IV ST
Перечень документов для проведения ремонтных работ.
Предварительная дефектная ведомость :
Технология ремонта оборудования.
Наименование и краткая характеристика выявленных дефектов зубчатого колеса.
Термическая обработка закалка и отпуск
Наименование и краткая характеристика выявленных дефектов вала
РЕГУЛЯРНЫЙ ОСМОТР И ТЕХНИЧЕСКОЕ ОБСЛУЖИВАНИЕ
Список мероприятий технического осмотра:
Осмотр во время работы (после подачи питания)
Еженедельный техосмотр или через 60 часов работы
Раз в полгода или через 1500 часов работы
Ежегодный или через 3000 часов работы
Соблюдение правил ТБ при проведении технического обслуживания
Наплавка
Для наплавки зубьев зубчатого колеса из стали 40X применяется ручная дуговая сварка. Это один из наиболее распространенных способов восстановления деталей на предприятиях.
Дуговая наплавка электродами является наиболее распространенным способом ремонта (восстановления формы и размеров) деталей и механизмов вследствие простоты ее осуществления и мобильности оборудования. Наплавку осуществляют обычно вручную, поэтому такой способ называют также ручной дуговой наплавкой:
Популярность данного способа обусловлена несколькими причинами: простота, удобство, гибкость, отсутствие необходимости в специальном оснащении.
Основные недостатки: низкая производительность, тяжелые условия для исполнителя, нестабильность качества полученного слоя, большое проплавление основного материала.
Наплавление требует от исполнителя наличия определенных навыков. Необходимо при минимальном токе оплавить оба компонента.
С помощью определения состава металла подбирается тип электрода, а толщина и форма заготовок влияет на диаметр сварочного стержня. Если толщина наплавленного материала составляет менее 1,5 мм. – то диаметр прутка должен быть 3 мм. При толщине более 1,5 мм. – 4-6 мм.
Сталь 40х – конструкционная, легированная, Х говорит о наличии легирующего элемента – хрома (0,8-1,1%), что повышает стойкость стали к коррозии. 40 – это показатель концентрации углерода (0,44%).
Такой металл весьма прочен и надежен. Его твердость составляет до 217 МПа. Еще сталь 40Х весьма устойчива к износу. Подобное вещество способно стойко противостоять негативным воздействиям агрессивной среды.
Наряду с плюсами у этой марки есть и недостатки, которые нужно знать и учитывать при работе с изделиями из нее : хрупкость, восприимчивость к ударной нагрузке; плохая свариваемость.
Чаще всего для сварки 40Х используют электроды марки МР С такими электродами легко работать, они легко поджигаются, а металл во время сварки практически не разбрызгивается.
Сталь 40Х является чувствительной к перепадам температур и образованию трещин из-за этого. Прогревать деталь нужно газовой горелкой перед любым видом сварки. Оптимальная температура для сварки данной марки стали – 300 °C. Температуру контролируем бесконтактным пирометром.
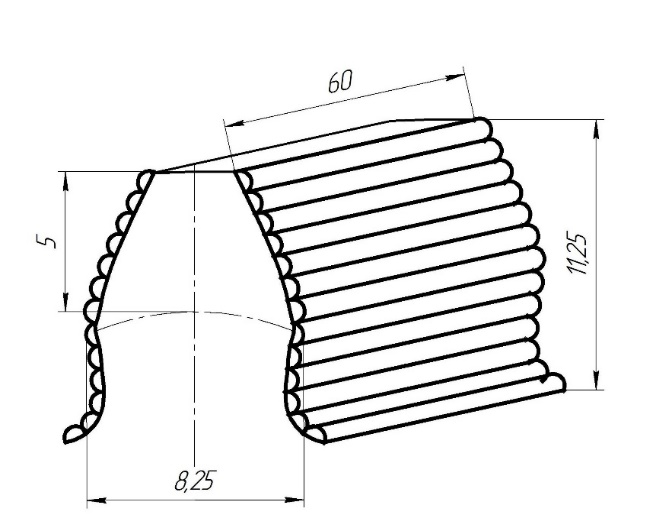
Рисунок 5 – Эскиз наплавки зубчатого колеса
Термическая обработка отжиг
Отжигом называется вид термической обработки, при котором изделия нагревают до определенной температуры, выдерживают определенное время при этой температуре и затем медленно охлаждают, достигая устойчивой равновесной структуры стали.
Основное назначение отжига – получение равновесной структуры, поэтому при отжиге, как правило, детали охлаждают медленно.
Отжиг улучшает обрабатываемость, повышает пластичность, уменьшает остаточные напряжения и т.д. Производят его в электрических печах. Обрабатываемый металл нагревают при температурах 650 – 720°С 2 – 3 часа, а затем охлаждают вместе с печью.
Зубофрезерование.
Для зубофрезерной операции используем станок 5М324 А - зубофрезерный вертикальный для цилиндрических колес.
Выбираем червячную фрезу по ГОСТ 9324-80: Однозаходная фреза 2510-4322 B c параметрами: модуль m = 5; диаметр отверстия фрезы d= 32 мм; диаметр фрезы d= 100 мм; длина фрезы L = 100 мм; число стружечных канавок z = 10. Материал – быстрорежущая сталь P18.
Величину подачи выбираем из табличных данных:

Так как фреза однозаходная, а угол наклона зуба равен нулю, то корректирование подачи не производим.
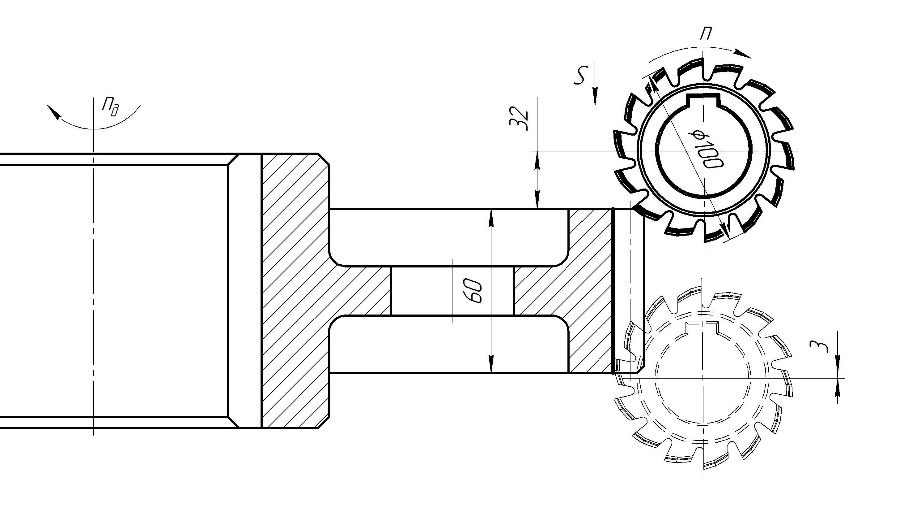
Рисунок 6 – Эскиз зубофрезерной операции
Термическая обработка закалка и отпуск
Закалкой называют вид термической обработки, при которой изделию придают высокую твердость, упругость и прочность. Однако при закалке с повышением твердости сталь становится более хрупкой. Процесс закалки заключается в нагреве изделия до высокой температуры (740 – 850°С), выдержке и быстром охлаждении с разной скоростью в разных средах – масле, воде, соляных и иных растворах. Как правило, скорость охлаждения должна быть не меньше 150°С в секунду, т.е. охлаждение должно произойти за очень короткий интервал времени – 2 – 3 секунды. Охлаждение ниже 300°С может произойти при любой температуре, так как полученная при закалке структура достаточно устойчива и скорость
дальнейшего охлаждения на нее не оказывает влияния.
Закалка не является окончательной операцией термической обработки. Для получения требуемых механических свойств, сталь после закалки чаще всего подвергают отпуску.
Отпуск обычно используется с закалкой, потому что помогает снизить внутреннее напряжение материала. Это делает сырье значительно прочнее, снимает хрупкость, которая может появиться при воздействии повышенных температур.
Еще одна цель применения — увеличение показателей ударной вязкости. Материал становится менее жестким, а значит, при сильном внешнем механическом воздействии его будет сложно повредить.
Отпуск является окончательной термической обработкой. Целью отпуска является повышение вязкости и пластичности, снижение твердости и уменьшение внутренних напряжений закаленных сталей . С повышением температуры нагрева прочность обычно снижается, а пластичность и вязкость растут. Температуру отпуска выбирают, исходя из требуемой прочности конкретной детали.Нагрев заготовки до 550 градусов по Цельсию с последующим охлаждением на воздухе. Обычно с повышением температуры отпуска ударная вязкость увеличивается, а скорость охлаждения не влияет на свойства. Но для некоторых сталей наблюдается снижение ударной вязкости. Этот дефект называется отпускной хрупкостью. После этого твердость стала равна 29 HRS.