ВУЗ: Не указан
Категория: Не указан
Дисциплина: Не указана
Добавлен: 09.11.2023
Просмотров: 128
Скачиваний: 2
СОДЕРЖАНИЕ
Описание конструкции оборудования и принцип действия оборудования
Производственный цикл в котором участвует обрабатывающий центр Integrex 300-IV ST
Перечень документов для проведения ремонтных работ.
Предварительная дефектная ведомость :
Технология ремонта оборудования.
Наименование и краткая характеристика выявленных дефектов зубчатого колеса.
Термическая обработка закалка и отпуск
Наименование и краткая характеристика выявленных дефектов вала
РЕГУЛЯРНЫЙ ОСМОТР И ТЕХНИЧЕСКОЕ ОБСЛУЖИВАНИЕ
Список мероприятий технического осмотра:
Осмотр во время работы (после подачи питания)
Еженедельный техосмотр или через 60 часов работы
Раз в полгода или через 1500 часов работы
Ежегодный или через 3000 часов работы
Соблюдение правил ТБ при проведении технического обслуживания
Принцип работы
Технология токарной обработки включает в себя основные и вспомогательные операции. Первые – это сама металлообработка, а вторые – все, что связано с подготовкой и завершением цикла обработки заготовки. В общем виде их последовательность при точении одной поверхности детали выглядит так:
-
Базирование заготовки. Выполняется ее загрузка, центровка, необходимые измерения и фиксация зажимными приспособлениями. -
Размещение оснастки. При необходимости устанавливается оснастка и приспособления, используемые в процессе работы. -
Выбор и фиксация резца. Согласно технологической карте отбирается соответствующий резец и устанавливается в резцедержатель или поворотную инструментальную головку. -
Запуск вращения шпинделя. Задается скорость вращения и включается главный привод. -
Позиционирование в исходную точку. Резец выводится в точку начала резания и устанавливается на заданном расстоянии от поверхности -
Включение подачи. Включается поперечное перемещения резца, которое по достижении заданной глубины точения переключается на продольное. -
Рабочий проход. Выполняется проход на заданной глубине со снятием металлической стружки. -
Отвод резца. По достижении конца обрабатываемой поверхности продольное перемещение переключается на поперечное, и резец отводится от поверхности. -
Новое позиционирование. Резец отводится в исходное положение (или позиционируется для нового прохода). -
Измерение. Замеряется геометрия обработанной поверхности. -
Снятие детали. Расфиксация детали и снятие ее вручную или с использованием грузоподъемных механизмов.
На основании параметров технологического процесса технолог рассчитывает нормы вспомогательного и основного времени. С учетом этих данных определяются экономические показатели изготовления изделия. Автоматизированная механообработка намного сокращает трудозатраты на единицу продукции и увеличивает коэффициент загрузки оборудования.
Производственный цикл в котором участвует обрабатывающий центр Integrex 300-IV ST
-
Производственный диспетчерский отдел (ПДО) - получение информации по заготовкам. -
Подготовка материала нужного диаметра для серийного/массового производства . -
Нарезание заготовок необходимой длины на ленточнопильном станке Pegas 400. -
Контроль ОТК. -
Складирование и транспортировка нужного объёма заготовок к станку. -
Транспортировка заготовок к металлообрабатывающему станку. -
Установка заготовок в патрон станка Integrex 300-4 ST с последующей обработкой. -
Контроль ОТК. -
Слесарная обработка – удаление заусениц (надфиль, наждачная бумага). -
Контроль ОТК. -
Транспортировка на склад готовой продукции.










Нарезка деталей заданного размера



Механическая обработка на станке Integrex 300-IV ST
Контроль ОТК
Слесарная доработка

Транспортировка на склад
Техническое обслуживание и планово-предупредительный ремонт проектируемого оборудования.
Техническое обслуживание — комплекс технологических операций и организационных действий по поддержанию работоспособности или исправности объекта при использовании по назначению, ожидании, хранении и транспортировании (техническое обслуживание), а также по восстановлению работоспособности, исправности и ресурса объекта и/или его составных частей (ремонт). ТО могут быть как плановыми (регламентированными), так и неплановыми.
Планово-предупредительный ремонт (ППР
) - проверка через установленные интервалы времени, независимо от состояния, установки или инженерной системы с осуществлением настройки и регулировки, текущего ремонта, ремонта или замены пришедших в негодность элементов, которые имеют признаки повреждения или рассматриваются как исчерпавшие предусмотренный срок службы.
Перечень быстро изнашиваемых узлов оборудования
Таблица 3 – изнашиваемы узлы станка.
Наименование узлов и деталей | Материалы | Срок службы в мес. |
Направляющие | Сталь II0ГI3Л | 36 |
ШВП | Сборка | 48 |
Грязесъемные кожуха | Сборка | 24 |
Подшипник качения | Сборка | 12 |
РВД | Сборка | 36 |
Смазка станка
Карта смазки станка показывает все точки оборудования, подлежащие обработке маслами и пластичными смазками. В ней указаны способы смазывания, марки масел, периодичность, сроки замены и количество смазочных жидкостей. Карта вывешивается у рабочего места оператора и является обязательным для исполнения документом.
Смазка шариковых винтовых передач механизмов осевой подачи осуществляется с помощью устройства автоматической подачи смазки. Охлаждающий воздух подается из пневмоблока и смешивается со смазочным маслом в зоне каждой шариковой винтовой пары.
Если из-за неполадок в системе смазки давление на выходе насоса падает ниже 0,68 МПа, срабатывает реле давления. При снижении уровня масла ниже допустимого предела срабатывает поплавковое реле уровня. В этом случае на экране появляется предупредительное сообщение и станок переходит в режим покадровой работы.
Всегда следует применять консистентную смазку рекомендованных марок.
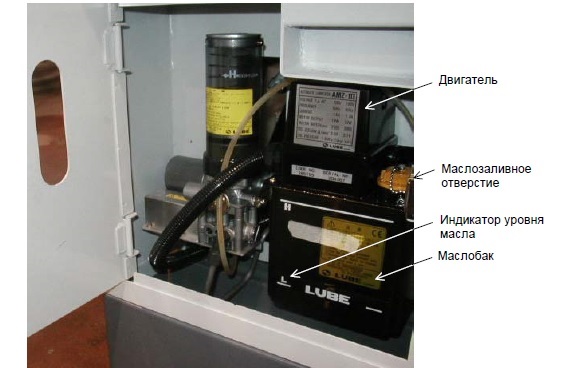
Рисунок 2 – станция смазки.
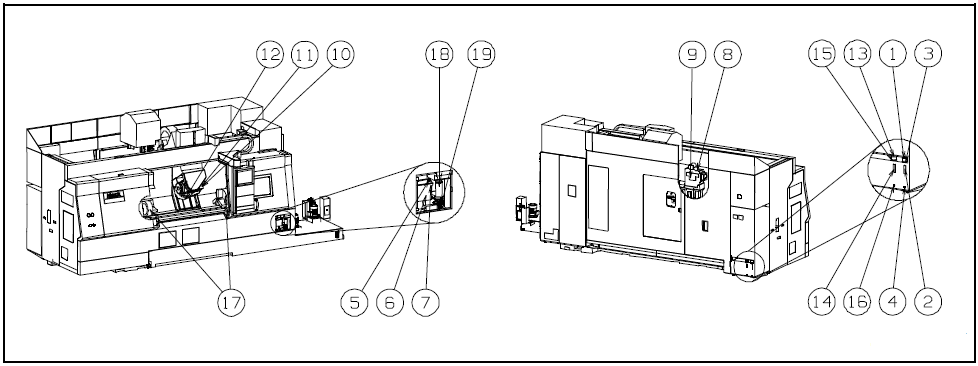
Рисунок 3 – карта смазки.
Таблица 4 – карта смазки
№ | Название детали | Точка смазки | Расход | Рекомендуемая марка масла | Примечания |
1 | Масломерное стекло | Гидравли- ческий силовой блок | 20 л | D.T.E. 24 (Mobil) UNI POWER 32 (Esso) TELLUS OIL 32 (Shell) | - Менять масло раз в полгода и производить очистку ловушки с сеткой |
2 | Визуальный Указатель уровня | ||||
3 | Сетчатый фильтр | ||||
4 | Сливная пробка | ||||
5 | Крышка масляного фильтра | Подторма- живание оси C | 1.8 л | VACTRA No. 2 (Mobil) FEBIS K68 (Esso) TONNA OIL T68 (Shell) | - Смазывать по мере необходимости - Чистить фильтр ежегодно |
6 | Масломерное стекло | ||||
7 | Всасывающий фильтр | АСИ | |||
8 | Крышка масляного фильтра | 6 л | - Менять масло ежегодно | ||
9 | Пробка сливного отверстия |
Продожение таблицы 4
10 | Масломерное стекло | Ось В | 3,5 л | SHC 629 (Mobil) | - Менять масло ежегодно |
11 | Крышка масляного фильтра | ||||
12 | Сливная пробка | ||||
13 | Крышка масляного фильтра | Блок охлаждения | 50 л | VELOCITE OIL № 3 (Mobil) | - Менять масло ежегодно |
14 | Масломерное стекло | ||||
15 | Сетчатый фильтр |
Организация ремонтных работ.
Вывод оборудования в ремонт и все ремонтные работы должны проводиться в полном соответствии с требованиями, изложенными в инструкциях и правилах, действующих на предприятиях, в частности:
а) по технике безопасности, промышленной санитарии и пожарной безопасности цеха, в котором проводятся работы;
б) по организации и ведению работ в газоопасных местах и порядку оформления разрешений на право выполнения этих работ на предприятии;
в) о порядке проведения огневых работ;
г) о порядке работы сторонних цехов и служб предприятия в энергетических цехах.
Оборудование останавливают на ремонт в соответствии с действующей инструкцией по эксплуатации (пуску, обслуживанию и остановке) этого оборудования.
При подготовке оборудования к ремонту необходимо выполнить следующие работы:
а) отключить электроэнергию, снять напряжение на сборках и щитах, отсоединить ремонтируемый объект от всех подходящих к объекту и отходящих от него коммуникаций с помощью заглушек;
б) освободить оборудование и коммуникации от грязи и шлама, которые следует удалить из помещения, промыть, пропарить, продуть и проветрить;
в) подготовить места для установки заглушек и установить их.
Ответственность за подготовку мест установки заглушек согласно схеме, за их установку и снятие, а также за своевременную запись об этом в журнале несет лицо, ответственное за вывод оборудования в ремонт.