Файл: Организация работы участка по ремонту автосцепок с разработкой технолгии ремонт автосцепного устройства.docx
ВУЗ: Не указан
Категория: Не указан
Дисциплина: Не указана
Добавлен: 10.11.2023
Просмотров: 120
Скачиваний: 2
ВНИМАНИЕ! Если данный файл нарушает Ваши авторские права, то обязательно сообщите нам.
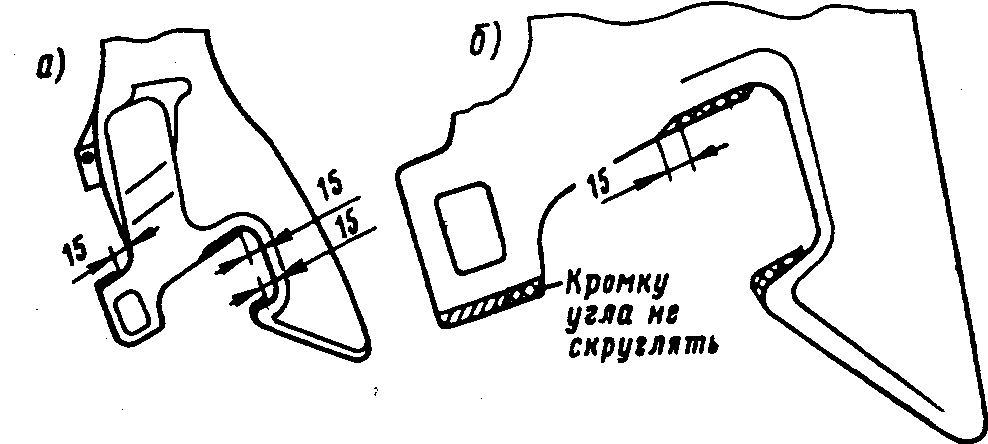
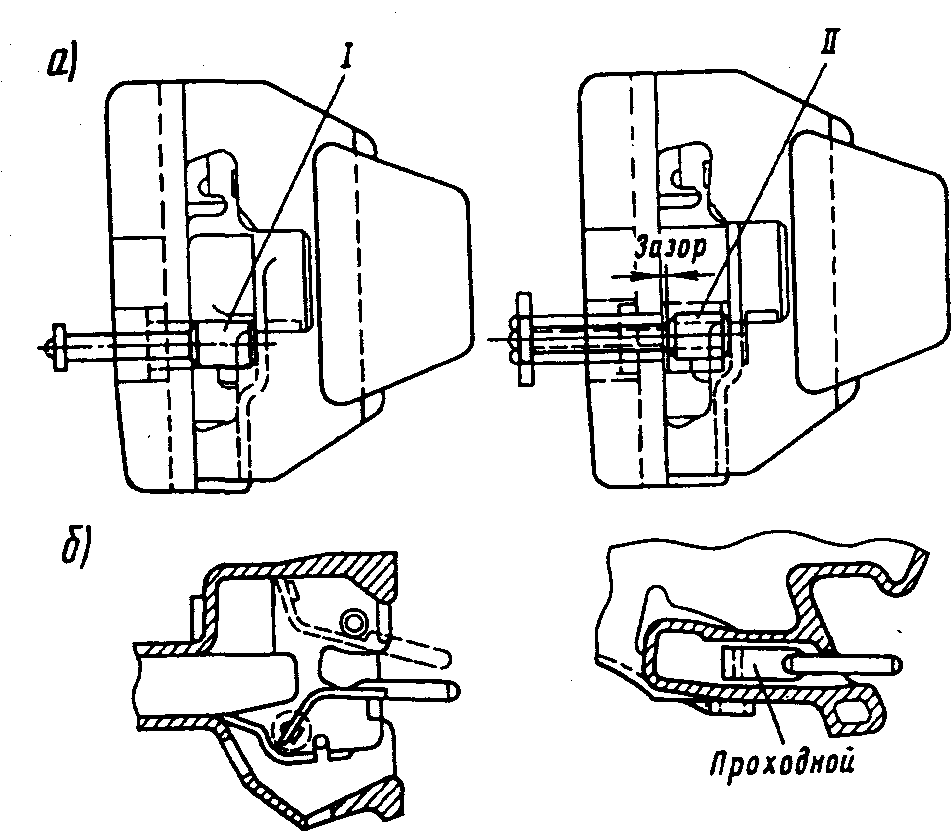
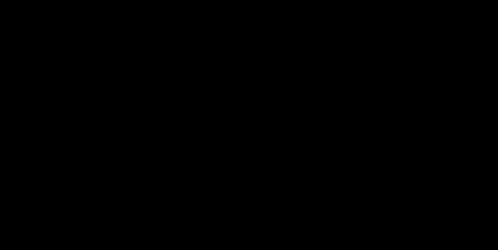
Рисунок 1.7. Требования к поверхностям контура зацепления корпуса автосцепки после их наплавки
Ширина кармана для замка в корпусе считается увеличенной, если при вращении валика подъемника подъемник замка проходит мимо нижнего плеча предохранителя, не задевая его своим верхним широким пальцем. В этом случае соосно с малым отверстием для валика подъемника должна быть приварена шайба такой толщины, чтобы ширина исправленного кармана отвечала требованиям проверки непроходным шаблоном 845р и проходным 848р.
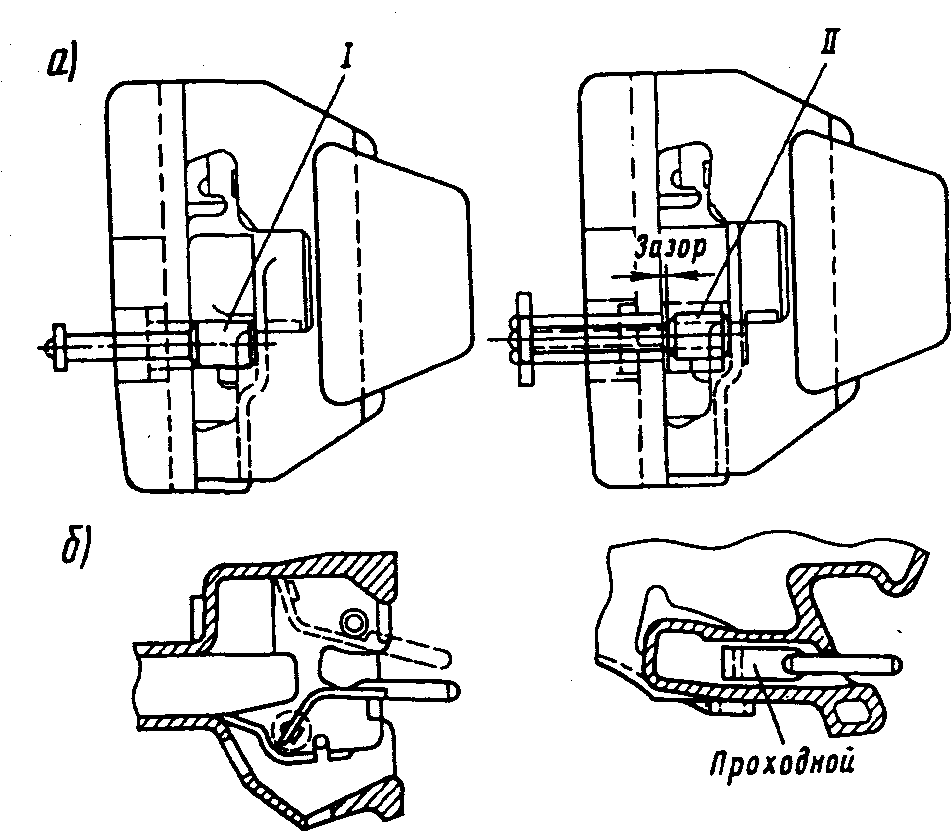
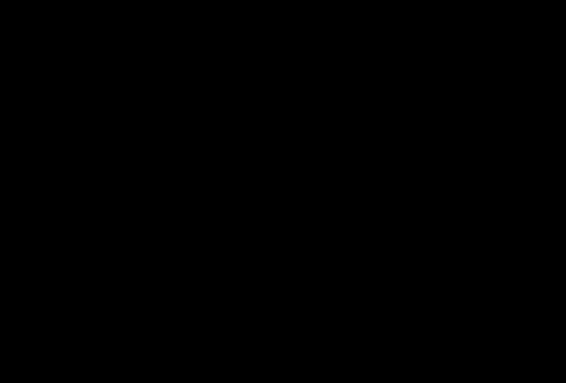
Рисунок 1.8. Проверка ширины кармана корпуса автосцепки: а - непроходным шаблоном 845р; б - проходным шаблоном 848р. / - корпус годен
Для проверки шаблон 845р вводят в карман корпуса автосцепки через большое отверстие для валика подъемника до упора во внутреннюю стенку кармана так, чтобы шаблон касался стенки корпуса всей торцовой поверхностью (рис. 1.8, а). При этом цилиндрическая часть шаблона не должна проходить между стенками кармана. Шаблон 848р вводят внутрь головы корпуса через окно для замка и пропускают между стенками кармана. Ширина кармана признается правильной, если мерительная полоса шаблона свободно проходит между стенками по всей ширине кармана (рис. 1.8, б).
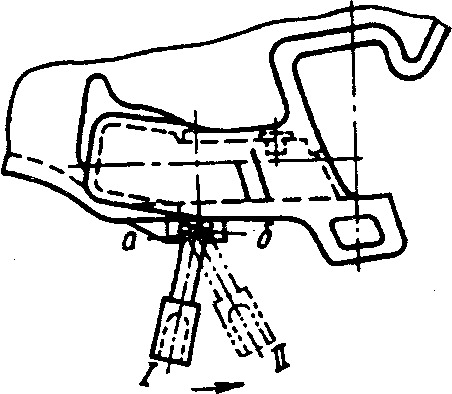
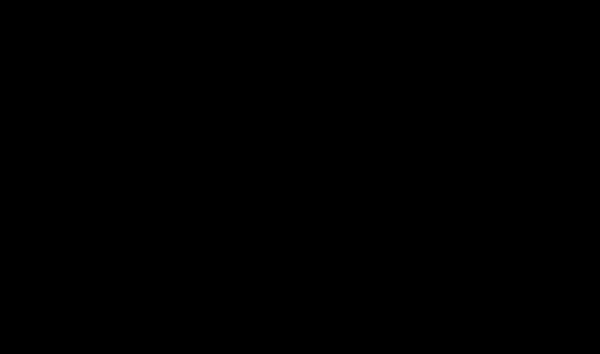
Рисунок 1.9. Проверка положения отверстия Д"" запорного болта валика подъемника шаблоном 845р
Шаблоном 845р также контролируют расстояние от передней кромки отверстия для валика подъемника до стенки отверстия для запорного болта (рис. 1.9). Для этого шаблон устанавливают так, чтобы прямолинейная поверхность а непроходной его планки входила в паз для запорного болта, при этом полукруглая поверхность б шаблона не должна проходить мимо передней кромки отверстия для валика подъемника (положение Г). Если поверхность
б проходит мимо передней кромки отверстия для валика подъемника (положение II), то необходимо наплавить стенку паза для запорного болта, а затем обработать ее заподлицо с поверхностью задней кромки отверстия для валика подъемника.
После обработки отверстие проверяют шаблоном 845р с установкой запорного болта, который должен свободно входить на свое место и легко извлекаться.
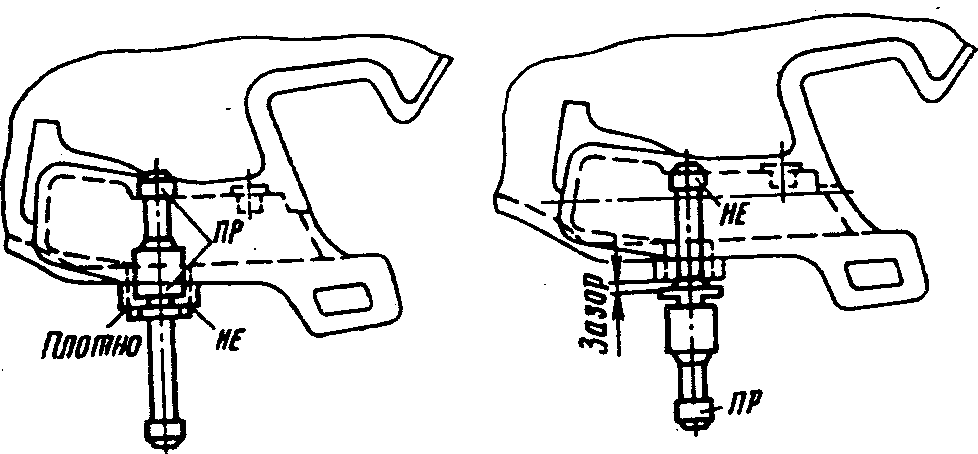
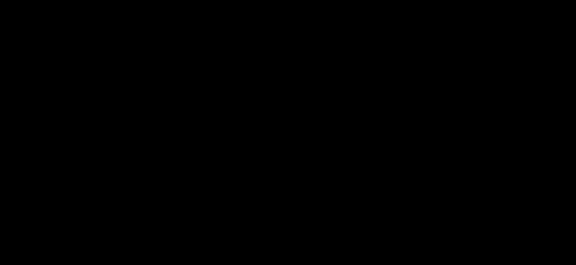
Рисунок 1.10. Проверка диаметров и соосности малого и большого отверстий для валика подъемника в корпусе автосцепки шаблоном 797р
Диаметры и соосность малого и большого отверстий для валика подъемника проверяют шаблоном 797р (рис. 1.10), а положение отверстий относительно контура зацепления автосцепки — шаблонами 937р и 797р (рис. 1.11). Корпус считается годным, если проходная часть шаблона 797р свободно входит в со ответствующее отверстие, а непроходная часть шаблона не входит в отверстие до упора в торец прилива корпуса.
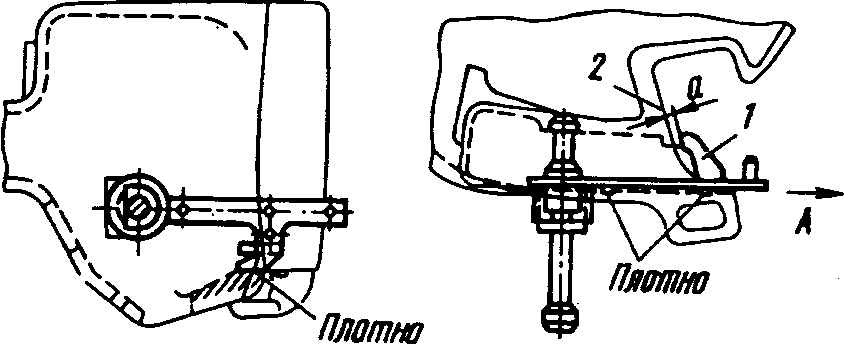
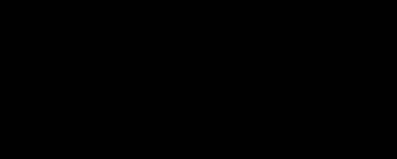
Рисунок 1.11. Проверка положения отверстий для валика подъемника относительно контура зацепления автосцепки шаблонами 937р и 797р
Если непроходные части шаблона входят в соответствующие отверстая, значит стенки отверстий изношены и их надо отремонтировать наплавкой с последующей обработкой. После ремонта положение отверстий проверяют шаблонами 937р и 797р (см. рис.1.11). Для проверки шаблон 937р вводят в карман корпуса, а через отверстие этого шаблона пропускают шаблон 797р. Затем, прижимая шаблон к внутренней стенке и нижней перемычке малого зуба, перемещают его по направлению стрелки А, проверяя при этом зазор а между упором 1 и ударной стенкой 2 зева. Положение отверстий признается правильным, если этот зазор составляет не более 4 мм.
Размеры шипа для замкодержателя и его положение относительно контура зацепления корпуса автосцепки проверяют шаблонами 849р-1,806р и 816р.
Шаблоном 849р-1 контролируют высоту шипа. Если в пространство между стенкой со стороны малого зуба и торцом шипа проходит проходная часть шаблона и не проходит непроходная
, значит высота шипа соответствует требованиям.
Если в это пространство проходит непроходная часть шаблона (шип короткий) или не проходит проходная (шип длинный), то шип должен быть отремонтирован. Проверка производится по всей поверхности торца шипа. Диаметр и состояние кромки торца шипа проверяют шаблоном 806р (рис. 1.12). С этой целью шаблон плотно прижимают к торцу шипа и перемещают вдоль рукоятки (показано стрелками), последовательно поворачивая рукоятку в зоне А..
Если при этом шил проходит в проходной вырез шаблона и не проходит в непроходной, то он считается исправным (годным).
В противном случае шип должен быть отремонтирован.
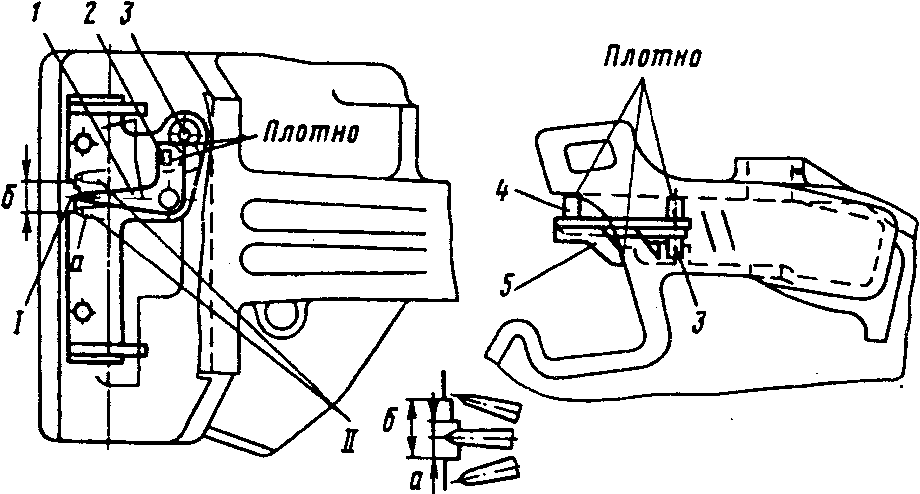
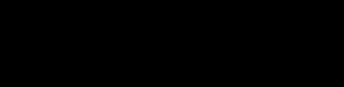
Рисунок 1.13. Проверка положения шипа для
Положение передней поверхности шипа относительно контура зацепления автосцепки проверяют шаблоном 816р (рис. 1.13). Для проверки шаблон вводят в карман корпуса автосцепки и устанавливают так, чтобы опоры 4 были прижаты к внутренней стенке малого зуба, опоры 5 упирались в ударную стенку зева, а внутренняя опора 3 своей нижней плоской частью опиралась на верх шипа для замкодержателя. Удерживая шаблон в таком положении, поднимают заостренный конец стрелки 1 до тех пор, пока выступ 2 на другом ее конце не упрется в переднюю часть поверхности шипа.
Положение I шипа считается правильным, если заостренный конец стрелки 1 не выходит за пределы контрольного выреза б в листе шаблона. Шип негоден, если острие стрелки выходит за пределы выреза (положение II).
Если шип не удовлетворяет требованиям проверки хотя бы одного из шаблонов 849р-1, 806р и 816р, то его необходимо отремонтировать и затем проверить вышеуказанным порядком. Но в этом случае к шипу предъявляется более жесткое требование: конец стрелки 1 не должен выходить за пределы более глубокого выреза а шаблона.
Кроме того, нужно проверить положение отремонтированного шипа относительно отверстия для валика подъемника шаблоном 938р (рис. 1.14). Это положение считается правильным, если шаблон отверстием а надевается на шип, а выступом б входит в малое отверстие для валика подъемника. Как у отверстия, так и у шипа шаблон должен прилегать к плоскости кармана корпуса.
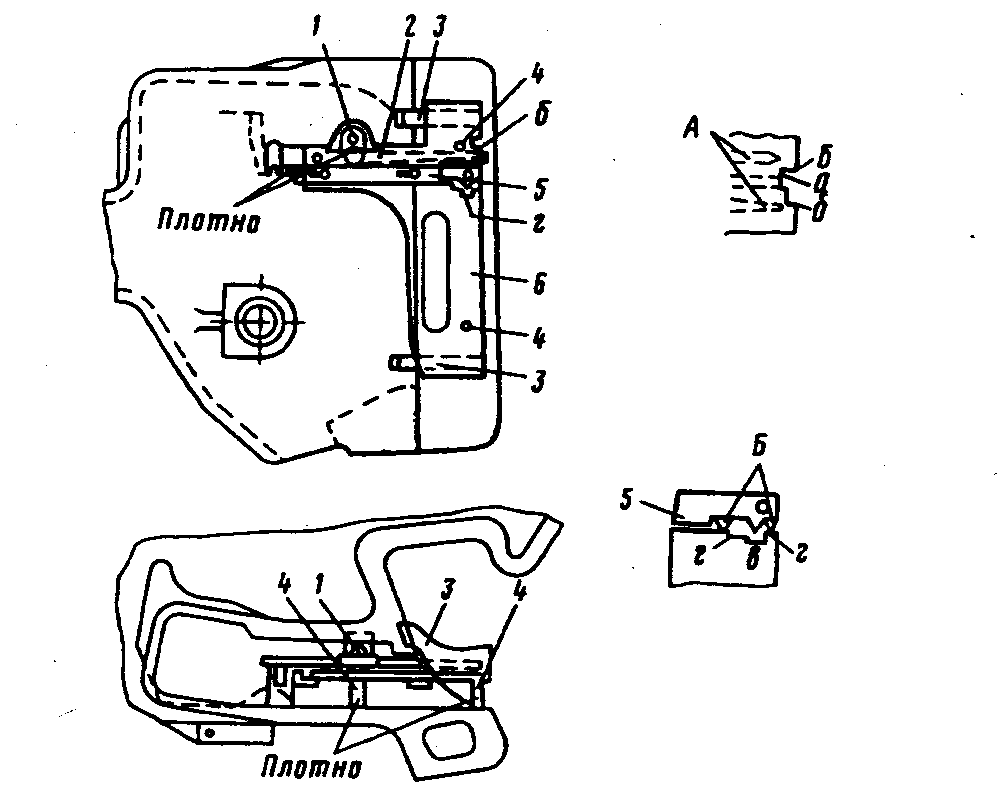
Рисунок 1.15. Проверка положения полочки для верхнего плеча предохранителя относительно шипа для замкодержателя и контура зацепления автосцепкишаблоном 834р
Положение полочки для верхнего плеча предохранителя в корпусе относительно шипа для замкодержателя и контура зацепления проверяют шаблоном 834р (рис. 1.15), после того, как будет установлено, что шип для навешивания замкодержателя удовлетворяет требованиям проверки шаблонами 849р-1, 806р и 816р.
Для проверки шаблон 834р нужно взять за основание 6, ввести в карман корпуса и установить так, чтобы упоры 3 и выступы 4 были плотно прижаты к неизнашиваемой части ударной поверхности зева и внутренней стенке малого зуба, а прямоугольная опора 1 опиралась на шип для замкодержателя.
После такой установки шаблона положение полочки по вертикали проверяют поворотом стрелки 2, заостренный конец которой поднимают вверх до тех пор, пока ее задний конец не упрется в верхнюю поверхность полочки. Положение полочки по горизонтали проверяют с помощью движка 5, который передвигают до упора в переднюю кромку полочки. Если острие стрелки 2, опирающейся другим своим концом на рабочую поверхность полочки, располагается вне пределов обеих ступеней контрольного выреза б, значит положение полочки по вертикали неправильное (поз. А). Если указатель движка 5, упирающегося в полочку, располагается вне пределов обеих ступеней контрольного выреза г, то это указывает на неправильное положение полочки по горизонтали (поз. Б).
Для правильного показания шаблона при проверке положения полочки по вертикали необходимо поворачивать стрелку 2 при полностью выдвинутом на себя движке 5, а положение полочки по горизонтали проверять при крайнем нижнем положении указателя стрелки 2.
Полочка, не удовлетворяющая требованиям проверки шаблоном 834р, должна быть отремонтирована или заменена новой.
Новую или отремонтированную полочку также проверяют шаблоном 834р, как описано выше. Но при этом предъявляются повышенные требования, а именно: положение полочки считается правильным, когда указатели стрелки и движка располагаются соответственно в пределах более глубоких вырезов а и в.
Толщина перемычки хвостовика автосцепки СА-3 должна отвечать требованиям .проверки непроходным шаблоном 897Р-1 или 898р-1 (рис. 1.16, а) в зависимости от вида ремонта подвижного состава (приложение 2) как со стороны верхней, так и со стороны нижней плоскости. Перемычка считается годной, если шаблон не надевается на нее полностью (поз. I); если шаблон доходит до упора в перемычку, то она негодна (поз. II).
Перемычка, изношенная клином тягового хомута и имеющая размеры менее допустимых, подлежит наплавке. Изношенную торцовую часть хвостовика восстанавливают наплавкой в случае, если длина хвостовика автосцепки менее 645 мм, а для автосцепки СА-ЗМ 1 — менее 654 мм.
Примечание. Автосцепка СА-ЗМ устанавливается на 8-осных и некоторых специальных вагонах, а также маневровых 8-осных локомотивах. Допускается при ремонте производить замену автосцепки СА-ЗМ на автосцепку СА-3 с ограничителем вертикальных перемещений при одновременной замене упряжного устройства (тяговый хомут, поглощающий аппарат, клин тягового хомута) в соответствии с проектом ПКБ ЦВ № М 1497.00.000.
Толщина перемычки хвостовика автосцепки СА-ЗМ, измеренная в средней части, должна быть не менее 44 мм при всех видах периодического ремонта подвижного состава. Измерение производится кронциркулем, снабженным мерительной планкой.
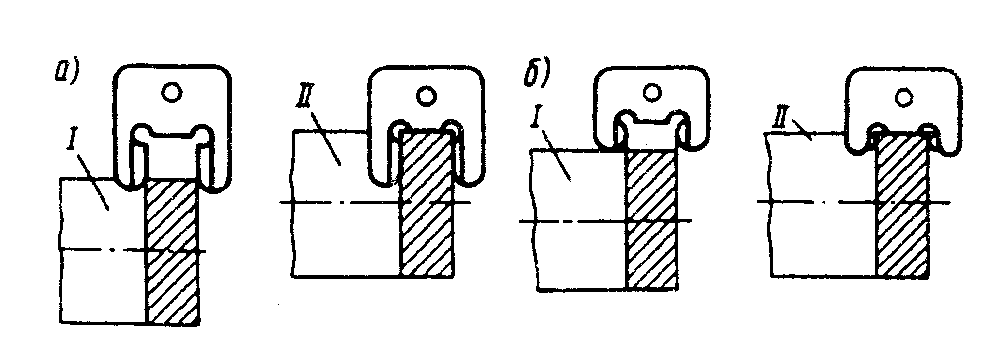
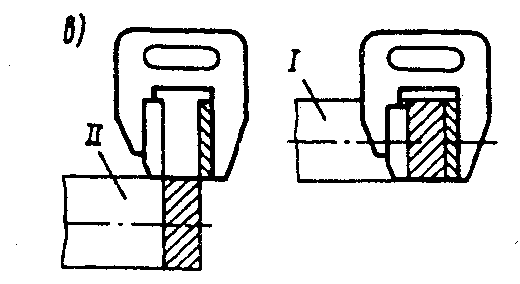
а—непроходным шаблоном 897р-1 или 898р-1; б — непроходным шаблоном 900р-1; в — проходным шаблоном 46г (/—перемычка годна. // — перемычка негодна)
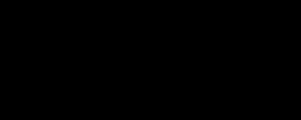
Рисунок 1.16. Проверка толщины
Перемычка хвостовика автосцепки СА-3 со стороны клина должна быть обработана таким образом, чтобы получилась ровная цилиндрическая поверхность с радиусом кривизны не менее 16 мм и не более 20 мм, с плавным переходом в боковые поверхности стенок отверстия.
После ремонта перемычку хвостовика проверяют непроходным 900р-1 (рис. 1.16, б) и проходным 46г (рис. 1.16, в) шаблонами.
Поверхности хвостовика корпуса, соприкасающиеся.с тяговым хомутом, центрирующей балочкой, стенками ударной розетки и клином тягового хомута (боковые стенки отверстия), изношенные на глубину более 3 мм, должны быть наплавлены, а затем обработаны заподлицо с литейной поверхностью.
Погнутый хвостовик автосцепки должен быть выправлен в том случае, если его изгиб г (рис. 1.17), измеряемый от первоначальной продольной оси корпуса в средней части, превышает 3 мм.
Разметка корпуса для определения изгиба в горизонтальной плоскости производится, как показано на рис. 1.17, а. Сначала находят и обозначают середину хвостовика на расстоянии 20 мм от упора головы, а также на торце и в средней части.