Файл: Государственное бюджетное профессиональное образовательное учреждение московский государственный образовательный комплекс.docx
ВУЗ: Не указан
Категория: Не указан
Дисциплина: Не указана
Добавлен: 12.01.2024
Просмотров: 202
Скачиваний: 2
ВНИМАНИЕ! Если данный файл нарушает Ваши авторские права, то обязательно сообщите нам.
СОДЕРЖАНИЕ
Глава 3. Алгоритм расчёта параметров печатающей головки.................................63
Глава 1. Анализ известных исследований точности аддитивных мехатронных установок
2. Смещение предыдущего слоя относительно нанесенного слоя;
3. Плотность при укладке слоев.
Глава 2. Расчёт и проектирование литьевой мехатронной аддитивной установки. Математический анализ.
2.1. Разработка мехатронной установки присадок для производства форм для литья в песчаные формы.
1. подсистема производства связующего;
2. Подсистема порошкового покрытия.
Расширенная структурная схема технологического комплекса представлена на рисунке 2.1.3.
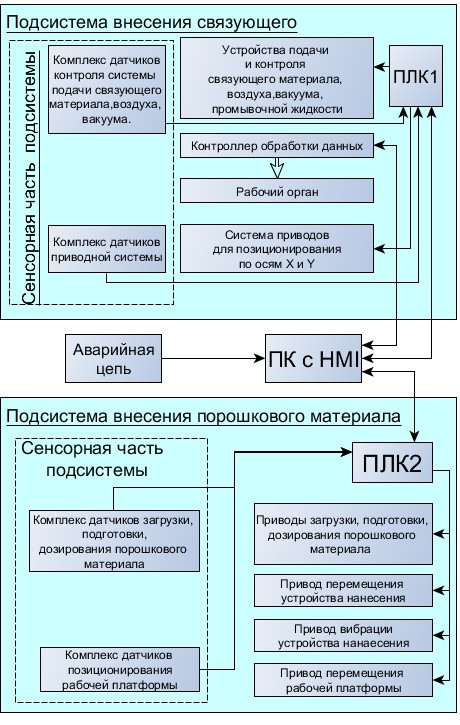
Рисунок 2.1.3 – Структурная схема системы управления технологическим комплексом.
Технологический комплекс условно можно разделить на две подсистемы, которые связаны между собой управляющим компьютером:
1. подсистема производства связующего;
2. Подсистема порошкового покрытия.
Расширенная структурная схема технологического комплекса представлена на рисунке 2.1.3.
Общее управление технологическим комплексом осуществляется с помощью персонального компьютера с панелью управления, отображаемой на сенсорном экране. Каждая подсистема управляется собственным промышленным логическим контроллером, к которому подключены приводные системы, датчики обратной связи и другие функциональные устройства. Помимо основного API, подсистема ввода привязки также включает контроллер для обработки данных для печати и отправки на печатающие головки. ПЛК также контролирует движение печатающей головки и другие функции, такие как поддержание уровня вакуума, уровень клея во вспомогательном баке, изменение клапанов и т.д. Связующее добавляется по алгоритмам, обрабатывающим цифровую модель продукта и формирующим управляющие сигналы для рабочего элемента: набор печатающих головок с 300 индивидуально управляемыми соплами, через которые подается связующее. Подсистема порошкового покрытия подготавливает материал, смешивает его с катализатором и загружает в портальный аппликатор в полностью автоматическом режиме на основе данных, полученных от датчиков и алгоритмов, запрограммированных в контроллере. Каждая подсистема по-своему влияет на качество и точность деталей. Необходимо изучить факторы в обеих системах, которые влияют на параметры точности конечного продукта, и определить наиболее важные параметры.2.2. Состав составляющих элементов, влияющих на прецизионные параметры установки мехатронных присадок.
В настоящее время производители оборудования для аддитивного производства не дают однозначного ответа на вопрос о точности крепления изделий к оборудованию. Например, VoxelJet предлагает разрешение инструмента (600 точек на дюйм) и точность размещения инструмента (100 мкм), которые можно экстраполировать на возможную точность производимого продукта. Кроме того, точность продуктов можно приблизительно оценить на основе эмпирических данных, полученных с помощью устройства. Однако окончательная точность конечного продукта неизвестна, пока продукт не будет получен. В то же время имеющиеся данные не позволяют прогнозировать возможные отклонения размеров и форм изделий при изменении технологических и материальных режимов.
На точность, которой можно добиться при получении товара, влияет множество факторов, которые можно разделить на две группы:
1) технологический.
2) constructively (конструктивно).
К технологическим факторам относятся факторы, которые можно проследить до влияния технологических моментов в процессе. Свойства рабочих материалов, взаимодействие материалов, технологические параметры работы и др.
К конструктивным факторам относятся: жесткость конструкции, погрешности позиционирования, неточности в основной части работы и т.д.
Каждый из факторов по-разному влияет на точность результата. Этот документ определяет ключевые факторы и оценивает их совокупное влияние на конечную точность продуктов.
Условно, исходя из деталей работы технологического комплекса, можно разделить разломы по осям X, Y и Z. Положение осей показано на рисунке 2.2.1.
Изделие состоит из множества поперечных слоев. Каждый слой состоит из песка, который подается на погрузчик песка при движении песчаной скважины по оси Y, и другого связующего рабочей жидкости, движущегося по оси X. Точность контуров каждого слоя зависит от погрешности система позиционирования работы самой рабочей жидкости и в процессе нанесения очередного слоя.
Выясняем все возможные факторы, влияющие на точность формирования контура реза, готового слоя и погрешности формирования толщины слоя.
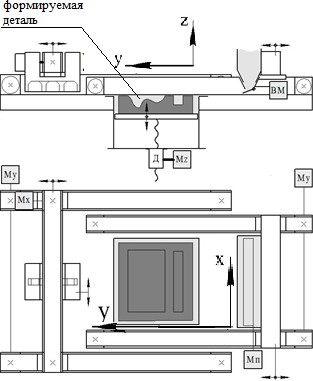
По оси X отклонения от линейных размеров изделий могут быть вызваны следующими факторами:
Отклонение координаты точки подачи от расчетного значения.
(а) вызвано отклонением траектории полета от вертикали;
б) вызвано ошибкой вывода пропущенного сигнала;
в) вызвано отклонением от скорости выведения капель из сопла;
г) из-за уменьшения скорости капель из-за сопротивления воздуха каплям разного размера;
д) из-за изменения скорости движения СГ, вызванного изменением плотности распределения точек по оси
2. Неточности из-за неточностей при сборке и изготовлении мобильного устройства.
Изменение размеров поперечного сечения зависит от гранулометрического состава порошкового материала.
По оси Y отклонения от линейных размеров изделий могут быть вызваны следующими факторами:
1. Отклонения координат точки впрыска капли от расчетного значения из-за ошибки выброса капли из сопла;
2. Отклонение в размерах из-за ошибок сборки и обращения с подвижной конструкцией.
3. Отклонение размеров в зависимости от гранулометрического состава порошкового материала.
4. Погрешности размеров из-за установки порошкового покрытия.
По оси Z отклонения от линейных размеров изделий могут быть вызваны следующими факторами:
1. Ошибка положения платформы.
2. Отклонение размеров как функция гранулометрического состава порошкового материала.
3. Отклонение размеров из-за действия устройства компенсации порошка.
Помимо точности сжатия каждого слоя отдельно по осям, специфика получения изделий послойным синтезом приводит к отклонениям контура из-за искривленных поверхностей по сравнению с теоретическими.
Затем мы смотрим на каждый фактор размера и рассматриваем порядок внесенных ошибок.
2.3. Отклонениекоординаты точки внесения капли связующего материала от расчетногозначения
В офисном рабочем пространстве используется набор пьезоэлектрических (PG) струйных печатающих головок с индивидуально управляемыми соплами, которые перемещаются по осям X и Y с помощью 2D-манипулятора.
Кинематическая схема подсистемы хранения скоросшивателя приведена на рисунке 2.3.1. Печатающая головка перемещается линейными ленточными модулями (2, 6, 8), которые приводятся в действие сервоприводами (сервоприводы 1, 5) с оптическим энкодером в качестве датчика обратной связи (D4, D8).
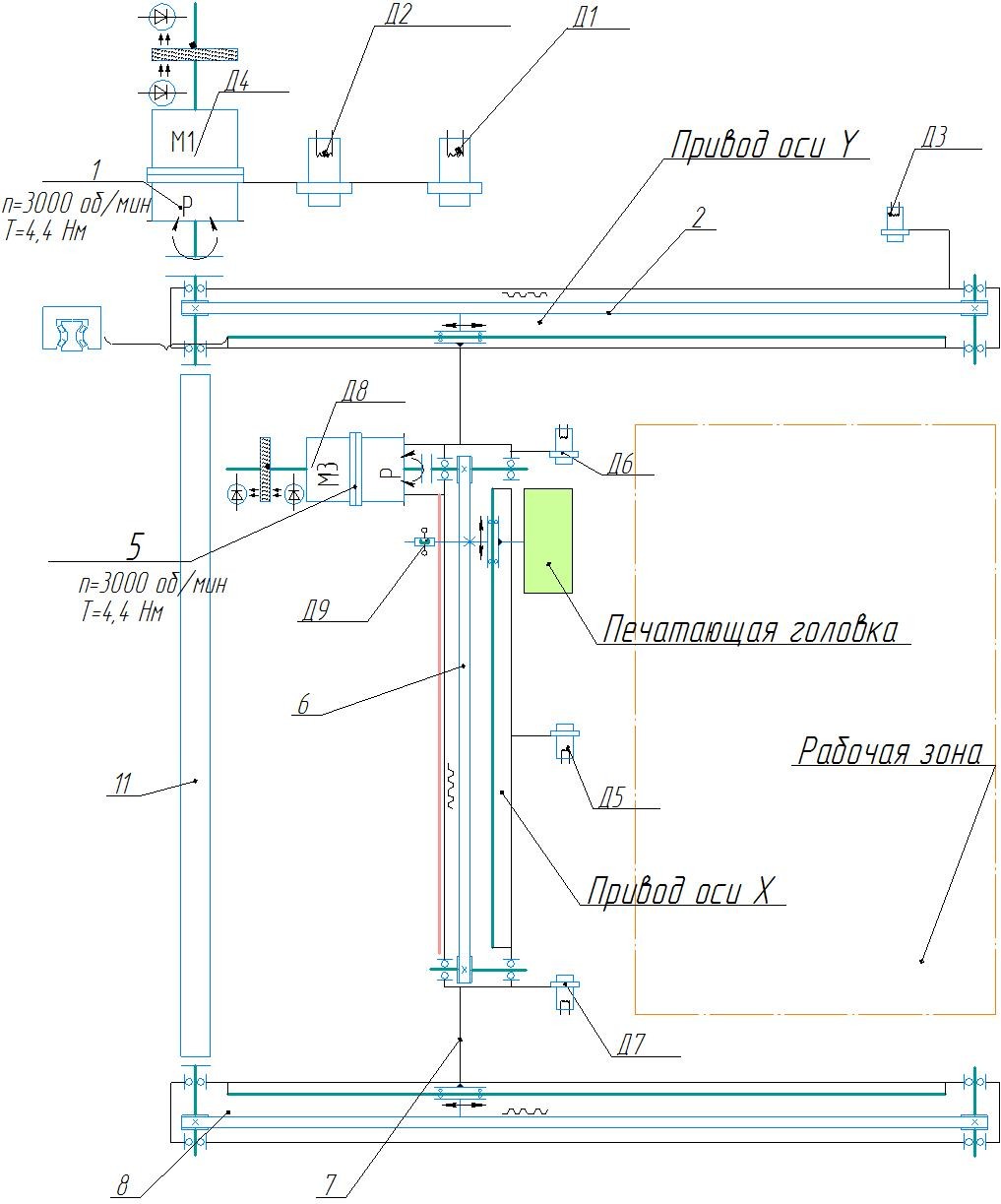
Рисунок 2.3.1 – Кинематическая схема подсистемы нанесения связующего материала.
Индуктивные датчики (D1, D5) используются для определения основного положения. Концевые датчики D2, D3, D6, D7 контролируют наличие SG в разрешенном диапазоне движения и предотвращают возникновение чрезвычайных ситуаций. Линейный энкодер D9 (управляемый магнитным полем с помощью датчика Холла) используется в качестве часов для выдавливания связующего материала из рабочей среды.
Печатающие головки вводят связующее в песчаный слой, чтобы сформировать геометрию одной части модели, которая перемещается по оси X и постепенно по оси Y по всей ширине печатающей головки. Схема движения узла печатающей головки в рабочей зоне представлена на рисунке 2.3.2.
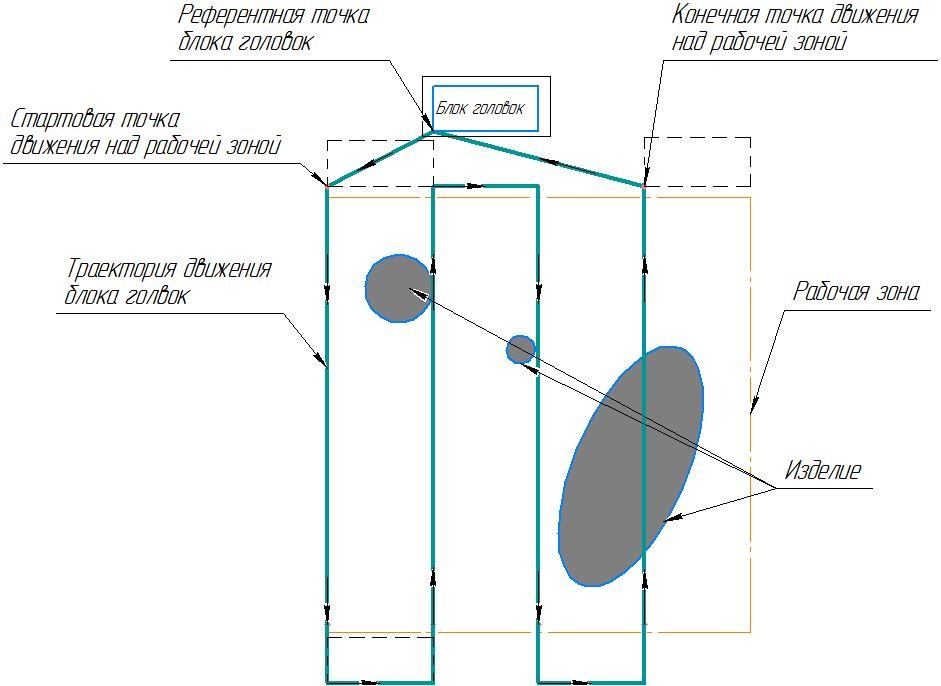
Рисунок 2.3.2 – Схема движения блока рабочего тела по рабочей зоне.
Усилитель адгезии расширяется по запросу: капля по запросу, капли выходят из сопла после одного звукового сигнала. Каждая печатающая головка в предлагаемой экспериментальной установке имеет 300 сопел. Печатающие головки перемещаются на постоянное расстояние по рабочей поверхности.
После выброса каждая капля движется по направлению движения, а затем падает в слой песка.
Схема распределения капель показана на рисунке 2.3.3.
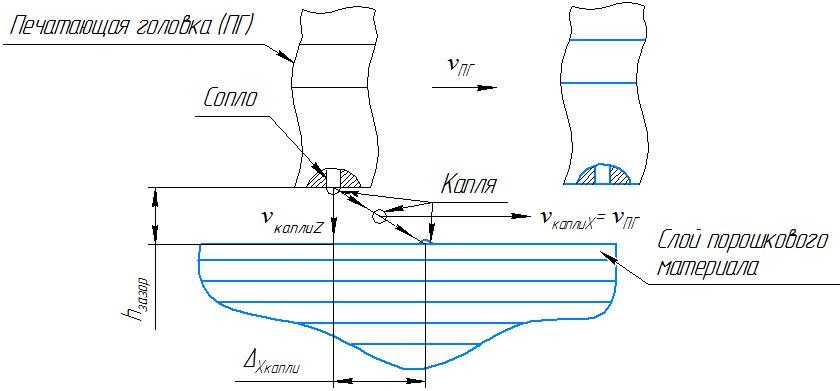
Рисунок 2.3.3 – Схема выброса и смещения капли из ПГ.
Факторы, вызывающие отклонение координат точки приложения капли вяжущего от расчетных, по осям различны. Для оси X:
а) отклонение траектории дрейфа из-за выброса капель из сопла;
б) отклонение координаты точки впрыска, погрешность сигнала выброса капли;
в) отклонение скорости истечения капель из сопла;
г) отклонение координат точки приложения из-за уменьшения скорости капли по отношению к сопротивлению воздуха для капель разного размера;
д) Отклонение координат точки приложения из-за изменения скорости, вызванной изменением плотности распределения точек по оси.
Для оси Y только два параметра влияют на координату падения точки:
а) отклонение траектории капель, вызванное ошибкой при выпадении из сопла;
б) Ошибка позиционирования PG по оси Y
Отклонение координат точки удара из-за отклонения траектории движения капли из-за ошибки выброса капли из сопла.
Каждая печатающая головка содержит от 100 до 2000 индивидуально управляемых сопел, в зависимости от модели и производителя печатающей головки.
Когда печатающие головки отклоняются от оси сопла, из каждого сопла выбрасывается капля (рисунок 2.3.4).
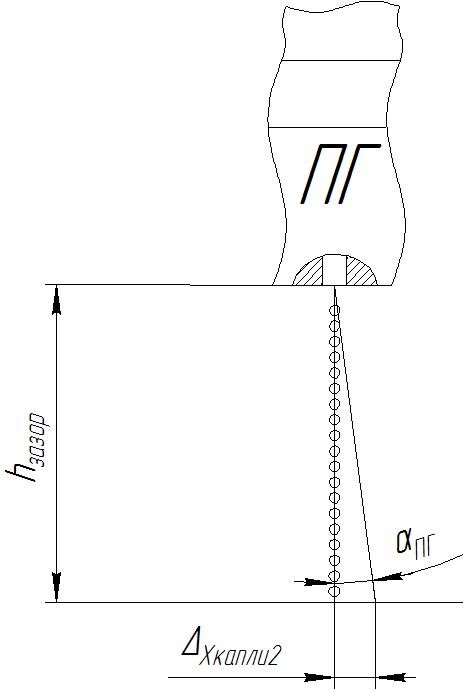
Рисунок 2.3.4 – Схема отклонения падения капли.
Размер этого угла зависит от конструкции печатающей головки, на которую наносится клей, а также от самого клея.
На стенде Jet Expert было проведено исследование по определению отклонения траектории полета при падении от вертикали с использованием рабочей жидкости на основе фурановой смолы (рис. 2.3.5).
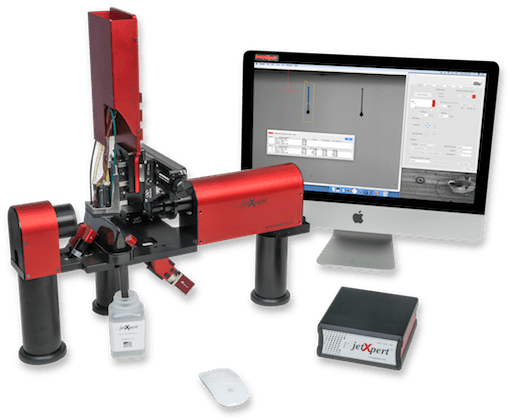
Рисунок 2.3.5 – Стенд для экспериментального исследования процесса выброса капли
Эти инструменты используются для изучения образования, отделения и выброса капли рабочей жидкости из печатающих головок. Аналогичные исследования проводятся для разработки новых чернил для полиграфической промышленности, производства новых печатающих головок и их тестирования.
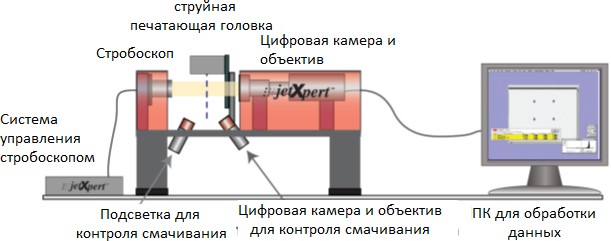
Рисунок 2.3.6 – Схема стенда для экспериментального исследования процесса выброса капли JetExpert.
Консоль содержит (схема консоли показана на рисунке 2.3.6). Высокоскоростная основная цифровая камера, стробоскоп, система управления стробоскопом и печатающей головкой, а также цифровая камера и подсветка для контроля смачивания поверхности печатающей головки. Информация с цифровой камеры передается на компьютер с помощью специального программного обеспечения ImageExpert. Выброс капель синхронизируется со вспышкой и записью видео. Изображение передается на ПК, где изображение автоматически обрабатывается и измеряются его параметры.
Было проведено исследование выбросов парниковых газов для оценки систематических ошибок при использовании гидравлических жидкостей на основе фурана. В ходе исследований автор сделал 6000 капель рабочей жидкости из 300 форсунок, по 20 ходов из каждой форсунки. Результаты показаны на Рисунке 2.3.7.
Стандартное отклонение этого образца рассчитывается по следующей формуле
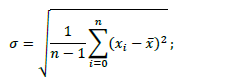
???????? — i-й элемент выборки; n — объём выборки; ????̅ — Среднее арифметическое для образца (диаметр образца)
В результате исследования было обнаружено, что стандартное отклонение пути падения для соответствующей печатающей головки составляет ???? = 3.1 ∙ 10−3 рад.

Колтичество капель
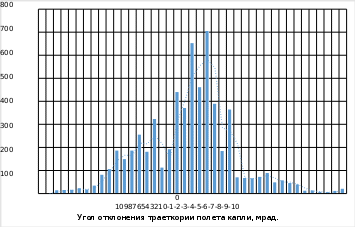
Отклонение от вертикали - это случайная ошибка, соответствующая гауссовскому (нормальному) распределению.