ВУЗ: Не указан
Категория: Не указан
Дисциплина: Не указана
Добавлен: 09.11.2023
Просмотров: 273
Скачиваний: 2
СОДЕРЖАНИЕ
1 Анализ исходных данных и известных решений по ремонту ковша экскаватора ELAZ 880 Bl
1.2 Сведения о материале ковша экскаватора ELAZ 880 Bl и оценка его свариваемости
1.3 Базовая технология ремонтной сварки ковша экскаватора ELAZ Bl 880
1.4 Обоснование выбора способа ремонтной сварки ковша экскаватора ELAZ Bl 880
1.5 Формулировка задач выпускного квалификационного проекта
2 Технологический процесс ремонта ковша экскаватора ELAZ 880BL
3 Выбор оборудования для ремонта ковша экскаватора
3.4 Источник питания и подающий механизм
4 Безопасность и экологичность технического объекта
4.2 Идентификация профессиональных рисков
4.3 Методы и средства снижения профессиональных рисков
4.4 Обеспечение пожарной безопасности
4.5 Обеспечение экологической безопасности технического объекта
5 Оценка экономической эффективности выпускной квалификационной работы
5.2 Расчёт фонда времени работы оборудования
5.4 Расчёт заводской себестоимости вариантов технологии
5.5 Оценка капитальных затрат по базовой и проектной технологиям
5.6 Расчёт показателей экономической эффективности
Известно, аргонодуговая сварка рисунок 8 это разновидность электродуговой сварки, только с неплавящимся электродом и другим принципом защиты сварочной ванны. Дуга зажигается между изделием, к которому присоединена масса, и вольфрамовым электродом. Он не плавится, зато температуры дуги достаточно, чтобы плавить кромки металла. Колебаниями электрода можно управлять сварочной ванной, регулируя скорость сварки, ширину шва, глубину проплавления. Так же данная сварка для ремонта ковша имеет ряд преимуществ, такие как: надежная изоляция от окружающей среды, повышение качества и отсутствие нарушений кристаллической решетки в соединенной поверхности, показательная тепловая мощность дугового разряда, что положительно сказывается на качестве и скорости сварки, весь процесс может быть произведен под наблюдением. Однако недостатки данной сварки заключаются в том, что оборудование в настройке сложное, а квалификация сварщика напрямую будет влиять на производительность.
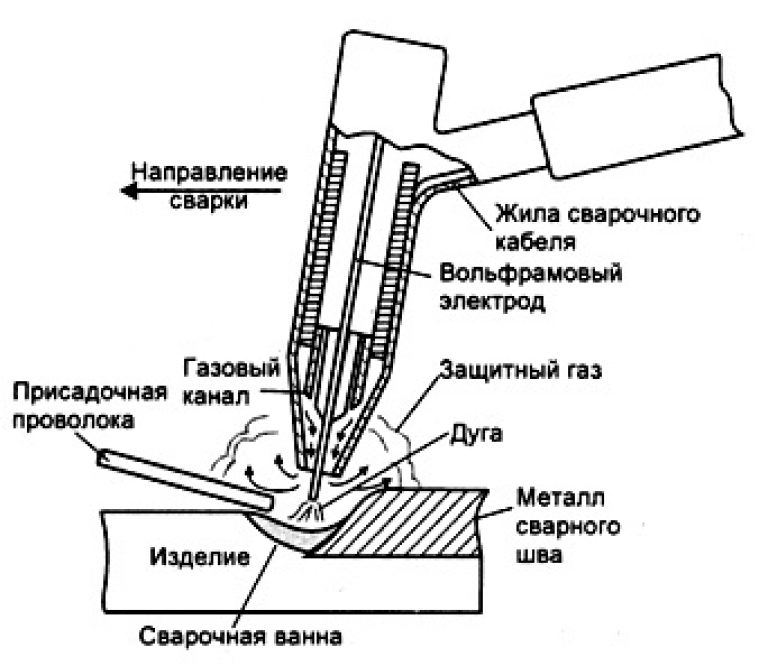
Рисунок 8 – Схема осуществления аргонодуговой сварки
Следовательно, на основании проведенного анализа возможных способов сварки выбран способ механизированной сварки в защитных газах проволокой сплошного сечения.
1.5 Формулировка задач выпускного квалификационного проекта
Данная выпускная квалификационная работа посвящена повышению производительности сварочных процессов при ремонтной сварке ковша экскаватора ELAZ Bl880. Во введении сформулирована цель – повышение производительности ремонтной сварки ковша экскаватора-погрузчика ELAZ Bl 880.
Анализ конструкции изделия позволил заключить, что рассматриваемая конструкция является технологичной, и автоматизация сварки его швов является оправданной.
При выполнении базовой технологии ремонтной сварки ковша применяется ручная дуговая штучными электродом.
Однако сварка штучным электродом обладает рядом недостатков:
1) повышенное разбрызгивание электродного металла (ограничение на ток сварки и производительность, потери металла);
2) низкая пластичность наплавленного металла.
На основании анализа возможных способов сварки принято решение заменить ручную дуговую сварку штучными электродами – на механизированную сварку в защитных газах проволокой сплошного сечения.
На основании вышесказанного можно сформулировать задачу выпускного квалификационного проекта, последовательное решение которой позволит достигнуть поставленной цели:
-
разработка технологического процесса ремонтной сварки ковша; -
выбор возможного оборудования для проектного варианта ремонтной сварки ковша экскаватора ELAZ 880Bl.
2 Технологический процесс ремонта ковша экскаватора ELAZ 880BL
Проектный технологический процесс ремонта ковша экскаватора, включает в себя операции: 1) Дефектация; 2) Очистка поверхности; 3) Выборка дефектов; 4) Обезжиривание поверхностей, 5) Ремонтная сварка; 6) Контроль качества.
2.1 Дефектация
В начале проектной технологии проводится дефектация. Осматривается поврежденная область ковша (рисунок 9). Рабочий размечает все дефекты, имеющиеся на изделии маркером. Освещение должно быть не менее 500Лк. Вспомогательные приспособления: лупа, рулетка, штангенциркуль.
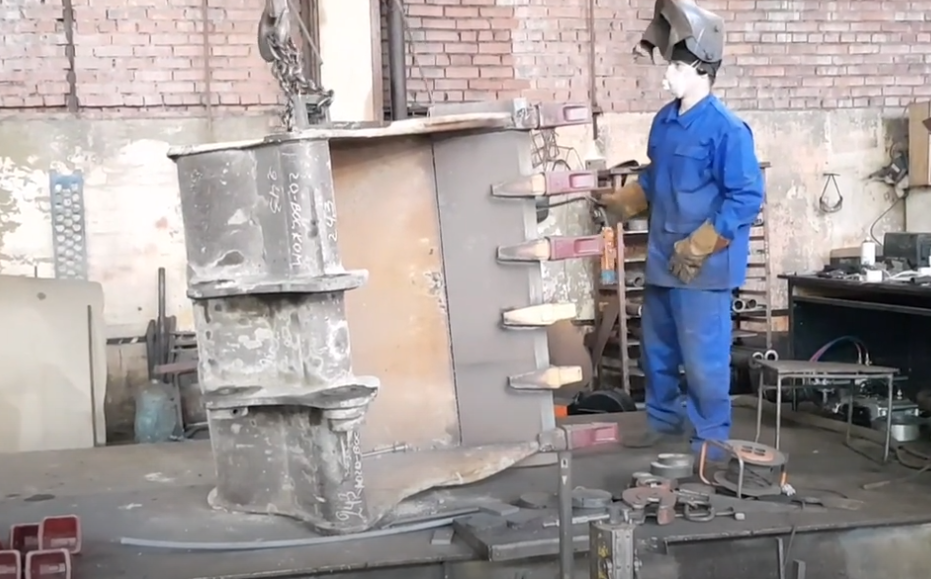
Рисунок 9 – Дефектация ковша экскаватора
2.2 Очистка поверхности
Вторым этапом необходимо произвести очистку ковша от ржавчины, старой краски и других загрязнений с помощью шлифовальной машины ИЭ-2106 (рисунок 10). Важно проверить соответствие насадки техническим требованиям и начинать только после достижения болгаркой максимальных оборотов. После чего стропальщик закрепляет стропы за проушину ковша и с помощью мостового крана устанавливают ковш экскаватора в положение «вверх днищем», для предоставления к трещине на задней стенке ковша.
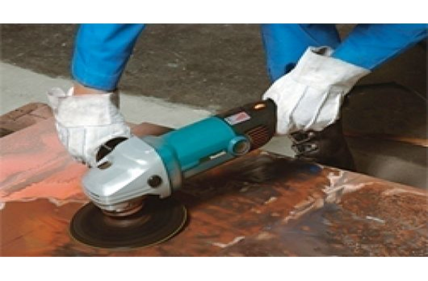
Рисунок 10 – Отчистка поверхности ковша экскаватора
2.3 Выборка дефектов
На третьем этапе операции оператору необходимо произвести разделку кромок. Трещины разделываются кромкофрезерной машиной ЕКФ 450 с торцевой фрезой, выдерживая размеры, угол разделки кромок 25°±2. Разделку трещины нужно выполнить на всю глубину до чистого металла. Подготовленные кромки под ремонтную сварку должно соответствовать ГОСТ 14771-78. После этого производят сверление отверстий по концам трещины d = 7 мм. Выполнение данной операции производится с применением сетевой ударной дрели ЗДУ-780 ЭРКМ2 (рисунок 11).
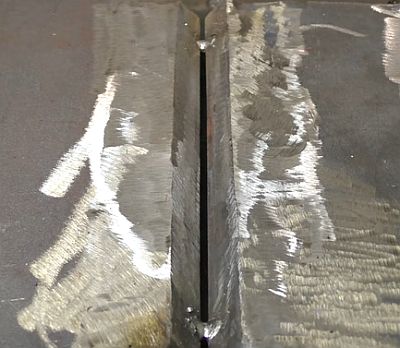
Рисунок 11 - Выборка трещин на участке ковша экскаватора
2.4 Обезжиривание поверхности
После выборки дефектов на четвёртой операции производят обезжиривание поверхности. Эта операция происходит с применением растворителя 646 (рисунок 12). Перед обезжириванием поверхность следует тщательно просушить. После промежутка времени, когда раствор испарится, так же следует просушить поверхность.
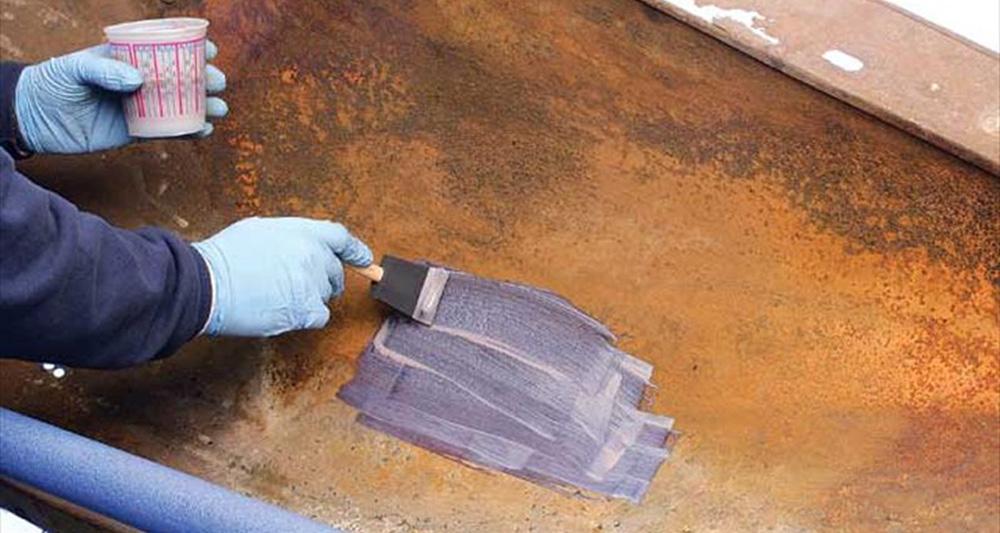
Рисунок 12 – Обезжиривание участка ковша экскаватора
2.5 Ремонтная сварка ковша ELAZ 880 Bl
Для защиты сварочной ванны и перегретого металла применим газовую смесь (Ar 70% + CO2 30%).
Качество сварочной проволоки должно соответствовать ГОСТ 2264. Упаковка сварочных материалов должна быть проведена согласно требованиям, ТУ на эти материалы. Обязательно наличие сертификатов предприятия-изготовителя, которые удостоверяют качество поставленной сварочной проволоки. Очищенная и намотанная в кассеты сварочная проволока должна храниться в закрытых помещениях, температура в которых не опускается ниже +15 С. При этом на каждой кассете с проволокой на видном месте необходимо выполнить маркировку несмываемой краской. При намотке проволоки на кассеты следят за тем, чтобы не было перегибов. Сварочные проволоки в зависимости от
условий поставки могут быть полированными, омеднёнными или осветлёнными. Перед запуском необходимо убедиться в исправности пусковой системы, проверить на герметичность все шланги.
Для механизированной сварки (выполнение швов малой протяжённости) применяется проволока сплошного сечения диаметром 1,14 мм марки L-56 производства Lincoln Electric.
Таблица 5 – Химический состав проволоки SuperArc L-56
Углерод | Марганец | Кремний | Сера | Фосфор | Медь |
0,05...0,15 % | 1,40...1,85 % | 0,80...1,15 % | < 0,035 % | < 0,025 % | до 0,50 % |
Таблица 6 – Механические свойства наплавленного металла проволокой SuperArc L-56
Предел прочности, МПа | Предел текучести, МП+ а | Относит. удлин., % | Ударная вязкость при -20 С, Дж |
564 | 468 | 29 | 54 |
Для выполнения сварки швов малой протяжённости применим источник питания Invertec STT-II и полуавтомат LF-33 (рисунок 13).
Таблица 7 – Параметры режима сварки проволокой SuperArc L-56 диаметром 1,14 мм [16]
Скорость подачи проволоки, мм/мин | Пиковый ток, А | Сварочный ток, А | Базовый ток, А | Расход газа, л/мин | Вылет проволоки, мм |
228...170 | 400...420 | 150...170 | 35...55 | 10...12 | 10...16 |
В процессе сварки оператор проверяет:
- режим сварки;
- размеры накладываемых слоев шва и окончательные размеры шва.
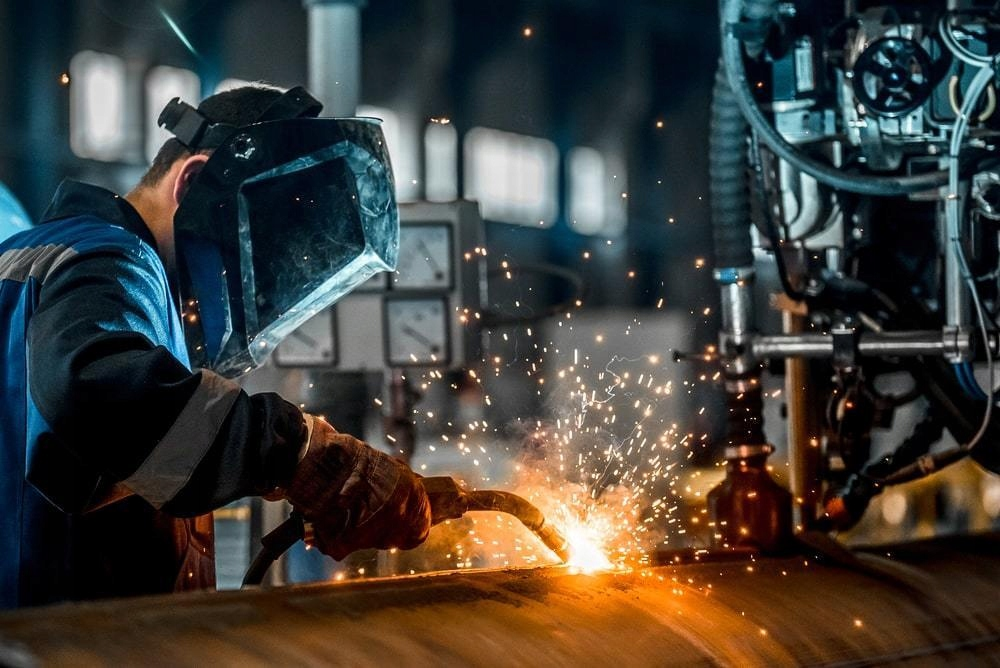
Рисунок 13 - Механизированная сварка проволокой сплошного сечения в смеси защитных газов
2.6 Контроль качества
Завершающим этапом является контроль качества (рисунок 14). Сварные соединения стальных конструкций должны подчиняться требованиям:
- внешний осмотр с проверкой геометрических размеров и формы швов в объеме 100 %;
- неразрушающими методами в объеме не менее 0,5 % длины швов.
Контроль швов сварных соединений конструкций неразрушающими методами следует проводить после исправления недопустимых дефектов, обнаруженных внешним осмотром. Выборочному контролю швов сварных соединений, качество которых согласно проекту, требуется проверять неразрушающими физическими методами, должны подлежать участки, где наружным осмотром выявлены дефекты, а также участки пересечения швов.
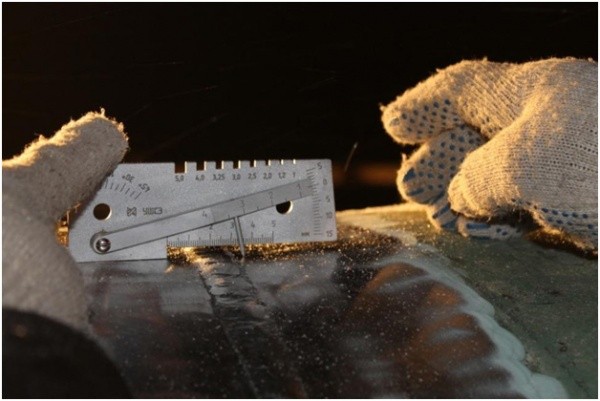
Рисунок 14 – Контроль качества сварных соединений