ВУЗ: Не указан
Категория: Не указан
Дисциплина: Не указана
Добавлен: 09.11.2023
Просмотров: 300
Скачиваний: 2
СОДЕРЖАНИЕ
1 Анализ исходных данных и известных решений по ремонту ковша экскаватора ELAZ 880 Bl
1.2 Сведения о материале ковша экскаватора ELAZ 880 Bl и оценка его свариваемости
1.3 Базовая технология ремонтной сварки ковша экскаватора ELAZ Bl 880
1.4 Обоснование выбора способа ремонтной сварки ковша экскаватора ELAZ Bl 880
1.5 Формулировка задач выпускного квалификационного проекта
2 Технологический процесс ремонта ковша экскаватора ELAZ 880BL
3 Выбор оборудования для ремонта ковша экскаватора
3.4 Источник питания и подающий механизм
4 Безопасность и экологичность технического объекта
4.2 Идентификация профессиональных рисков
4.3 Методы и средства снижения профессиональных рисков
4.4 Обеспечение пожарной безопасности
4.5 Обеспечение экологической безопасности технического объекта
5 Оценка экономической эффективности выпускной квалификационной работы
5.2 Расчёт фонда времени работы оборудования
5.4 Расчёт заводской себестоимости вариантов технологии
5.5 Оценка капитальных затрат по базовой и проектной технологиям
5.6 Расчёт показателей экономической эффективности
Таблица 2 – Механические свойства стали 15ХСНД в соответствии с ГОСТ 19281-2014
![]() | ![]() | δ, % |
740 | 640 | 20 |
Сталь 15ХСНД имеет сильную склонность к образованию закалочных структур [5]. После анализа литературных источников стало понятно, что при ремонтной сварке деталей и агрегатов узлов из стали 15ХСНД часто проявляются дефекты такие как: 1) Горячие трещины; 2) Непровар сварного шва; 3) Пористость шва. При тщательном анализе корневых причин появления горячих трещин следует подчеркнуть, что:
- увеличивается время между сваркой и термообработкой;
- высокую скорость охлаждения металла шва;
- низкое качество основного металла.
На рисунке 3 представлен пример горячих трещин, которые могут возникать ремонтной сварки ковша ELAZ Bl 880.
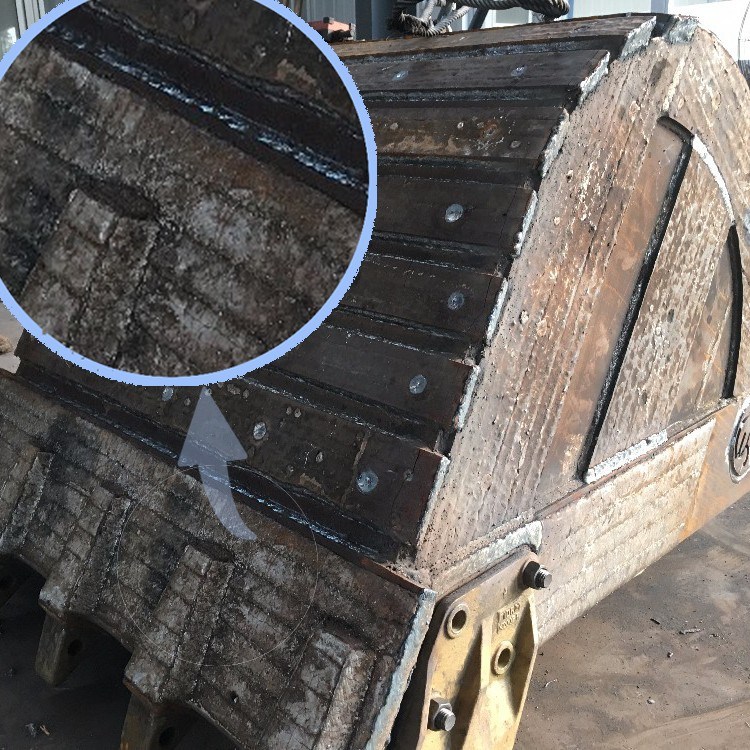
Рисунок 3 – Горячие трещины
Конструкция ковша подвергается различным нагрузкам и деформациям, что в результате приводит к образованию трещин разной длины. Из способов борьбы с горячими трещинами можно произвести пример, который заключается в тщательном заплавлении кратеров, из-за которых собственно говоря и возникают трещины.
«Так же рассмотрим способы борьбы с проблемами при сварке стали 15ХСНД. Действенным средством против образования закалочных структур при сварке стали 15ХСНД является предварительный подогрев, который способствует перлитному превращению. Путём изменения скорости охлаждения становится возможным получение желаемой твёрдости металла в зоне термического влияния. Далее рассмотрим способ борьбы с непроварами нужно учесть «Выбор параметров режима сварки должен выполняться с учётом построенной для стали 15ХСНД термокинетической диаграммы рисунок 4 [21]. Эта диаграмма показывает начало и окончание аустенитного превращения при различных скоростях охлаждения металла. Как видно из диаграммы, увеличение скорости охлаждения приводит к измельчению структуры в зоне термического влияния и повышению её твёрдости. Образование закалочных структур при сварке стали
15ХСНД происходит в случае превышения скорости охлаждения критической скорости» [9].
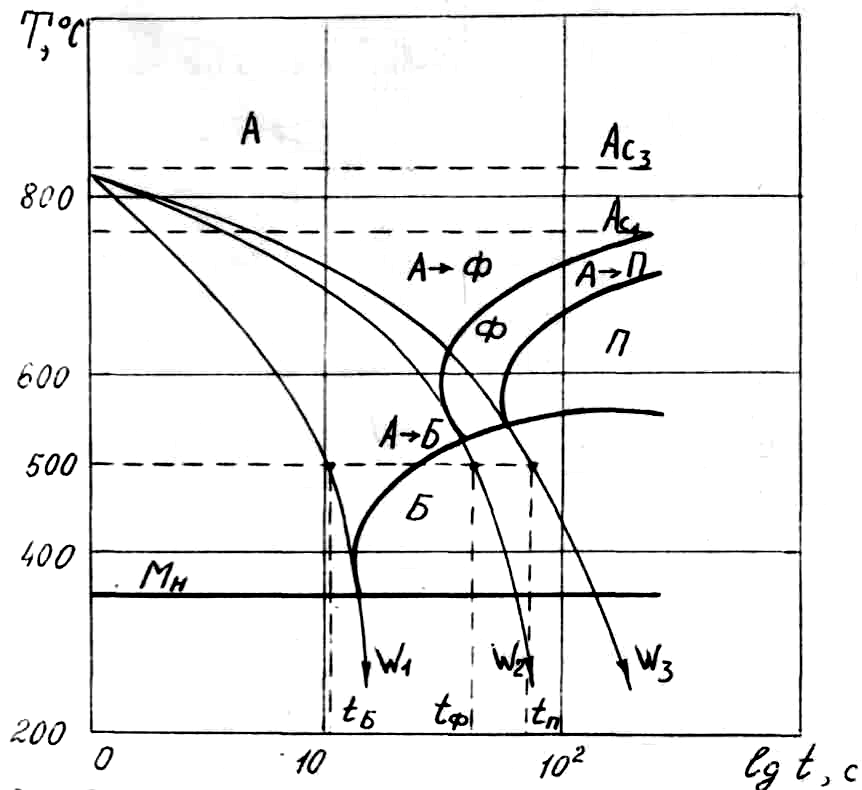
Рисунок 4 – Термокинетическая диаграмма для стали 15ХСНД
Как правило, для сварки этих сталей применяют электроды марки ДСК-50 d = 5-6 мм. Данные по химическому составу приведены ниже в таблице 3 и механические свойства электрода приведенной в таблице 4. В роли аналога данного электрода можно применить Э55, перед сваркой электроды нужно прокаливать.
Таблица 3 –Химический состав электродов Э50А в соответствии с ГОСТ 9467-75
C | Si | Mn | Ni | S | P |
0,09 | 0,42 | 0,83 | 0,3 | 0,022 | 0,024 |
Таблица 4 – Механические свойства металла шва Э50А в соответствии с ГОСТ 9467-75
![]() | ![]() | δ, % |
740 | 410 | 29 |
1.3 Базовая технология ремонтной сварки ковша экскаватора ELAZ Bl 880
Технология ремонтной сварки ковша ELAZ 880Bl, предусматривает выполнение следующих операций: 1) Входной контроль; 2) Разделка кромок; 3) Сверление отверстий; 4) Зачистка под сварку; 5) Обезжиривание поверхности: 6) Заварка трещины; 7) Контроль качества готовой продукции.
Первой операцией производится входной контроль.
Перед началом сварки проверяется:
-
наличие у сварщика допуска к выполнению работы; -
наличие документов, подтверждающих положительные результаты контроля сварочных материалов; -
состояние сварочного оборудования или наличие документа, подтверждающего надлежащее состояние оборудования; -
температура предварительного подогрева свариваемых деталей (если таковой предусмотрен научно технической документации или производственной научной документации).
На второй операции производится разделка кромок трещины-кромкофрезерной машиной с торцевой фрезой.
После выполняют сверление отверстий по концам трещины и их зенкерование.
На четвертой операции производится зачистка путем шлифования места под сварку, с применением шлифовальной машины.
Далее выполняется обезжиривание обработанной поверхности растворителями.
На шестой операции выполняется заварка трещины. Ремонтную сварку можно произвести с помощью сварочного выпрямителя ВД-252 или аналогов. Сварку ведут на постоянном токе обратной полярности. Электроды применяют марки ДСК-50 d = 5-6мм (ГОСТ 9467-75), так же возможно применение аналогов.
Завершающей операцией является контроль качества. После ремонтной сварки прошедший контроль ковш эскалатора перемещают на участок подготовительной окраски.
1.4 Обоснование выбора способа ремонтной сварки ковша экскаватора ELAZ Bl 880
Выбор способа сварки предусматривает анализ конструктивных особенностей изделия, возможностей конкретного производства и местоположения, а также достижений в области сварочных технологий.
В числе основных критериев, на которые следует обратить внимание при выборе способа сварки, следует назвать:
1) свойства и толщина металла заготовок;
2) геометрия сварных швов;
3) при выборе того или иного способа сварки следует руководствоваться приоритетом механизированных способов перед ручными и автоматическими способами перед механизированными;
4) оценка преимуществ и недостатков способов сварки.
Анализ свойств и толщины заготовок. Поскольку рассматриваемая сварная конструкция выполняется из стали 15ХСНД, то ограничений по свариваемости нет, а значит можно сделать вывод о применимости всех известных способов сварки. Рассмотрим следующие способы сварки:
1) ручная дуговая сварка штучными электродами;
2) механизированная сварка самозащитной порошковой проволокой;
3) автоматическая сварка под флюсом;
4) аргонодуговая сварка
Анализ геометрии сварных швов. Рассматриваемая сварная конструкция ковша имеет протяжённые швы.
При выполнении длинномерных швов целесообразно применение:
1) автоматической сварки под флюсом;
2) автоматической сварки проволокой сплошного сечения в защитных газах.
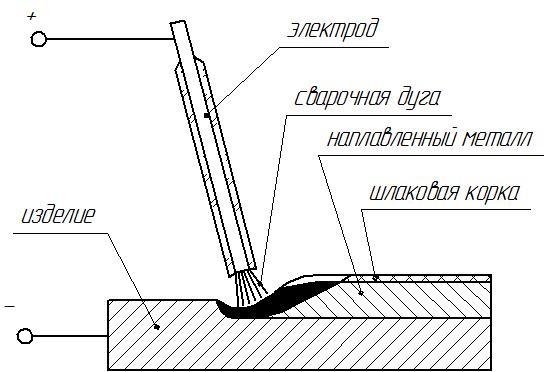
Рисунок 5 – Схема осуществления ручной электродуговой сварки
штучными электродами
В настоящее время доля сварных конструкций, получаемых с применением ручной дуговой сварки штучными электродами, значительно снижается. Это можно объяснить тем, что данный способ сварки обладает рядом недостатков. В первую очередь, следует подчеркнуть невысокую производительность выполнения сварочных работ, в настоящее время ресурс повышения скорости сварки и наплавки штучными электродами за счёт назначения оптимальных режимов и сварочных материалов полностью выработан. Вторым недостатком следует признать работу сварщика в тяжёлых условиях, которые приводят к возникновению профессиональных заболеваний и заставляют увеличивать расходы на обеспечение безопасности персонала. Третьим недостаток следует выделить низкую стабильность качества сварки, которая в значительной мере зависит от профессионализма и кондиции сварщика. Четвёртым недостатком следует признать повышенный расход электродного материала на угар и разбрызгивание, а также на огарки. Необходимость смены электродов не только приводит к увеличению расхода сварочных материалов, но и снижает производительность и качество сварочных работ.
Из-за множественных недостатков ручной дуговой сварки штучными электродами она повсеместно заменяется более производительными и перспективными способами сварки.
Хорошо известно, что у способа сварка в смеси защитных газов для ремонтной сварки ковша экскаватора, рисунок 6 можно выделить следующие преимущества: 1) высокая производительность сварки; 2) не образуется шлаковая корка; 3) улучшаются условия труда сварщика; 4) возможность сварки во всех пространственных положениях.
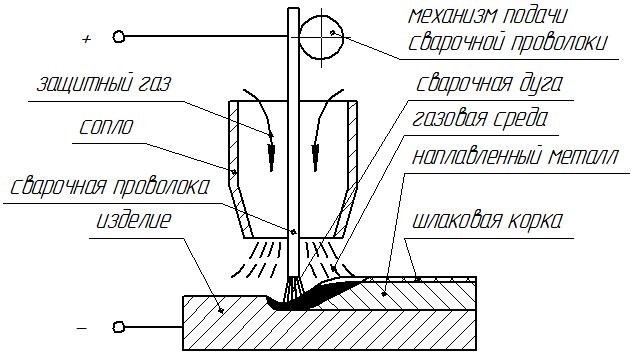
Рисунок 6 – Схема осуществления сварки в среде защитных газов
Известно, что данный способ сварки обладает рядом недостатков. Можно выделить следующие недостатки при сварке в смеси защитных газов: наличие газовых баллонов (ограниченная подвижность сварщика), повышенное разбрызгивание электродного металла (ограничение на ток сварки и производительность, потери металла), низкая пластичность наплавленного металла (опасность получения трещин).
Так же хорошо известно, что значительные усилия исследователей направлены на повышение эффективности механизированной и автоматической сварки в среде защитных газов посвящено большое количество работ [13, 10, 11, 19, 17]. Показано, что повышение качества и производительности сварки в защитных газах, расширение области её применения возможно при управляемом переносе расплавленного электродного металла в сварочную ванну.
Сварка самозащитными порошковыми проволоками, рисунок 7 хорошо сочетает в себе преимущества ручной дуговой сварки и сварки в защитных газах. Применение самозащитной порошковой проволоки позволяет отказаться от использования газовой аппаратуры (редукторы, смесители газов, баллоны, осушители, шланги), которые в значительной мере снижают мобильность сварщика [17,18].
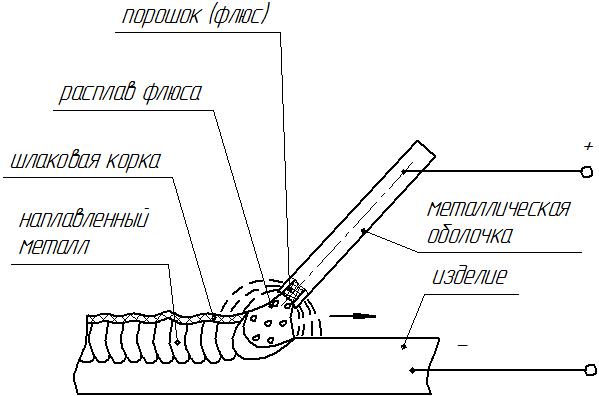
Рисунок 7 – Схема осуществления сварки самозащитной
порошковой проволокой
Однако сварка самозащитной порошковой проволоки обладает следующими недостатками: 1) Необходимость удаления шлаковой корки с поверхности шва; 2) высокая стоимость порошковой проволоки; 3) сильное порообразование и возможность получения дефектов в виде пор и шлаковых включений; 4) необходимость борьбы с заломами сварочной проволоки из-за её излишней мягкости. Как вывод можно сказать, что данный способ весьма дорогостоящий и затратный, для ремонтной сварки ковша экскаватора.