ВУЗ: Не указан
Категория: Не указан
Дисциплина: Не указана
Добавлен: 09.11.2023
Просмотров: 125
Скачиваний: 2
СОДЕРЖАНИЕ
Описание конструкции оборудования и принцип действия оборудования
Производственный цикл в котором участвует обрабатывающий центр Integrex 300-IV ST
Перечень документов для проведения ремонтных работ.
Предварительная дефектная ведомость :
Технология ремонта оборудования.
Наименование и краткая характеристика выявленных дефектов зубчатого колеса.
Термическая обработка закалка и отпуск
Наименование и краткая характеристика выявленных дефектов вала
РЕГУЛЯРНЫЙ ОСМОТР И ТЕХНИЧЕСКОЕ ОБСЛУЖИВАНИЕ
Список мероприятий технического осмотра:
Осмотр во время работы (после подачи питания)
Еженедельный техосмотр или через 60 часов работы
Раз в полгода или через 1500 часов работы
Ежегодный или через 3000 часов работы
Соблюдение правил ТБ при проведении технического обслуживания
Предварительная дефектная ведомость :
составляется за 2 - 3 месяца до начала работы на основе планового осмотра и опроса обслуживающего персонала.
После разборки оборудования и дефектации, предварительная дефектная ведомость уточняется, дополняется и составляется окончательная дефектная ведомость.
В предварительную дефектную ведомость должны быть записаны дета-ли, которые будут заменяться при ремонте новыми, а также детали, которые хотя и не заменяются, но ремонт их потребует разработки технологии, изготовления чертежей, специального инструмента, приспособлений, переделки чертежей на отдельные узлы и т. д. В предварительную дефектную ведомость вносится все то, что можно сделать до начала ремонта, чтобы сократить его продолжительность и не создавать каких-либо затруднений при ремонте. Также записываются все детали, имеющиеся на центральном складе запасных частей. В этом случае в дефектной ведомости указывается, где взять запасную деталь.
Подготовку к составлению предварительной дефектной ведомости проводит конструкторское бюро, которое должно иметь план подготовок на каждый месяц года, а на данный месяц график остановки каждого станка. Конструктор к этим срокам подбирает альбом чертежей, восстанавливает
недостающие чертежи и производит изменения, если это требуется, в существующих конструкциях отдельных деталей и узлов.
Составление предварительной дефектной ведомости производит инспектор по оборудованию совместно с механиком цеха и конструкторами.
Дефектная ведомость с подобранными чертежами поступает в плановое бюро, которое выдает заказы на изготовление заготовок и деталей, а затем в технологическое бюро, которое разрабатывает технологические процессы, конструкции специального инструмента и необходимых приспособлений
, и передает дефектные ведомости с разработанной технологической документацией на участок ремонтного цеха.
Во время разборки станка для ремонта предварительная дефектная ведомость уточняется, отчасти изменяется и, главным образом, дополняется. После этого предварительная дефектная ведомость становится рабочей дефектной ведомостью, которой предусмотрено уже все до мелочей, не включенных в предварительную дефектную ведомость.
Рабочая дефектная ведомость :
должна ясно показывать, какие детали и в какой последовательности по узлам заменяются новыми: Указываются способы сочленения старых деталей с новыми. В ней должны быть перечислены все работы вплоть до снятия станка с фундамента, разборки, транспортировки в ремонтный цех и всех сопутствующих работ, ремонта всех ограждений и кожухов, испытания на стенде и на производстве, монтажа на месте после ремонта с установкой электропроводки и сдачей станка ОТК и цеху.Подпись механика цеха-заказчика на дефектной ведомости обязательна. Это необходимо потому, что механик изучает станок в процессе его эксплуатации и может дать ряд ценных указаний, которые можно использовать при ремонте.
Таблица 6 - дефектная ведомость для ремонта станка Integrex
№ | Наименование детали | Наименование дефекта, величина износа | Перечень работ при ремонте | Примечание |
1 | Зубчатое колесо | скол зуба | Наплавка, зубофрезерование | |
2 | Блок-шестерня | износ зуба 65% | изготовить венец | |
3 | Вал | Износ более чем на 10% | наплавка, мехобработка | |
4 | Втулка | износ отверстия | наплавить, расточить | |
5 | Подшипник | износ беговой дорожки внутри кольца | заменить | |
6 | Станина | Износ направ-ляющих до 10% | заменить | |
Технология ремонта оборудования.
Ремонт металлорежущих станков начинается с подготовительного этапа, в результате которого станок внимательно осматривают и определяют дефекты. Техник и мастер по ремонту составляют ведомость, где отражаются выявленные дефекты и прилагаются чертежи подлежащих замене деталей. Дефекты выявляются путем включения оборудования и запуска его работы, в ходе которой замечаются неточности, находящие отражение в журнале записей и подвергающиеся тщательному анализу в целях предотвращения возникновения подобной ситуации в будущем. Затем наступает этап очистки, когда все детали станка, в том числе и его корпус, очищаются от пыли, грязи и смазывающей жидкости, выполняющей роль охлаждения. Чтобы ремонт проходил качественно и посторонние предметы не мешали работнику, место вокруг оборудования освобождают. Так же освобождают внутренние резервуары станка от масла, разъединяют полумуфту, снимают ремни, предварительно отключив станок от питания, готовятся необходимые инструменты и запчасти.
Этап разборки всех частей и деталей станка подразумевает наличие конкретного плана действий, намеченного в результате осмотра. Иногда требуется разобрать только часть оборудования без осмотра ее деталей. Иногда требуется разобрать полностью все детали и механизмы станка, чтобы ясно представлять себе картину восстановления его работы. Поэтому объем ремонтных работ в каждом случае индивидуален. Однако существуют особые правила, согласно которым необходимо разбирать станок. К ним относятся:
1. Соблюдение последовательности разбора: от отдельных частей до деталей. Иначе нарушается плотность соединения механизмов;
2. Ознакомление с паспортом станка, схемами его деталей, составление графика разборочно-сборочных работ;
3. Составление кинематической и гидравлической схем в случае их отсутствия;
4. Составление дефектной ведомости после проверки всех деталей на наличие отклонений в работе;
5. Разборку следует организовывать таким образом, чтобы обеспечить доступ к основным частям оборудования, поэтому сначала снимаются вспомогательные детали, такие как: дверцы, щитки, крышки, кожухи и т.д.;
6. Применение только исправных инструментов. Иначе можно повредить годные детали;
7. Использование прессов, съемных или винтовых приспособлений, чтобы снять шкивы, зубчатые колеса, муфты и др. детали;
8. Использование молотков предполагает наличие выколоток или подставок из мягкого металла во избежание повреждений деталей;
9. Подогрев детали для облегчения ее снятия;
10. Аккуратность в снятии деталей, чтобы исключить возможность повреждений;
11. Снятие деталей без применения силы;
12. Маркировка и расположение каждой детали в отдельном ящике позволяет облегчить задачу поиска и хранения;
13. Закрытие ящика крышкой во избежание утраты детали;
14. Расположение крупных деталей на подставках недалеко от станка;
15. Проставление отметок на узлах нерабочих поверхностей;
16. Применение ключей и отверток соответствующей формы к гайкам и болтам;
17. Устранение ржавчины с помощью керосина, раствор которого необходимо оставить на обрабатываемой поверхности на 8-10 часов;
18. Применение механических инструментов при разборке резьбовых соединений;
19. Удаление остатков сломанных деталей.
В результате разборочных работ происходит замена устаревших деталей или их обновление с помощью промывочных растворов – керосина, соды, чистящих и абразивных веществ. Дефективные детали помечают маркером или краской.
Следующий этап – сборка, которую следует проводить согласно чертежам и только после очистительных работ
Наименование и краткая характеристика выявленных дефектов зубчатого колеса.
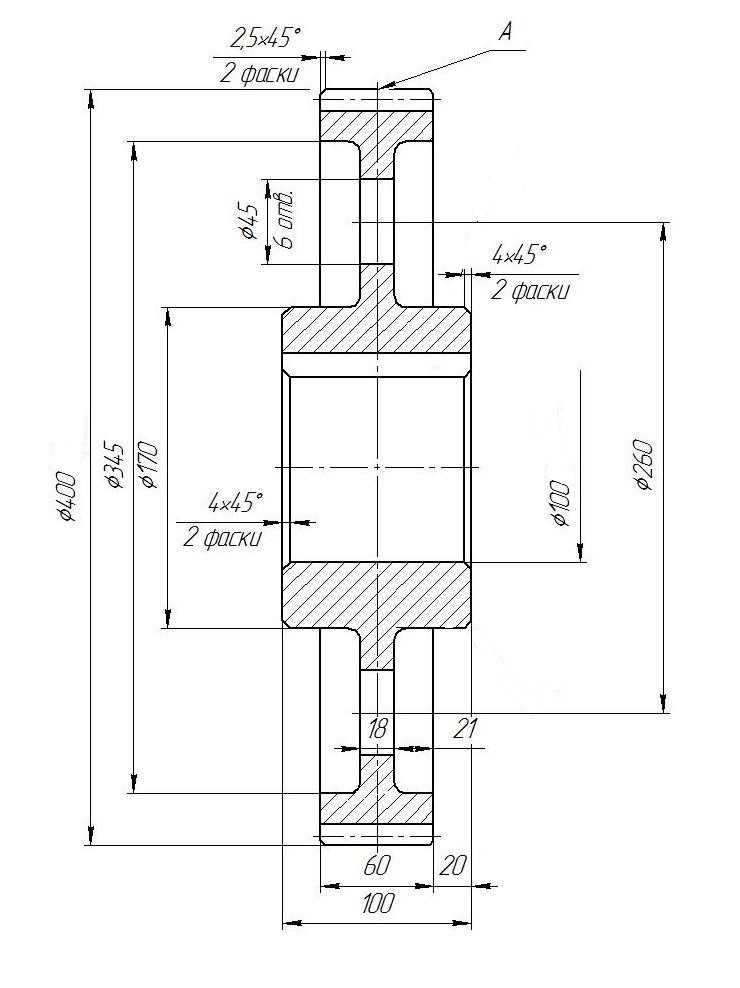
Рисунок 4 – Дефекты зубчатого колеса
Таблица 7 – Карта дефектов
Наименование дефекта | Размер, мм | Способ устранения | |||||
Возможный | Принятый | ||||||
А | Дефект зуба зубчатого колеса по ширине | 6,12 | Наплавка в среде углекислого газа | Наплавка ручной дуговой сваркой |