Файл: Целью данной выпускной работы является проектирование литейного цеха на базе уже имеющегося.docx
ВУЗ: Не указан
Категория: Не указан
Дисциплина: Не указана
Добавлен: 11.01.2024
Просмотров: 332
Скачиваний: 1
СОДЕРЖАНИЕ
1.5 Смесеприготовительное отделение
2 Разработка технологического процесса изготовления отливки «Серьга».
2.1 Обоснование способа формовки
2.2 Обоснование положения детали в форме при заливке
2.3 Обоснование выбора поверхности разъема формы и модели
2.4 Обоснование величины усадки и припусков на механическую обработку, уклонов, галтелей
2.5 Определение конструкции и размеров знаков стержней
2.6.1 Элементы литниковой системы и их назначение
2.6.2 Выбор типа литниковой системы
2.7 Обоснование применяемой оснастки
2.8 Выбор формовочных и стержневых смесей
3. Разработка конструкции прессового агрегата
3.1 Общая компоновка прессовых формовочных машин
3.3 Общее описание рассчитываемого прессового агрегата по типу модели 5833Г
3.4.1 Расчет рычажного механизма прессования
3.4.2 Расчет индикаторных диаграмм
4.1 Анализ опасных и вредных производственных факторов литейного цеха
4.2 Мероприятия по снижению опасных и вредных производственных факторов
4.3 Меры пожарной безопасности цеха
5.1 Анализ состояния окружающей среды ТОО “КазТехСтальПром”
5.2 Расчет выброса вредных веществ при стальном литье
6. Технико-экономическое обоснование проекта.
6.2 Выбор оборудования литейного цеха
По формуле (1) рассчитываем число плавильных агрегатов
6.2.2 Формовочное оборудование
6.2.4 Смесеприготовительное отделение
6.2.6 Капитальные вложения в оборудование цеха
6.2.7 Капитальные вложения в оснастку, производственный инструмент и инвентарь
6.2.8 Расчет капитальных вложений в производственное здание проектируемого цеха
6.3.1 ЕСТ и расчет средневзвешенного тарифного коэффициента для рабочих литейного цеха
6.3.2 Количество вспомогательных рабочих
6.3.3 Определение численности и состава служащих (организационная структура управления цехом)
6.4.1 Расчет фонда оплаты труда производственных рабочих
6.4.2 Расчет отчислений социального, индивидуального подоходного налога и пенсионные отчисления
6.4.3 Расчет фонда оплаты труда вспомогательных рабочих
6.4.4 Расчет отчислений социального, индивидуального подоходного налога и пенсионные отчисления
6.5 Расчет затрат на электроэнергию, расходуемую на нетехнологические цели
6.5.1 Затраты на электроэнергию, расходуемую на нетехнологические цели
К расходам электроэнергии на нетехнологические цели относится расходы энергии:
6.6 Расчет себестоимости производства литья
6.6.1 Калькуляция себестоимости жидкой стали
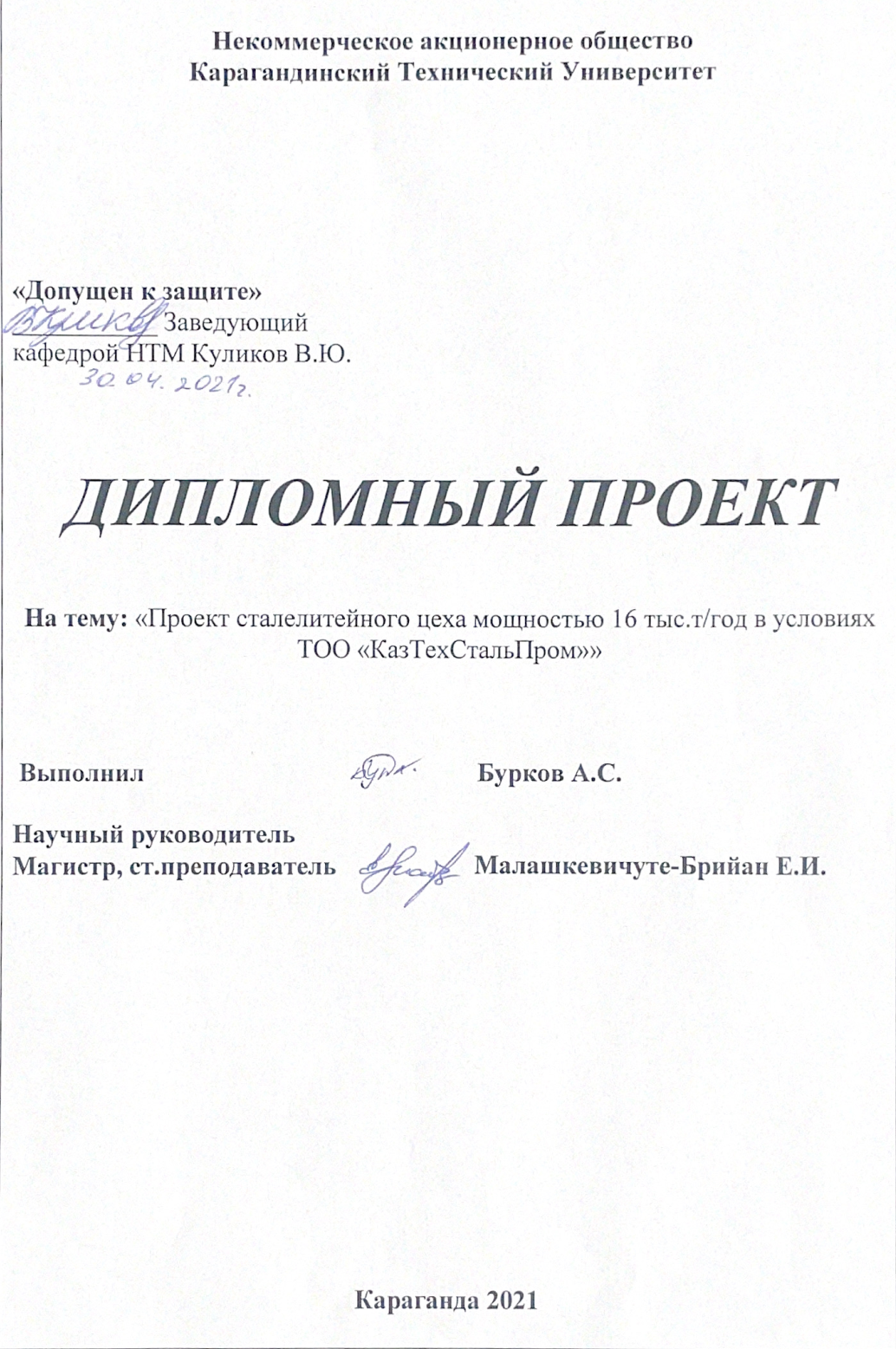
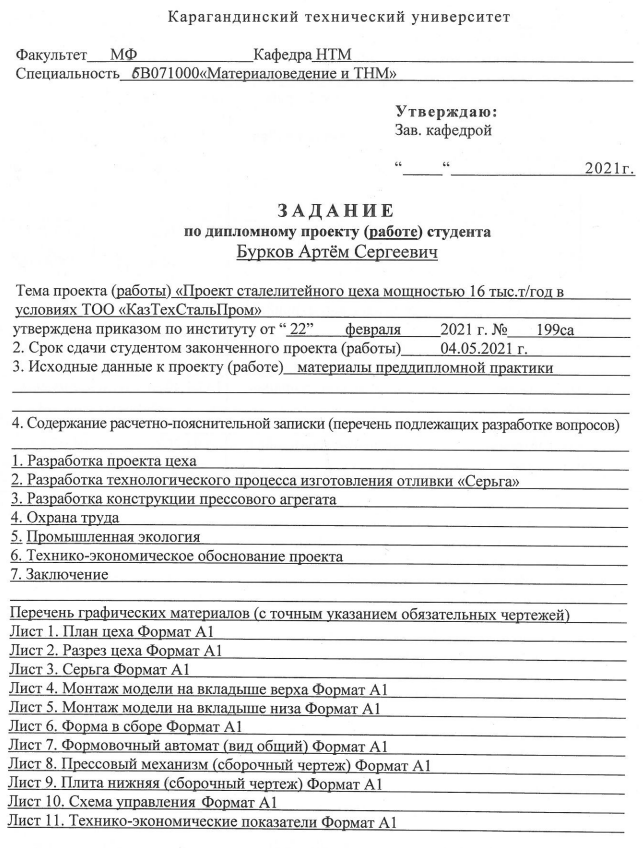


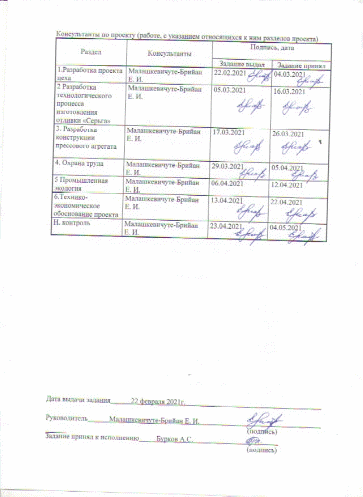

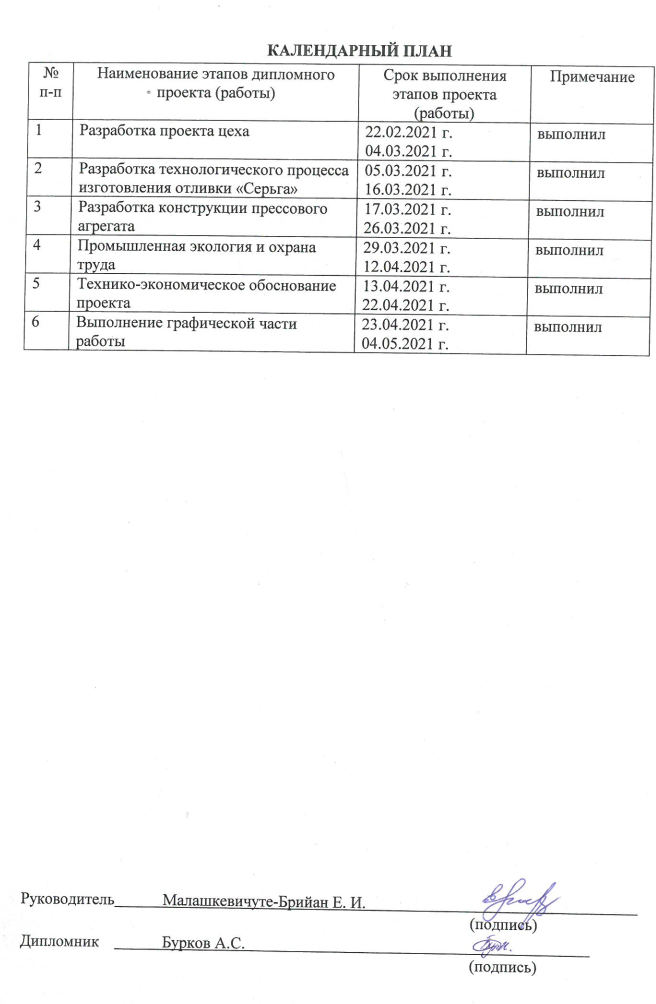
Аннотация
Целью данной выпускной работы является проектирование литейного цеха на базе уже имеющегося. Проекту необходимо было проанализировать помещение и оборудование базового цеха, и, используя полученные данные, привести пример своего собственного проекта.
В первой главе были проведены основные расчеты и обоснование общих решений. На основе полученных результатов выбрано необходимое оборудование, затем дано подробное описание по планировке проектируемого цеха, графическое исполнение которого представлено на первых двух листах дипломного проекта.
Вторая глава заключает в себе технологию изготовления отливки, которая входит в общую номенклатуру выпускаемой продукции. В данной главе дипломник показал знания, полученные при изучении дисциплины Технология литейного производства, произвел расчеты литниковой системы и дал обоснование при выборе формовочных материалов. Кроме раздела в пояснительной записке также были выполнены четыре обязательных листа по технологии.
В третью главу дипломного проекта входит специальная часть, целью которой является выбор и модернизация оборудования по заданным параметрам. Были произведены исследования и на их основе внесены изменения в выбранное устройство, чтобы оно отвечало всем требованиям задания. Последние четыре листа графической части дают представление о выбранном оборудовании и о его рассчитываемых узлах.
В четвертой главе выпускник проанализировал опасные и вредные производственные факторы литейного цеха, могущие повлиять на здоровье работающих в нем людей.
Промышленной экологии отводится пятая глава. Здесь был произведен анализ окружающей среды базового предприятия, перечислены возможные выбросы и отходы.
Технико-экономическое обоснование проекта является заключительной главой. В ней были произведены расчеты всех капитальных вложений и затрат, конечным результатом которых является заключение о его окупаемости.

Содержание

Введение 8
1 Разработка проекта цеха 9
1.1 Обоснование общих решений по проекту 9
1.2 Плавильное отделение 9
1.3 Формовочное отделение 16
1.4 Стержневое отделение 18
1.5 Смесеприготовительное отделение 22
2 Разработка технологического процесса изготовления отливки «Серьга». 26
2.1 Обоснование способа формовки 26
2.2 Обоснование положения детали в форме при заливке 27
2.3 Обоснование выбора поверхности разъема формы и модели 27
2.4 Обоснование величины усадки и припусков на механическую обработку, уклонов, галтелей 28
2.5 Определение конструкции и размеров знаков стержней 28
2.6 Литниковая система 29
2.6.1 Элементы литниковой системы и их назначение 29
2.6.2 Выбор типа литниковой системы 30
2.6.3 Расчет литниковой системы 30
2.7 Обоснование применяемой оснастки 32
2.8 Выбор формовочных и стержневых смесей 34
3. Разработка конструкции прессового агрегата 35
3.1 Общая компоновка прессовых формовочных машин 35
3.2 Прессовые механизмы 39
3.3 Общее описание рассчитываемого прессового агрегата по типу модели 5833Г 42
3.3.1 Устройство и работа 42
3.4 Расчет прессовой машины 44
3.4.1 Расчет рычажного механизма прессования 44
3.4.2 Расчет индикаторных диаграмм 47
3.4.3 Расчет станины 51
4. Охрана труда. 53
4.1 Анализ опасных и вредных производственных факторов литейного цеха 53
4.2 Мероприятия по снижению опасных и вредных производственных факторов 53
4.2.1 Расчет искусственного освещения 54
4.3 Меры пожарной безопасности цеха 55
5 Промышленная экология 57
5.1 Анализ состояния окружающей среды ТОО “КазТехСтальПром” 57
5.2 Расчет выброса вредных веществ при стальном литье 58
Ппыли = 8,74,20,80,282 = 16,37 кг/час 58
Ппыли = 16,373890 = 63679,3 ≈ 63,7 т/год 58
6. Технико-экономическое обоснование проекта. 59
6.1 Исходные данные для проектирования специализированного цеха стального литья мощностью 16 тыс. тонн в год 59
6.2 Выбор оборудования литейного цеха 59
6.2.1 Плавильное отделение 59
По формуле (1) рассчитываем число плавильных агрегатов 60
6.2.2 Формовочное оборудование 60
6.2.3 Стержневое отделение 60
6.2.4 Смесеприготовительное отделение 61
6.2.5 Термообрубное отделение 61
Модель 62
6.2.6 Капитальные вложения в оборудование цеха 63
6.2.7 Капитальные вложения в оснастку, производственный инструмент и инвентарь 64
6.2.8 Расчет капитальных вложений в производственное здание проектируемого цеха 64
6.3 Расчет численности производственных рабочих по рабочим местам на основании норм обслуживания по агрегатам 66
6.3.1 ЕСТ и расчет средневзвешенного тарифного коэффициента для рабочих литейного цеха 66
6.3.2 Количество вспомогательных рабочих 68
Нагревальщик ковшей 68
6.3.3 Определение численности и состава служащих (организационная структура управления цехом) 69
6.4 Расчет фонда оплаты труда 69
6.4.1 Расчет фонда оплаты труда производственных рабочих 69
6.4.2 Расчет отчислений социального, индивидуального подоходного налога и пенсионные отчисления 71
6.4.3 Расчет фонда оплаты труда вспомогательных рабочих 71
6.4.4 Расчет отчислений социального, индивидуального подоходного налога и пенсионные отчисления 72
Всего отчислений 72
В том числе 72
6.5 Расчет затрат на электроэнергию, расходуемую на нетехнологические цели 72
6.5.1 Затраты на электроэнергию, расходуемую на нетехнологические цели 72
К расходам электроэнергии на нетехнологические цели относится расходы энергии: 72
6.6 Расчет себестоимости производства литья 74
6.6.1 Калькуляция себестоимости жидкой стали 74
6.7 Расчет экономической эффективности капитальных вложений 74
Заключение 76
Список использованных источников 77
Приложение Б (Таблицы)
Приложение В (Спецификация)

Введение
Значение литейного производства для народного хозяйства и в первую очередь для машиностроения чрезвычайно велико. Литейное производство - основная заготовительная база, определяющая возможности дальнейшего развития отраслей машиностроения. Метод получения фасонных заготовок заливкой металла в формы до настоящего времени наиболее простой и доступный.
Отливки имеют существенные преимущества по сравнению с другими видами заготовок. Выбор вида заготовок для машиностроительных деталей в основном обуславливается различными техническими требованиями к их качеству.
При проектировании литейных цехов и заводов необходимо особое внимание уделять вопросам повышения качества отливок. В результате автоматизации обработки резанием повысились требования к геометрической точности литых заготовок. Оценкой конструкции машин по удельной массе на единицу мощности определилась тенденция получения тонкостенных отливок и уменьшения удельной массы литых деталей от общей массы оборудования.
С улучшением внешнего вида, а, следовательно, с повышением конкурентоспособности изделий повысились требования к качеству поверхности и внешнему виду отливок.
Появилась ориентация на использование в плавильных отделениях разнообразных шихтовых материалов. Распространяется применение предварительного подогрева шихты. Уменьшение содержания газов может быть обеспечено при выплавке стали в новых плавильных агрегатах, таких как индукционно-вакуумные печи.
Определилась тенденция по совершенствованию системы планирования и отчетности по литейному производству, направленная на увеличение изготовления отливок в штуках, а не в тоннах. Для уменьшения металлоемкости продукции наметилось расширение производства из ВЧ изложниц, труб, тюбингов и отливок в автомобилестроении. Будет увеличено изготовление отливок из алюминиевых сплавов.
Важнейшей современной проблемой литейного производства является автоматизация заливки форм. Данная задача уже решается как для чугунных, так и для стальных отливок, это позволит увеличить возможности использования формовочных автоматических линий. Расширяется применение мокрой уборки в смесеприготовительных и обрубочно-очистных отделениях, а также использование пылеуборочных вакуумных систем. Все отходы должны сепарироваться. Предусматривается грануляция шлаков для последующей сепарации. Повысились требования к условиям труда, по улучшению защиты окружающей атмосферы и прилегающих водных бассейнов.
1 Разработка проекта цеха
1.1 Обоснование общих решений по проекту
Согласно заданию, в случае ТОО «КазТехСтальПром» должен быть разработан проект завода по серийному производству стальных отливок мощностью 16 000 тонн в год.
ТОО «КазТехСтальПром» производит сталь и чугун промышленного назначения, а также декоративное литье в песчаных формах, слитки массой от 0,5 кг до 5 тонн, машинной и ручной формовки.
В связи с большим количеством литейных наименований в базовом цехе производственные мощности рассчитываются по программе, в которую входят пятнадцать представителей.
Производственное здание проектируемого цеха расположено в здании размером 72000х144000 м2 и высотой 10,5 м.
Основным видом деятельности компании является стальное литье.
Режим работы в две смены, в смену по 8 часов, 254 дня в году. Намеченная максимальная мощность - 16 000 тонн годного литья в год.
Технологический процесс производства состоит из этапов:
- прием, содержание и заготовка шихтовых материалов;
- формование и изготовление стержневых композиций;
- подготовка пресс-форм и стержней;
- выплавка стали;
- литье, охлаждение и разборка отливок;
- очистка отливок;
- термическая обработка отливок;
- исправление недостатков приемки и наполнения готовой продукции;
- утилизация отходов личного изготовления (возврат личного изготовления, браковка).
1.2 Плавильное отделение
В настоящее время в сталеплавильном производстве в области машиностроения используются следующие плавильные печи:
1. конвертеры с боковым дутьем с кислотным и основным покрытием;
2. Электродуговые печи с кислотным и основным покрытием;
3. Мартеновские печи с кислотным и основным покрытием;
4. индукционные и тигельные печи.
Сталь - это сплав железа с углеродом, содержание которого практически не превышает 1,7 ÷ 2%. Стали, содержащие обычные или стабильные сплавы называются углеродистыми сталями.
Стали с содержанием углерода до 0,25% называются низкоуглеродистыми или мягкими; содержит от 0,25 до 0,6% - среднего углерода, от 0,6 до 2% С - высокого углерода. Стали, содержащие большое количество таких примесей либо примесей таких как хром, никель, титан, молибден, называются легированными сталями. Если содержание легирующих компонентов в сталях (без углерода) не превышает 2,5%, они называются низколегированными. Содержание легирующих компонентов от 2,5 до 10,0%, то стали называют среднелегированными, более 10% - высоколегированными.
Жидкая сталь должна обладать следующими свойствами:
1. Достаточной жидкотекучестью, чтобы заполнить рабочую полость формы и дать ей хорошие следы;
2. химический состав в соответствии с требованиями ГОСТ или техническими условиями приемки слитков; должен содержать минимально вредные примеси (фосфор и сера) и растворенные газы (кислород, азот и водород).
3. Не должно содержать твердых и жидких неметаллических примесей. Металлические примеси должны легко и быстро всплывать на поверхность или удаляться с металла.
4. Обеспечить чистую поверхность слитков без захвата и обжига.
5. Структура литого металла должна быть плотной, сплошной разного типа и происхождения.
Чем выше нагрев металла, тем больше тепла выделяется из стали при кристаллизации и чем меньше тепла отводится от стенок каналов и полостей форм при ее заполнении, тем выше жидкотекучесть.
Определение массы расплавленного сплава в цехе является ключевым в структуре плавильного цеха. В основе расчета лежит цеховая программа, разделенная на отдельные (по весу) группы или технологические потоки литейного производства. В каждой группе или технологическом потоке слитки для отдельных классов загрузки разделяются в зависимости от требований к их физико-механическим свойствам. Эти данные включены в Таблицу 1.1 и являются основой для выбора метода плавки и типа плавильного завода. Информация о характере производства отливок, приведенные в цеховой программе сплавы и выбранный способ плавки позволяют определить процентное содержание и вес трещин, лома, отходов, безвозвратных потерь и, как следствие, общий вес жидкого сплава и металлической засыпки.
Одна и та же марка шихты используется для разных технологических процессов.
В таблицу 1.2 заполняют баланс металлозавалки.
По таблице 1.3 ведется расчет шихтовых материалов.
Для расчета используем метод подбора.
Таблица 1.1 Программа плавильного отделения
Введение
Значение литейного производства для народного хозяйства и в первую очередь для машиностроения чрезвычайно велико. Литейное производство - основная заготовительная база, определяющая возможности дальнейшего развития отраслей машиностроения. Метод получения фасонных заготовок заливкой металла в формы до настоящего времени наиболее простой и доступный.
Отливки имеют существенные преимущества по сравнению с другими видами заготовок. Выбор вида заготовок для машиностроительных деталей в основном обуславливается различными техническими требованиями к их качеству.
При проектировании литейных цехов и заводов необходимо особое внимание уделять вопросам повышения качества отливок. В результате автоматизации обработки резанием повысились требования к геометрической точности литых заготовок. Оценкой конструкции машин по удельной массе на единицу мощности определилась тенденция получения тонкостенных отливок и уменьшения удельной массы литых деталей от общей массы оборудования.
С улучшением внешнего вида, а, следовательно, с повышением конкурентоспособности изделий повысились требования к качеству поверхности и внешнему виду отливок.
Появилась ориентация на использование в плавильных отделениях разнообразных шихтовых материалов. Распространяется применение предварительного подогрева шихты. Уменьшение содержания газов может быть обеспечено при выплавке стали в новых плавильных агрегатах, таких как индукционно-вакуумные печи.
Определилась тенденция по совершенствованию системы планирования и отчетности по литейному производству, направленная на увеличение изготовления отливок в штуках, а не в тоннах. Для уменьшения металлоемкости продукции наметилось расширение производства из ВЧ изложниц, труб, тюбингов и отливок в автомобилестроении. Будет увеличено изготовление отливок из алюминиевых сплавов.
Важнейшей современной проблемой литейного производства является автоматизация заливки форм. Данная задача уже решается как для чугунных, так и для стальных отливок, это позволит увеличить возможности использования формовочных автоматических линий. Расширяется применение мокрой уборки в смесеприготовительных и обрубочно-очистных отделениях, а также использование пылеуборочных вакуумных систем. Все отходы должны сепарироваться. Предусматривается грануляция шлаков для последующей сепарации. Повысились требования к условиям труда, по улучшению защиты окружающей атмосферы и прилегающих водных бассейнов.
1 Разработка проекта цеха
1.1 Обоснование общих решений по проекту
Согласно заданию, в случае ТОО «КазТехСтальПром» должен быть разработан проект завода по серийному производству стальных отливок мощностью 16 000 тонн в год.
ТОО «КазТехСтальПром» производит сталь и чугун промышленного назначения, а также декоративное литье в песчаных формах, слитки массой от 0,5 кг до 5 тонн, машинной и ручной формовки.
В связи с большим количеством литейных наименований в базовом цехе производственные мощности рассчитываются по программе, в которую входят пятнадцать представителей.
Производственное здание проектируемого цеха расположено в здании размером 72000х144000 м2 и высотой 10,5 м.
Основным видом деятельности компании является стальное литье.
Режим работы в две смены, в смену по 8 часов, 254 дня в году. Намеченная максимальная мощность - 16 000 тонн годного литья в год.
Технологический процесс производства состоит из этапов:
- прием, содержание и заготовка шихтовых материалов;
- формование и изготовление стержневых композиций;
- подготовка пресс-форм и стержней;
- выплавка стали;
- литье, охлаждение и разборка отливок;
- очистка отливок;
- термическая обработка отливок;
- исправление недостатков приемки и наполнения готовой продукции;
- утилизация отходов личного изготовления (возврат личного изготовления, браковка).
1.2 Плавильное отделение
В настоящее время в сталеплавильном производстве в области машиностроения используются следующие плавильные печи:
1. конвертеры с боковым дутьем с кислотным и основным покрытием;
2. Электродуговые печи с кислотным и основным покрытием;
3. Мартеновские печи с кислотным и основным покрытием;
4. индукционные и тигельные печи.
Сталь - это сплав железа с углеродом, содержание которого практически не превышает 1,7 ÷ 2%. Стали, содержащие обычные или стабильные сплавы называются углеродистыми сталями.
Стали с содержанием углерода до 0,25% называются низкоуглеродистыми или мягкими; содержит от 0,25 до 0,6% - среднего углерода, от 0,6 до 2% С - высокого углерода. Стали, содержащие большое количество таких примесей либо примесей таких как хром, никель, титан, молибден, называются легированными сталями. Если содержание легирующих компонентов в сталях (без углерода) не превышает 2,5%, они называются низколегированными. Содержание легирующих компонентов от 2,5 до 10,0%, то стали называют среднелегированными, более 10% - высоколегированными.
Жидкая сталь должна обладать следующими свойствами:
1. Достаточной жидкотекучестью, чтобы заполнить рабочую полость формы и дать ей хорошие следы;
2. химический состав в соответствии с требованиями ГОСТ или техническими условиями приемки слитков; должен содержать минимально вредные примеси (фосфор и сера) и растворенные газы (кислород, азот и водород).
3. Не должно содержать твердых и жидких неметаллических примесей. Металлические примеси должны легко и быстро всплывать на поверхность или удаляться с металла.
4. Обеспечить чистую поверхность слитков без захвата и обжига.
5. Структура литого металла должна быть плотной, сплошной разного типа и происхождения.
Чем выше нагрев металла, тем больше тепла выделяется из стали при кристаллизации и чем меньше тепла отводится от стенок каналов и полостей форм при ее заполнении, тем выше жидкотекучесть.
Определение массы расплавленного сплава в цехе является ключевым в структуре плавильного цеха. В основе расчета лежит цеховая программа, разделенная на отдельные (по весу) группы или технологические потоки литейного производства. В каждой группе или технологическом потоке слитки для отдельных классов загрузки разделяются в зависимости от требований к их физико-механическим свойствам. Эти данные включены в Таблицу 1.1 и являются основой для выбора метода плавки и типа плавильного завода. Информация о характере производства отливок, приведенные в цеховой программе сплавы и выбранный способ плавки позволяют определить процентное содержание и вес трещин, лома, отходов, безвозвратных потерь и, как следствие, общий вес жидкого сплава и металлической засыпки.
Одна и та же марка шихты используется для разных технологических процессов.
В таблицу 1.2 заполняют баланс металлозавалки.
По таблице 1.3 ведется расчет шихтовых материалов.
Для расчета используем метод подбора.
Таблица 1.1 Программа плавильного отделения
Введение
Значение литейного производства для народного хозяйства и в первую очередь для машиностроения чрезвычайно велико. Литейное производство - основная заготовительная база, определяющая возможности дальнейшего развития отраслей машиностроения. Метод получения фасонных заготовок заливкой металла в формы до настоящего времени наиболее простой и доступный.
Отливки имеют существенные преимущества по сравнению с другими видами заготовок. Выбор вида заготовок для машиностроительных деталей в основном обуславливается различными техническими требованиями к их качеству.
При проектировании литейных цехов и заводов необходимо особое внимание уделять вопросам повышения качества отливок. В результате автоматизации обработки резанием повысились требования к геометрической точности литых заготовок. Оценкой конструкции машин по удельной массе на единицу мощности определилась тенденция получения тонкостенных отливок и уменьшения удельной массы литых деталей от общей массы оборудования.
С улучшением внешнего вида, а, следовательно, с повышением конкурентоспособности изделий повысились требования к качеству поверхности и внешнему виду отливок.
Появилась ориентация на использование в плавильных отделениях разнообразных шихтовых материалов. Распространяется применение предварительного подогрева шихты. Уменьшение содержания газов может быть обеспечено при выплавке стали в новых плавильных агрегатах, таких как индукционно-вакуумные печи.
Определилась тенденция по совершенствованию системы планирования и отчетности по литейному производству, направленная на увеличение изготовления отливок в штуках, а не в тоннах. Для уменьшения металлоемкости продукции наметилось расширение производства из ВЧ изложниц, труб, тюбингов и отливок в автомобилестроении. Будет увеличено изготовление отливок из алюминиевых сплавов.
Важнейшей современной проблемой литейного производства является автоматизация заливки форм. Данная задача уже решается как для чугунных, так и для стальных отливок, это позволит увеличить возможности использования формовочных автоматических линий. Расширяется применение мокрой уборки в смесеприготовительных и обрубочно-очистных отделениях, а также использование пылеуборочных вакуумных систем. Все отходы должны сепарироваться. Предусматривается грануляция шлаков для последующей сепарации. Повысились требования к условиям труда, по улучшению защиты окружающей атмосферы и прилегающих водных бассейнов.
1 Разработка проекта цеха
1.1 Обоснование общих решений по проекту
Согласно заданию, в случае ТОО «КазТехСтальПром» должен быть разработан проект завода по серийному производству стальных отливок мощностью 16 000 тонн в год.
ТОО «КазТехСтальПром» производит сталь и чугун промышленного назначения, а также декоративное литье в песчаных формах, слитки массой от 0,5 кг до 5 тонн, машинной и ручной формовки.
В связи с большим количеством литейных наименований в базовом цехе производственные мощности рассчитываются по программе, в которую входят пятнадцать представителей.
Производственное здание проектируемого цеха расположено в здании размером 72000х144000 м2 и высотой 10,5 м.
Основным видом деятельности компании является стальное литье.
Режим работы в две смены, в смену по 8 часов, 254 дня в году. Намеченная максимальная мощность - 16 000 тонн годного литья в год.
Технологический процесс производства состоит из этапов:
- прием, содержание и заготовка шихтовых материалов;
- формование и изготовление стержневых композиций;
- подготовка пресс-форм и стержней;
- выплавка стали;
- литье, охлаждение и разборка отливок;
- очистка отливок;
- термическая обработка отливок;
- исправление недостатков приемки и наполнения готовой продукции;
- утилизация отходов личного изготовления (возврат личного изготовления, браковка).
1.2 Плавильное отделение
В настоящее время в сталеплавильном производстве в области машиностроения используются следующие плавильные печи:
1. конвертеры с боковым дутьем с кислотным и основным покрытием;
2. Электродуговые печи с кислотным и основным покрытием;
3. Мартеновские печи с кислотным и основным покрытием;
4. индукционные и тигельные печи.
Сталь - это сплав железа с углеродом, содержание которого практически не превышает 1,7 ÷ 2%. Стали, содержащие обычные или стабильные сплавы называются углеродистыми сталями.
Стали с содержанием углерода до 0,25% называются низкоуглеродистыми или мягкими; содержит от 0,25 до 0,6% - среднего углерода, от 0,6 до 2% С - высокого углерода. Стали, содержащие большое количество таких примесей либо примесей таких как хром, никель, титан, молибден, называются легированными сталями. Если содержание легирующих компонентов в сталях (без углерода) не превышает 2,5%, они называются низколегированными. Содержание легирующих компонентов от 2,5 до 10,0%, то стали называют среднелегированными, более 10% - высоколегированными.
Жидкая сталь должна обладать следующими свойствами:
1. Достаточной жидкотекучестью, чтобы заполнить рабочую полость формы и дать ей хорошие следы;
2. химический состав в соответствии с требованиями ГОСТ или техническими условиями приемки слитков; должен содержать минимально вредные примеси (фосфор и сера) и растворенные газы (кислород, азот и водород).
3. Не должно содержать твердых и жидких неметаллических примесей. Металлические примеси должны легко и быстро всплывать на поверхность или удаляться с металла.
4. Обеспечить чистую поверхность слитков без захвата и обжига.
5. Структура литого металла должна быть плотной, сплошной разного типа и происхождения.
Чем выше нагрев металла, тем больше тепла выделяется из стали при кристаллизации и чем меньше тепла отводится от стенок каналов и полостей форм при ее заполнении, тем выше жидкотекучесть.
Определение массы расплавленного сплава в цехе является ключевым в структуре плавильного цеха. В основе расчета лежит цеховая программа, разделенная на отдельные (по весу) группы или технологические потоки литейного производства. В каждой группе или технологическом потоке слитки для отдельных классов загрузки разделяются в зависимости от требований к их физико-механическим свойствам. Эти данные включены в Таблицу 1.1 и являются основой для выбора метода плавки и типа плавильного завода. Информация о характере производства отливок, приведенные в цеховой программе сплавы и выбранный способ плавки позволяют определить процентное содержание и вес трещин, лома, отходов, безвозвратных потерь и, как следствие, общий вес жидкого сплава и металлической засыпки.
Одна и та же марка шихты используется для разных технологических процессов.
В таблицу 1.2 заполняют баланс металлозавалки.
По таблице 1.3 ведется расчет шихтовых материалов.
Для расчета используем метод подбора.
Таблица 1.1 Программа плавильного отделения
Наименование отливки | Марка сплава | Масса отливки | Кол-во годных отливок на годовую программу | Брак отливок | Годовое кол-во отливок с учетом брака | Масса литников (25%) | Итого жидкого металла | |||||||||
| | кг | т | шт. | % | шт. | т | шт. | т | на 1 отливку | на годовое кол-во | на 1 отливку, кг | на годовую программу | |||
Опора | 35Л | 110 | 1100 | 10000 | 5 | 500 | 55 | 10500 | 1155 | 27,5 | 288,75 | 137,5 | 1443,75 | |||
Проушина | 35Л | 13,5 | 675 | 50000 | 5 | 2500 | 33,8 | 52500 | 708,75 | 3,375 | 177,2 | 16,875 | 885,95 | |||
Серьга | 35Л | 30,2 | 755 | 25000 | 5 | 1250 | 37,7 | 26250 | 792,75 | 7,55 | 198,2 | 37,75 | 990,95 | |||
Опора | 35Л | 30 | 1000 | 33333 | 5 | 1665 | 50 | 34998 | 1049,95 | 7,5 | 262,5 | 37,5 | 1312,45 | |||
Опора | 35Л | 60 | 600 | 10000 | 5 | 500 | 30 | 10500 | 630 | 15 | 157,5 | 75 | 787,5 | |||
Траверса | 35Л | 90 | 900 | 10000 | 5 | 500 | 45 | 10500 | 945 | 22,5 | 236,25 | 112,5 | 1181,25 | |||
Шпунт | 35Л | 95 | 2470 | 26000 | 5 | 1300 | 124 | 27300 | 2593,5 | 23,75 | 648,4 | 118,75 | 3241,9 | |||
Опора | 35Л | 110 | 1100 | 10000 | 5 | 500 | 55 | 10500 | 1155 | 27,5 | 288,8 | 137,5 | 1443,8 | |||
Блок | 35Л | 120 | 1200 | 10000 | 5 | 500 | 60 | 10500 | 1260 | 30 | 315 | 150 | 1575 | |||
Траверса | 35Л | 80 | 800 | 10000 | 5 | 500 | 40 | 10500 | 840 | 20 | 210 | 100 | 1050 | |||
Траверса | 35Л | 150 | 600 | 4000 | 5 | 200 | 30 | 4200 | 630 | 37,5 | 156,5 | 187,5 | 787,5 | |||
Шпунт | 35Л | 90 | 1800 | 20000 | 5 | 1000 | 90 | 21000 | 1890 | 22,5 | 473 | 112,5 | 2362,5 | |||
Проушина | 35Л | 115 | 1150 | 10000 | 5 | 500 | 57,5 | 10500 | 1207,5 | 28,75 | 302 | 143,75 | 1509,5 | |||
Серьга | 35Л | 95 | 950 | 10000 | 5 | 500 | 47,5 | 10500 | 997,5 | 23,75 | 249 | 118,75 | 1246,5 | |||
Опора | 35Л | 90 | 900 | 10000 | 5 | 500 | 45 | 10500 | 945 | 22,5 | 236 | 112,5 | 1181 | |||
Итого | | 1279 | 16000 | 174333 | | | 800 | | 16800 | | 4200 | | 21000 |
Таблица 1.2 Баланс металлозавалки
Годное литье | Брак | Литники и прибыли | Сливы | Жидкий металл | Угар и безвозвратные потери | Металлозавалка | |||||||||||||
m | % | m | % | m | % | m | % | M | % | M | % | m | % | ||||||
16000 | 72 | 800 | 5 | 4000 | 25 | 320 | 2 | 21120 | 95 | 1056 | 5 | 22232 | 100 |
Для расчета требуется определить процент возврата (брак, литники, сливы), (из таблицы 1.2)

Химический состав ст.35Л | Средний |
С = 0,320,40 | 0,36 |
Mn = 0,400,90 | 0,65 |
Si = 0,200,52 | 0,36 |
P не более 0,5 | 0,045 |
S не более 0,05 | 0,04 |
Принимаем, что возврат (30%) химический состав которых соответствует среднему содержанию элементов в стали 35Л.
Таблица 1.3 Используемые материалы (химсостав материалов металлошихты)
Наименование | C | Mn | S | По расчету |
возврат | 0,36 | 0,65 | 0,36 | 30% |
Лом стальной | 0,32 | 0,45 | 0,25 | 68,15 |
Чугун передельный ПЛ-2 | 4,0 | 1,0 | 0,8 | 1,85 |
Ферромарганец ФМП-75 | 7,0 | 75,0 | 1,0 | Сверх 100% |
Ферросилиций ФС-45 | 0,15 | 0,6 | 45,0 | Сверх 100% |