Файл: Целью данной выпускной работы является проектирование литейного цеха на базе уже имеющегося.docx
ВУЗ: Не указан
Категория: Не указан
Дисциплина: Не указана
Добавлен: 11.01.2024
Просмотров: 333
Скачиваний: 1
СОДЕРЖАНИЕ
1.5 Смесеприготовительное отделение
2 Разработка технологического процесса изготовления отливки «Серьга».
2.1 Обоснование способа формовки
2.2 Обоснование положения детали в форме при заливке
2.3 Обоснование выбора поверхности разъема формы и модели
2.4 Обоснование величины усадки и припусков на механическую обработку, уклонов, галтелей
2.5 Определение конструкции и размеров знаков стержней
2.6.1 Элементы литниковой системы и их назначение
2.6.2 Выбор типа литниковой системы
2.7 Обоснование применяемой оснастки
2.8 Выбор формовочных и стержневых смесей
3. Разработка конструкции прессового агрегата
3.1 Общая компоновка прессовых формовочных машин
3.3 Общее описание рассчитываемого прессового агрегата по типу модели 5833Г
3.4.1 Расчет рычажного механизма прессования
3.4.2 Расчет индикаторных диаграмм
4.1 Анализ опасных и вредных производственных факторов литейного цеха
4.2 Мероприятия по снижению опасных и вредных производственных факторов
4.3 Меры пожарной безопасности цеха
5.1 Анализ состояния окружающей среды ТОО “КазТехСтальПром”
5.2 Расчет выброса вредных веществ при стальном литье
6. Технико-экономическое обоснование проекта.
6.2 Выбор оборудования литейного цеха
По формуле (1) рассчитываем число плавильных агрегатов
6.2.2 Формовочное оборудование
6.2.4 Смесеприготовительное отделение
6.2.6 Капитальные вложения в оборудование цеха
6.2.7 Капитальные вложения в оснастку, производственный инструмент и инвентарь
6.2.8 Расчет капитальных вложений в производственное здание проектируемого цеха
6.3.1 ЕСТ и расчет средневзвешенного тарифного коэффициента для рабочих литейного цеха
6.3.2 Количество вспомогательных рабочих
6.3.3 Определение численности и состава служащих (организационная структура управления цехом)
6.4.1 Расчет фонда оплаты труда производственных рабочих
6.4.2 Расчет отчислений социального, индивидуального подоходного налога и пенсионные отчисления
6.4.3 Расчет фонда оплаты труда вспомогательных рабочих
6.4.4 Расчет отчислений социального, индивидуального подоходного налога и пенсионные отчисления
6.5 Расчет затрат на электроэнергию, расходуемую на нетехнологические цели
6.5.1 Затраты на электроэнергию, расходуемую на нетехнологические цели
К расходам электроэнергии на нетехнологические цели относится расходы энергии:
6.6 Расчет себестоимости производства литья
6.6.1 Калькуляция себестоимости жидкой стали
Pпн δх3 = Pпр δх5; (3.2) [6]
Здесь Pпн – усилие пневмоцилиндра;
Pпр - усилие, развиваемое прессовой плитой.
δх3, δх5– возможные перемещения звеньев 3 и 5.
Из этой формулы определяем:
ŋ0 =

Проектируя звенья 1-2-3 и 1-2-4-5 на направление продольной вертикальной оси машины, (будем индексами «в» и «г» наверху обозначать проекции длины рычага li,j на вертикальное lвi,jи соответственно горизонтальное lгi,jнаправления, где i, j – номера шарниров, связываемых рычагом li,j), получим:
lв13 = l12cosβ - l23cosα; (3.4)
lв15 = l12cosβ + l24cos(α+φ) + l45cosγ; (3.5)
здесь углы α,β,γ изменяются в зависимости от положения звеньев механизма, угол φ – постоянный, его выбирают конструктивно.
Возможные перемещения ведущего звена δх3 и ведомого δх5 получим, дифференцируя выражения (3.4) и (3.5):
δх3 = d(lв13) = - l12sinβdβ + l23sinαdα. (3.6)
δх5 = d(lв15) = - l12sinβdβ - l24sin(α+φ)dα – l45sinγdγ; (3.7)
здесь dα,dβ,dγ – приращения углов α,β,γ, соответствующие возможным перемещениям δх3 ,δх5.
Для того чтобы найти связь между углами dβиdγи углом dα, спроектируем звенья 1-2-3 и 1-2-4-5 на направление по поперечной горизонтальной оси машины. Получим
lг13 = l12sinβ + l23sinα; (3.8)
lв15 = l12sinβ + l24sin(α+φ) - l45sinγ; (3.9)
Дифференцируя выражения (3.8) и (3.9), получим
d( lг13) = l12cosβdβ + l23cosαdα; (3.10)
d( lг15) =
l12cosβdβ + l24cos(α+φ)dα - l45cosγdγ. (3.11)
Так как при работе механизма расстояния lг13 и lг15 не изменяются, то
d( lг13) = 0; d( lг15) = 0. (3.12)
Из формул (3.10) и (3.11) находим
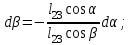
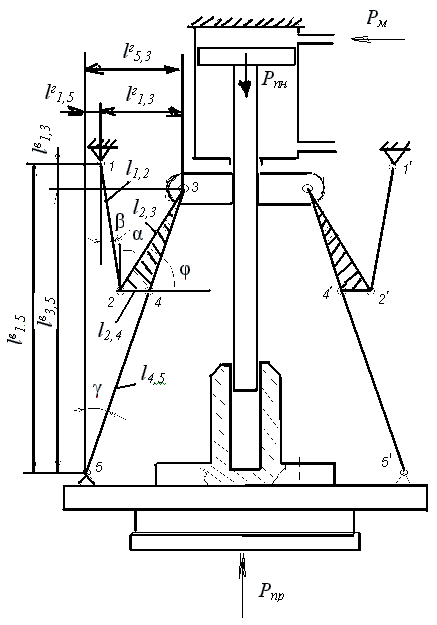
На рис. 3.10 Расчетная схема коленно-рычажного механизма с эксцентриком, связанным со звеном 2-3

Знак минус в формулах (3.13) и (3.14) указывает на то, что когда при опускании поршня пневмоцилиндра угол α увеличивается, углы β и γ уменьшаются.
Подставляя выражения (3.11) и (3.14) в формулы (3.6) и (3.7), получим
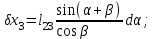

Подставляем (3.15) и (3.16) в (3.3) и получаем окончательную формулу коэффициента усиления рассматриваемого коленно-рычажного механизма в виде
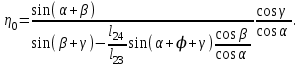
В полученной формуле углы α,β,γ изменяются в зависимости от положения звеньев; угол φ – величина постоянная, численное значение ее выбирают конструктивно.
Таким образом по заданной величине усилия прессования можем определить необходимое усилие силового пневмоцилиндра Pпн.Для этого подставляем в формулу (3.17) значения углов в конце хода прессования (рычаги находятся в крайнем положении):


Знак минус можно не учитывать. Имеем коэффициент усиления равный ≈1:20. Значение очень велико в сравнении с паспортными данными для этой машины. Отношение ŋ0 к ŋ составляет 2:1. Как видим, нельзя недооценивать значения сил трения в шарнирах! Поэтому далее будем вести расчет для коэффициента усиления в 1:10.
Из формулы (3.3) находим требуемое значение усилия силового пневмоцилиндра:
Pпн = Pпр ŋ = 30·0.1 = 3 кН
Как известно из паспортных данных диаметр поршня в машине модели 5833Г составляет 750 мм. При этом значение усилия силового пневмоцилиндра составляет 4 кН. Так как все расчеты ведутся приблизительно, мы из этих данных составим соотношение и найдем диаметр поршня в нашей расчетной машине:

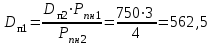
Из ряда нормальных значений диаметр поршня будет равен 600 мм.
3.4.2 Расчет индикаторных диаграмм
Рассмотрим рабочий процесс пневматического прессового цилиндра формовочной машины по индикаторной диаграмме. В нашей машине механизм прессования располагается над модельным комплектом. Опока и наполнительная рамка неподвижны. Перед началом прессования между прессовой колодкой и верхней кромкой наполнительной рамки имеется зазор Z см. При построении индикаторной диаграммы ход поршня S в м будем откладывать по ординате, а абсолютное давление в цилиндре P в Па – по абсциссе.
Начальные данные:
Dп = 600 мм
Размеры опоки 800х1000х250 мм
ρ0= 1г/см3
Зазор Z примем равным 0,01 м.
Точка 1 начала хода будет иметь следующие координаты:
1) ординату, равную приведенной высоте вредного пространства прессового цилиндра, м:
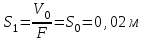
где V0 - объем вредного пространства, м3; F– площадь поршня, м2.
Fоп = 800*1000 = 0,8 м2 – площадь опоки
Fп = πR2 = 3,14*0,32 = 0,28 м2 – площадь поршня
Величина ρmaxформовочной смеси соответствует такому состоянию ее уплотнения, при котором вся глина и вода выдавлены в межзерновые поры песчаной основы, а эта последняя достигла своей максимально плотной упаковки зерен. Величину ρmax формовочной смеси можно легко рассчитать аналитически, если известны состав смеси и величина ρmax ее песчаной основы.
Пусть, например, смесь состоит из 90% песка, 7% глины и 3% воды и ρmax ее песчаной основы равна 1,60 г/см3. Тогда, очевидно, в 1 г смеси будет содержаться 0,90 г песчаной основы, которая при состоянии максимального уплотнения смеси (и одновременно максимального уплотнения песчаной основы) будет занимать объем, равный 0,90/1,60 см3. При этом остальные составные части смеси (0,07 г глины и 0,03 г воды) будут выдавлены в межзерновые поры и, следовательно, будут располагаться в том же объеме, занимаемом песчаной основой смеси. Таким образом, искомая предельная плотность смеси ρmax составит:

На практике состояние уплотнения формовочных смесей, соответствующее значениям их
ρmax, обычно не достигается или достигается редко. Поэтому ρmax= 1,6

На участке хода 1-2, на протяжении которого выбирается зазор Z между прессовой колодкой и поверхностью формовочной смеси в наполнительной рамке, давление под поршнем не изменяется.
Если начальная плотность смеси в опоке была ρ0 = 1

ρ=1+Сp0,25 (уравнение Н.П. Аксенова) (3.19) [7]
сопротивление формы уплотнению в начальный момент прессования ρ0=0. Линия прессования индикаторной диаграммы покажет плавное нарастание давления от точки 2.

Вес поднимаемых частей складывается в нашем случае из веса подвижной плиты, колодки и рычажного механизма. Прикинув в уме, примем вес G = 500 кг, что является равным 5·103 Н.
Сила трения равна
Fтр = 0,25G = 0,25·5·103 = 1,25·103 Н
Давление в точке 1

Примечание: в данной формуле учитываем коэффициент усиления рычажного механизма равный как помним 1:10.
Давление в точке 2


P0 =
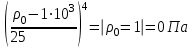


Высоту рамки находим по формуле
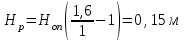
При построении индикаторной диаграммы промежуточные точки на участке прессования легко могут быть найдены аналитически.
Весь процесс уплотнения проходит по высоте наполнительной рамки. Тогда
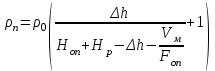
Где Vм – объем модели
Vм = 0,4 Vоп = 0,4*0,8*1*0,25 = 0,08 м3
Делим Hр на 4 равные части (0,0375; 0,075; 0,1125; 0,15) и находим промежуточные точки на рабочем участке диаграммы для ее построения