Файл: Целью данной выпускной работы является проектирование литейного цеха на базе уже имеющегося.docx
ВУЗ: Не указан
Категория: Не указан
Дисциплина: Не указана
Добавлен: 11.01.2024
Просмотров: 334
Скачиваний: 1
СОДЕРЖАНИЕ
1.5 Смесеприготовительное отделение
2 Разработка технологического процесса изготовления отливки «Серьга».
2.1 Обоснование способа формовки
2.2 Обоснование положения детали в форме при заливке
2.3 Обоснование выбора поверхности разъема формы и модели
2.4 Обоснование величины усадки и припусков на механическую обработку, уклонов, галтелей
2.5 Определение конструкции и размеров знаков стержней
2.6.1 Элементы литниковой системы и их назначение
2.6.2 Выбор типа литниковой системы
2.7 Обоснование применяемой оснастки
2.8 Выбор формовочных и стержневых смесей
3. Разработка конструкции прессового агрегата
3.1 Общая компоновка прессовых формовочных машин
3.3 Общее описание рассчитываемого прессового агрегата по типу модели 5833Г
3.4.1 Расчет рычажного механизма прессования
3.4.2 Расчет индикаторных диаграмм
4.1 Анализ опасных и вредных производственных факторов литейного цеха
4.2 Мероприятия по снижению опасных и вредных производственных факторов
4.3 Меры пожарной безопасности цеха
5.1 Анализ состояния окружающей среды ТОО “КазТехСтальПром”
5.2 Расчет выброса вредных веществ при стальном литье
6. Технико-экономическое обоснование проекта.
6.2 Выбор оборудования литейного цеха
По формуле (1) рассчитываем число плавильных агрегатов
6.2.2 Формовочное оборудование
6.2.4 Смесеприготовительное отделение
6.2.6 Капитальные вложения в оборудование цеха
6.2.7 Капитальные вложения в оснастку, производственный инструмент и инвентарь
6.2.8 Расчет капитальных вложений в производственное здание проектируемого цеха
6.3.1 ЕСТ и расчет средневзвешенного тарифного коэффициента для рабочих литейного цеха
6.3.2 Количество вспомогательных рабочих
6.3.3 Определение численности и состава служащих (организационная структура управления цехом)
6.4.1 Расчет фонда оплаты труда производственных рабочих
6.4.2 Расчет отчислений социального, индивидуального подоходного налога и пенсионные отчисления
6.4.3 Расчет фонда оплаты труда вспомогательных рабочих
6.4.4 Расчет отчислений социального, индивидуального подоходного налога и пенсионные отчисления
6.5 Расчет затрат на электроэнергию, расходуемую на нетехнологические цели
6.5.1 Затраты на электроэнергию, расходуемую на нетехнологические цели
К расходам электроэнергии на нетехнологические цели относится расходы энергии:
6.6 Расчет себестоимости производства литья
6.6.1 Калькуляция себестоимости жидкой стали
Продолжение таблицы 1.13
Траверса | 4284 | | 15 | 64 | | 66 |
Шпунт | 42840 | 9 | 386 | 397 | ||
Проушина | 10710 | 11,5 | 123 | 127 | ||
Серьга | 10710 | | 9,5 | 102 | | 105 |
Опора | 10710 | 9 | 96 | 99 | ||
Итого: | | | | | | 2372 |
Расчет количества оборудования смесеприготовительного отделения представлен формулой 1.4:

где Qсм – необходимое количество смеси, м3;
q – производительность оборудования, т/ч;
Fg – действительный фонд времени работы оборудования, ч.
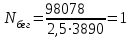
Судя по расчетам нам будет достаточно поставить одни бегуны, но, учитывая их важность в цехе, необходимо ставить еще одни на случай внезапной поломки и др.
Установим два бегуна модели 15104 для приготовления формовочной и стержневой смесей.
2 Разработка технологического процесса изготовления отливки «Серьга».
2.1 Обоснование способа формовки
Формование - это процесс создания одноразовых литейных форм. Это сложный и ответственный этап всего технологического цикла литья, который во многом определяет их качество. Процесс формирования выглядит следующим образом:
- уплотнение смеси, что позволяет получить точный след модели по форме и придать ей необходимую прочность в сочетании с податливостью, газопроницаемостью и другими свойствами;
- устройство в виде вентиляционных каналов, облегчающих отвод газов, образующихся при заливке, из полости формы;
- извлечение модели из формы;
- стандартная обработка и сборка, включая установку стержней.
В зависимости от размера, веса и толщины стенки отливки, а также типа сплава отливки его разливают в сырые, сухие и химически твердеющие формы. Формы изготавливаются вручную, на формовочных машинах, полуавтоматических и автоматических линиях.
Так как эта отливка весит 30,2 кг, отливка заливается по-сырому. Заливка по-сырому является более технологичной, так как отпадает необходимость в сушке форм, что значительно ускоряет технологический процесс.
В случае серийного производства его можно формировать как вручную, так и машинным способом. Для изготовления этой отливки мы используем машинную формовку. Машинное формование позволяет механизировать две основные операции формования (уплотнение смеси, удаление модели из формы) и некоторые вспомогательные операции (устройство литниковых каналов, вращение опок и т.д.). Механизация процесса формовки улучшает качество уплотнения, увеличивает точность размеров отливок, резко увеличивает производительность труда, упрощает работу рабочего, улучшает санитарно-гигиенические условия в цеху, снижает брак.
В качестве формовочной машины мы используем машину прессового типа. В такой машине уплотнение смеси происходит за счет давления прессовой колодки. Сжатый воздух (6/10)*106 Па поступает в пневмоцилиндр, шток поршня которого соединен с рычажной системой Эйлера. Они, в свою очередь, подключаются к прессу и опускают его при движении.
При использовании обычных песчано-глинистых смесей твердость поверхности формы достигает 89-94 единицы. Максимальному уплотнению смеси соответствует разъему полуформы. Улучшение технологических параметров литейной формы повышает геометрическую точность отливок, снижает брак, улучшает санитарно-гигиенические условия труда за счет полного устранения вибрации и шума.
2.2 Обоснование положения детали в форме при заливке
Основная задача выбора положения отливки при отливке - получение важнейших поверхностей без дефектов отливки. При выборе стандартного положения для отливки руководствуемся следующими рекомендациями:
- учитываем принцип затвердевания отливки: укладываем отливку по разъему формы;
- основные обрабатываемые поверхности и важнейшие детали отливки расположены вертикально;
- такое положение обеспечивает надежную фиксацию стержней в кристаллизаторе при отливке, толщину стенок отливки можно контролировать при сборке формы;
2.3 Обоснование выбора поверхности разъема формы и модели
Поверхность контакта верхней и нижней полуформы называется поверхностью разъема формы. Она необходима для извлечения модели из уплотненной формовочной смеси и установки стержней в форму. Поверхность разъема может быть плоской и фасонной.
Выбор формы разъема зависит от конструкции модели и разъемы модели, необходимости использования стержней, размера формовочных уклонов, размера опок и т.д. Если поверхность соединителя выбрана неправильно, отливка может деформироваться, а формовка и сборка могут быть неоправданно сложными.
Выбранная поверхность разъема формы соответствует следующим требованиям:
- поверхность формы и детали модели гладкая, что наиболее рационально с точки зрения создания набора моделей;
- стержень располагается преимущественно в нижней полуформе, а в верхней полуформе нет необходимости подвешивать стержень, проще контролировать их установку в форму, возможность повреждения околознаковых уменьшен;
- снижаются затраты на обрубку и зачистку отливки;
- позволяет снизить расход формовочного песка за счет уменьшения высоты формы
, так как эта распределительная поверхность обеспечивает меньшую высоту формы;
- в литой модели нет съемных деталей.
2.4 Обоснование величины усадки и припусков на механическую обработку, уклонов, галтелей
Усадка - это свойство металлов и сплавов уменьшать свой объем во время затвердевания и охлаждения. В результате модель должна быть намного больше будущих отливок. Уменьшение линейных размеров слитка при определенных производственных условиях называется литейной усадкой. Для каждой конкретной отливки его величина зависит от марки сплава, его конфигурации и устройства формы.
Для малых и средних сплавов из углеродистой стали (35Л) усадка сплава составляет 2%.
Припуски на механическую обработку предоставляются на все обрабатываемые литейные поверхности. Величина припуска зависит от положения поверхности при отливке, способа формовки и чистоты обработки поверхности, а также от величины отливки и самой обрабатываемой поверхности.
Из-за высокой точности литья при машинной формовке припуски на обработку даются меньше, чем при ручной формовке. Наибольшие припуски вносятся в облицовочные поверхности при литье, так как они часто забиваются неметаллическими примесями.
Наклон рабочих поверхностей литейных моделей нормальных поверхностей называется уклоном, который обеспечивает их свободное извлечение из форм или освобождение стержневых ящиков от стержней без разрушения, если конструкция детали не обеспечивает конструктивные уклоны.
Величина уклона зависит от высоты стены, материала модели и способа формирования. Уклон алюминиевых моделей для машинной формовки составляет 0,5-1. Принимаем 1.
Галтелями называются закругления внутренних углов моделей для получения в отливке плавного перехода от одной поверхности к другой. Они улучшают качество отливки, способствуют равномерному ее охлаждению, уменьшают опасность появления горячих трещин в местах пересечения стенок и предотвращают осыпание формовочной смеси в углах формы при извлечении из нее модели. Благодаря правильно выполненным закруглениям наружных и внутренних стенок удается избежать возникновения усадочных раковин.
2.5 Определение конструкции и размеров знаков стержней
Литейные стержни - это элементы литейной формы, которые изготавливаются на специальном (как правило) оборудовании отдельно от полуформ и предназначены для получения в отливке отверстий и полостей, которые не могут быть получены с модели. После сушки стержни формуют, что увеличивает их прочность и снижает газотворность.
Стержневые знаки используются для обеспечения правильного и надежного крепления стержня к форме и для удаления из него газов во время литья.
При проектировании стержней понадобится:
- определить границы стержней и их количество;
- выбрать размеры знаковых частей и определить размер зазоров между разметками стержневой формы;
- обеспечение прочности стержневой смеси подбором соответствующего состава или установкой каркасов;
- выбор способа приготовления, указание плоскости стержневых ящиков и направления набивки;
- разработка систем вентиляции.
При конструировании стержней руководствуемся следующими соображениями:
- стержень находится в нижней полуформе, так как установка и закрепление стержня к верхней опоке занимает в 5-6 раз больше времени, чем в нижней;
- избегаем односторонне посаженных стержней, для чего используем метод дублирования стержней; это исключает возможность их смещения под действием собственной массы или давления металла;
- конструкция формы предотвращает прикрепление одних стержней в знаках других, так как в этом случае будут суммироваться погрешности в их установке.
2.6 Литниковая система
2.6.1 Элементы литниковой системы и их назначение
Литниковая система (л.с.) должна обеспечивать плавную, равномерную и непрерывную подачу металла к заданным отливкам.
В конструкции л.с. должны быть созданы условия, предотвращающие засасыванию воздуха потоком металла.
Л.с. должна задерживать в потоке металла все неметаллические примеси.
Одна из важнейших особенностей л.с. заполнение формы с заданной скоростью: при очень большой скорости заливки происходит, размыв стенок формы и каналов самой л.с., а при слишком медленной заливке – значительное охлаждение металла и образование спаев, неслитин, недоливов.