Файл: Физикотехнологические основы получения композиционных материалов.doc
ВУЗ: Не указан
Категория: Не указан
Дисциплина: Не указана
Добавлен: 07.11.2023
Просмотров: 270
Скачиваний: 4
СОДЕРЖАНИЕ
Физико-технологические основы получения композиционных материалов
1.1. Характеристика композиционных материалов
1.2. Классификация композиционных материалов
1.3. Требования, предъявляемые к армирующим и матричным материалам
Изготовление изделий из металлических композиционных материалов
2.3. Способы получения полуфабрикатов и готовых изделий
3.2. Краткая характеристика порошковых материалов
3.3. Приготовление смеси и формообразование заготовок
3.4. Спекание и окончательная обработка заготовок
4. Изготовление деталей из полимерных композиционных материалов
4.3. Способы формообразования деталей в высокоэластичном состоянии
5. Получение деталей из композиционных пластиков
7. Технологические особенности проектирования и изготовления деталей из композиционных материалов
7.1. Технологические требования к конструкциям изготовляемых деталей
7.2. Технологические особенности дополнительной механической обработки заготовок
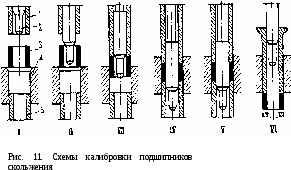
Для повышения износостойкости деталей применяют операцию сульфидирования; для придания спеченным заготовкам необходимых размеров и формы - калибровку, протягивание, штамповку и обработку резанием.
Калибровка позволяет получать детали высокой точности. Эту операцию проводят в специальных пресс-формах или приспособлениях.
Большая степень деформации при калибровке может значительно повысить прочность и снизить пластичность деталей. Поэтому после калибровки применяют дополнительное спекание или отжиг.
Рассмотрим схему последовательных операций калибровки подшипников скольжения на автоматическом прессе (рис. 11). Специальный захват устанавливает подшипник 3 над отверстием калибрующей матрицы 4 (положение I). Затем направляющая часть центрального стержня 2 входит во внутреннюю часть подшипника (положение II) и верхний пуансон 1 вдавливает подшипник в матрицу 4 (положение III). После этого центральный стержень продвигается вниз, и его калибрующая часть проходит через подшипник (положение IV). Этим осуществляется калибровка внутреннего и наружного диаметров. Для обеспечения калибровки по высоте нижний 5 и верхний / пуансоны продолжают движение навстречу друг другу до заданного предела (положение V). Затем нижний пуансон отводится вниз, а центральный стержень -вверх, и верхний пуансон 1 при дальнейшем своем ходе проталкивает подшипник из матрицы вниз (положение VI), после этого цикл повторяется. Такое последовательное расчленение деформаций на ряд операций позволяет снизить усилие калибровки в 2 ... 3 раза по сравнению с калибровкой, при которой деформация производится почти одновременно. Предварительная пропитка заготовок маслом значительно облегчает процесс.
4. Изготовление деталей из полимерных композиционных материалов
4.1. Классификация и технологические свойства пластмасс
Пластическими массами (пластмассами) называют материалы, основу которых составляют природные или синтетические высокомолекулярные соединения. Высокомолекулярные соединения состоят из большого числа низкомолекулярных соединений (мономеров), связанных между собой силами главных валентных связей. Соединения, большие молекулы (макромолекулы) которых состоят из одинаковых структурных звеньев, называют полимерами. Макромолекулы полимеров могут иметь линейную форму, разветвленную и пространственную (сшитую).
Линейные макромолекулы (рис. 12, а) имеют форму цепей, в которых атомы соединены между собой ковалентными связями. Отдельные цепи связаны межмолекулярными силами, в значительной степени определяющими свойства полимера.
Полимеры с линейной структурой молекул хорошо растворяются, так как молекулы растворителя могут внедряться в промежутки между макромолекулами и ослаблять межмолекулярные силы.
Наличие в цепях разветвлений (рис. 12, б) приводит к ослаблению межмолекулярных сил и тем самым к снижению температуры размягчения полимера.
Пространственные структуры (рис. 12, в) получаются в результате химической связи (сшивки) отдельных цепей полимеров либо в результате поликонденсации или полимеризации. Большое значение для свойств этих полимеров имеет частота поперечных связей. Если эти связи располагаются сравнительно редко, то образуется полимер с сетчатой структурой. При частом расположении связей полимер становится практически не растворимым и не плавким.
Полимеры в зависимости от расположения и взаимосвязи макромолекул могут находиться в аморфном (с неупорядоченным расположением молекул) или кристаллическом (с упорядоченным расположением молекул) состоянии. При переходе полимеров из аморфного состояния в кристаллическое повышаются их прочность и теплостойкость. Значительное влияние на полимеры оказывает теплота. В зависимости от поведения при повышенных температурах полимеры подразделяют на термопластичные (термопласты) и термореактивные (реактопласты).
Термопласты при нагреве размягчаются и расплавляются и при охлаждении вновь восстанавливают свои свойства. Переход термопластов из одного физического состояния в другое может осуществляться неоднократно без изменения химического состава. Термопласты имеют линейную или разветвленную структуру молекул.
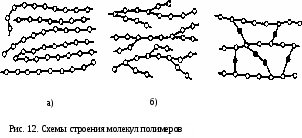
Реактопласты при нагреве в результате химических реакций (отверждения) переходят в необратимое состояние. Отвержденные реактопласты нельзя повторным нагревом перевести в вязкотекучее состояние. В процессе полимеризации под действием указанных факторов линейная структура полимера превращается в пространственную. Отдельные виды термореактивных смол (эпоксидные, полиэфирные) при введении в них отвердителя отверждаются при нормальной температуре.
Поведение термопластов и реактопластов под действием теплоты имеет решающее значение при технологическом процессе переработки пластмасс.
В зависимости от числа компонентов все пластмассы подразделяются на простые и композиционные. Простые (полиэтилен, полистирол и т.д.) состоят из одного компонента - синтетической смолы, композиционные (фенопласты, аминопласты и др.) - из нескольких составляющих, каждая из которых выполняет определенную функциональную роль. В композиционных пластмассах смола является связующим для других составляющих. Свойства связующего во многом определяют физико-механические и технологические свойства ПКМ. Большинство смол хорошо смачивают поверхность наполнителя. Содержание связующего в пластмассах достигает 30 - 70%.
Помимо связующего в состав композиционных пластмасс входят следующие компоненты: 1) наполнители различного происхождения для повышения механической прочности, теплостойкости, уменьшения усадки и снижения стоимости композиции; органические наполнители -древесная мука, хлопковые очесы, целлюлоза, хлопчатобумажная ткань, бумага, древесный шпон и др.; неорганические -графит, асбест, кварц, стекловолокно, стеклоткань, волокна углерода, бора и др.; 2) пластификаторы (дибутилфталат, касторовое масло и др.), увеличивающие эластичность, текучесть, гибкость и уменьшающие хрупкость пластмасс; 3) смазочные вещества (стеарин, олеиновая кислота и др.), увеличивающие текучесть, уменьшающие трение между частицами композиции, устраняющие прилипание к формообразующим поверхностям пресс-форм; 4) катализаторы (известь, магнезия и др.), ускоряющие процесс отверждения материала; 5) красители (сурик, нигрозин и др.), придающие нужный цвет изготовляемым деталям.
При изготовлении газонаполненных пластмасс (поро- и пенопластов) в полимеры вводят газообразователи - вещества, которые при нагреве разлагаются с выделением газообразных продуктов.
Конструкционные пластмассы в зависимости от показателей механической прочности подразделяют на три основные группы: низкой, средней и высокой прочности.
Основными технологическими свойствами пластмасс являются текучесть, усадка, скорость отверждения (реактопластов) и термостабильность (термопластов).
Текучесть - способность материалов заполнять форму при определенных температуре и давлении. Она зависит от вида и содержания в материале смолы, наполнителя, пластификатора, смазочного материала, а также от конструктивных особенностей пресс-формы. Для ненаполненных термопластов за показатель текучести принимают "индекс расплава" - количество материала, выдавливаемого через сопло диаметром 2,095 мм при определенных температуре и давлении в единицу времени.
Под усадкой понимают уменьшение размеров детали по сравнению с размером полости пресс-формы. Величина усадки зависит от физико-химических свойств связующей смолы, количества и природы наполнителя, содержания в нем влаги и летучих веществ, температурного режима переработки и других факторов. Усадку необходимо учитывать при проектировании формообразующих размеров пресс-формы.
Продолжительность процесса перехода реактопластов из вязкотекучего состояния в состояние полной полимеризации определяется скоростью отверждения, которая зависит от свойств связующего (термореактивной смолы) и температуры переработки. Низкая скорость отверждения увеличивает время выдержки материала в пресс-форме под давлением и снижает производительность процесса. Повышенная скорость может вызвать преждевременную полимеризацию материала пресс-формы, в результате чего отдельные участки формующей полости не будут заполнены пресс-материалом.
Под термостабильностью понимают время, в течение которого термопласт выдерживает определенную температуру без разложения. Высокую термостабильность имеют полиэтилен, полипропилен, полистирол и др. Переработка их в детали сравнительно проста. Для материалов с низкой термостабильностью (полиформальдегид, поливинилхлорид и др.) необходимо предусматривать меры, предотвращающие возможность разложения их в процессе переработки: например, увеличение сечения литников, диаметра цилиндра и т.д.
В зависимости от физического состояния, технологических свойств и других факторов все способы переработки пластмасс в детали подразделяют на следующие основные группы: переработка в вязкотекучем состоянии (прессованием, литьем под давлением, выдавливанием); переработка в высокоэластичном состоянии (пневмо- и вакуум-формовкой, штамповкой); получение деталей из жидких пластмасс различными способами формообразования; переработка в твердом состоянии разделительной штамповкой и обработкой резанием; получение неразъемных соединений сваркой, склеиванием; различные способы переработки (спекание, напыление и др.).
4.2. Способы формообразования деталей в вязкотекучем состоянии
Большинство пластмасс перерабатывают в детали в вязкотекучем состоянии способами прессования, литья, выдавливания.
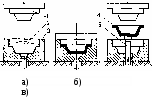
Прямое (компрессионное) прессование - один из основных способов переработки реактопластов в детали. В полость матрицы пресс-формы 3 (рис. 13, а) загружают предварительно таблетизирован-ный или порошкообразный материал 2. При замыкании пресс-формы под действием силы пресса пуансон 1 создает давление на прессуемый материал (рис. 13, б). Под действием этого давления и теплоты от нагретой пресс-формы материал размягчается и заполняет формообразующую полость пресс-формы. После определенной выдержки, необходимой для отверждения материала, пресс-форма раскрывается и с помощью выталкивателя 5 из нее извлекается готовая деталь 4 (рис. 13, в).
Рис. 8.13. Схемы прямого прессования
Процесс отверждения сопровождается выделением летучих составляющих композиционного материала и паров влаги. Для удаления газов в процессе прессования выполняют так называемую под-прессовку, заключающуюся в переключении гидропресса после определенной выдержки на обратный ход, в подъеме пуансона на 5 - 10 мм и выдержке его в таком положении в течение 2 - 3 с. После этого пресс-форма снова смыкается. При прессовании крупных толстостенных деталей из материалов с повышенной влажностью подпрессовку проводят дважды.
Температура и давление прессования зависят от вида перерабатываемого материала, формы и размеров изготовляемой детали. Время выдержки под прессом зависит от скорости отверждения и толщины прессуемой детали. Для большинства реактопластов время выдержки выбирают из расчета 0,5 - 2 мин на 1 мм толщины стенки. Технологическое время может быть сокращено вследствие предварительного подогрева материала в специальных шкафах. Давление зависит от текучести пресс-материала, скорости отверждения, толщины прессуемых деталей и других факторов.
Нагрев пресс-формы осуществляют обычно электронагревателем. Рабочую температуру в процессе прессования поддерживают постоянной с помощью автоматически действующих приборов. Для загрузки в полость пресс-формы определенного количества пресс-материала используют объемную дозировку или дозировку по массе. Применяют также поштучную дозировку (загружают определенное число таблеток). Прессуют на гидравлических прессах. При выпуске большого числа деталей используют прессы, работающие по автоматическому циклу.
Прямым прессованием получают детали средней сложности и небольших размеров из термореактивных композиционных материалов с порошкообразным и волокнистым наполнителями.
Литьевое прессование отличается от прямого тем, что прессуемый материал загружают не в полость формы, а в специальную загрузочную камеру 2 (рис. 14). Под действием теплоты от пресс-формы прессуемый материал переходит в вязко-текучее состояние и под давлением со стороны пуансона 1 выжимается из загрузочной камеры 2 в полости матрицы пресс-формы через специальное отверстие в литниковой плите 3. После отверждения материала пресс-форму разъединяют и готовые детали 4 извлекают из матрицы 5.
Литьевое прессование позволяет получать детали сложной формы, с глубокими отверстиями, в том числе резьбовыми. Возможна установка сложной и тонкой арматуры. В процессе протекания через литниковое отверстие пресс-материал прогревается одинаково, что обеспечивает более равномерную структуру прессуемой детали. При литьевом прессовании отпадает необходимость в подпрессовках, так как образующиеся газы могут выходить в зазор между литниковой плитой и матрицей.
Недостатком литьевого прессования является повышенный расход пресс-материала, так как в загрузочной камере и литниковых каналах остается часть от-вержденного и неиспользуемого в дальнейшем пресс-материала. Кроме того, пресс-формы для литьевого прессования сложнее по конструкции и дороже пресс-форм для прямого прессования.
Д
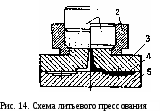
ля прессования деталей применяют одно- и многогнездные пресс-формы. Многогнездные пресс-формы используют для получения деталей простой формы и небольших размеров.
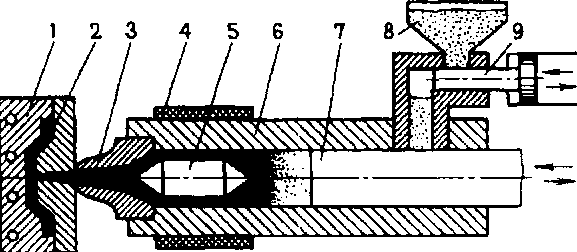