ВУЗ: Не указан
Категория: Не указан
Дисциплина: Не указана
Добавлен: 03.12.2023
Просмотров: 172
Скачиваний: 1
ВНИМАНИЕ! Если данный файл нарушает Ваши авторские права, то обязательно сообщите нам.
СОДЕРЖАНИЕ
1. ХАРАКТЕРИСТИКА ТВЕРДЫХ ЛЕКАРСТВЕННЫХ ФОРМ
2.1. Классификация и характеристика порошков.
2.2. Технология производства порошков.
2.3. Производство порошков методом распылительной сушки.
2.4. Производство порошков с применением сверхкритических флюидов.
3. ТАБЛЕТКИ, ПОКРЫТЫЕ ОБОЛОЧКОЙ.
3.1. Технология производства таблеток.
3.1.1. Метод прямого прессования.
3.1.2. Таблетирование, через предварительное гранулирование.
3.2. Покрытие таблеток оболочками.
3.2.3. Дражировочное покрытие.
2.2.4. Фасовка и упаковка.
Промышленная фармация выпускает порошки как в однодозовых упаковках, так и в многодозовых.
Однодозовые представлены пакетами или стиками из фольги, специальных видов бумаги или полиэтиленцеллюлозной пленки. Многодозовые упаковки– это стеклянные банки из темного стекла, пластиковые флаконы с просеивающими крышками, упаковки с механическим распылителем, контейнеры под давлением, полиэтиленовые или многослойные бумажные пакеты [8].
Фасовка осуществляется с помощью дозаторов, работающих по объемному принципу. Шнековый дозатор, представлен на рисунке 5.
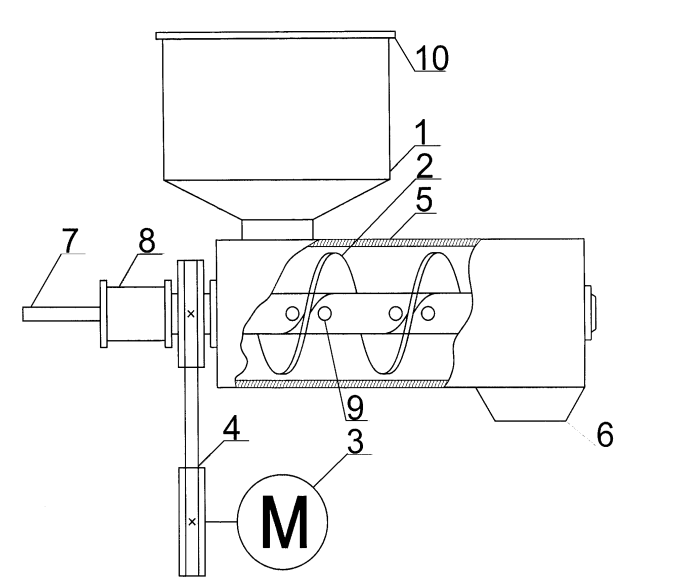
Рисунок 5. Шнековый дозатор.
Шнековый дозатор для сыпучих материалов содержит загрузочный бункер - 1, полый шнек - 2, привод дозатора, включающий двигатель - 3 и ременную передачу - 4, корпус - 5, разгрузочное отверстие корпуса - 6, пневмолинию - 7, сальниковый узел - 8, полый шнек снабжен сквозными отверстиями - 9, загрузочный бункер запирается крышкой - 10. В процессе дозирования сжатый воздух из пневмолинии подводится через сальниковый узел в полый шнек. Сжатый воздух поступает во внутренний объем дозатора через сквозные отверстия, придавая сыпучему материалу свойство «псевдотекучести». Таким образом, формируется «псевдоожиженная» среда, которая легко транспортируется вдоль корпуса за счет снижения сил трения. При этом наблюдается значительное снижение количества перемалываемого материала. Техническое решение позволяет снизить разрушительное механическое воздействие на дозируемый материал [6].
2.3. Производство порошков методом распылительной сушки.
Производство порошков методом распылительной сушки используется в фармацевтической технологии для получения: ингаляционных и инъекционных порошков, витаминов и протеинов, сухих растительных экстрактов, субстанций и вспомогательных веществ для твердых лекарственных форм.
Процесс распылительной сушки (рисунок 6) включает: распыление прокачиваемого материала с формированием капель; контакт капель с воздухом (или другим осушающим газом); увлечение капель потоком воздуха; испарение летучих веществ из капель, формирование частиц и сушка;
отделение частиц от воздуха и выгрузка; последующая обработка полученного продукта.
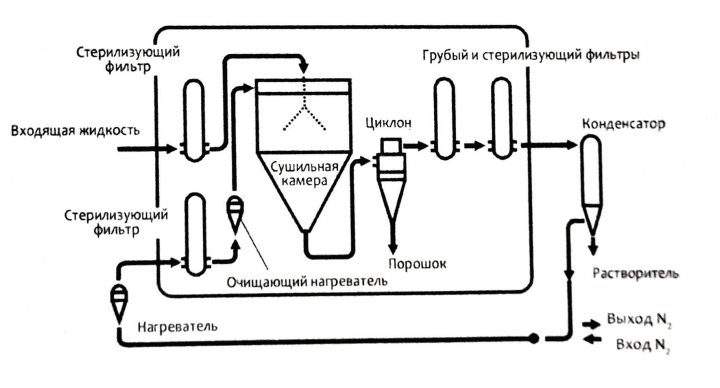
Рисунок 6. Схема работы распылительной сушилки.
2.4. Производство порошков с применением сверхкритических флюидов.
Сверхкритические флюиды (СКФ) – это вещества, находящиеся в сверхкритическом состоянии, т.е. при температурах и давлениях, превышающих их критические значения. Они объединяют свойства жидкости и газа. В основном в производстве используется сверхкритический диоксид углерода – CKCO2. Он не токсичен, не горюч и не взрывоопасен, следовательно его можно считать экологически чистым растворителем [10].
Порошки с помощью СКФ получают напрямую в микронизированном виде. Свойства таких порошков оптимизированы, так как поверхность всех частиц «выращена» естественным путем, распределение частиц по размеру более однородно и порошок менее склонен к агломерации [10].
Так, например, с помощью технологии СКФ получен порошок меди, применяющийся в качестве антибактериального компонента. На СЭМ-изображениях представлена структура полученного медного порошка (рисунок 7) [12].
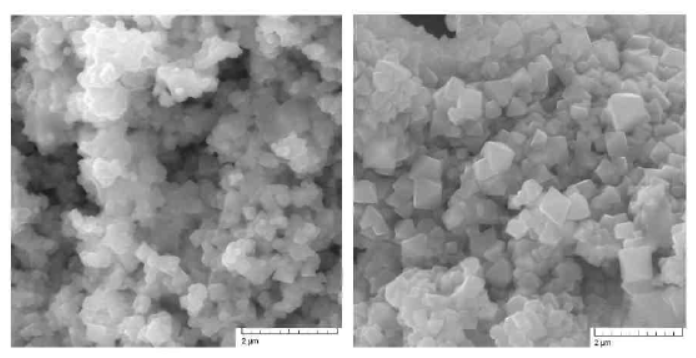
Рисунок 7. Морфология медных порошков.
2.5. Испытание порошков.
В соответствии с ОФС.1.4.1.0010.15 «Порошки» для порошков установлен ряд требований.
1. Описание.
Порошки должны быть однородными при рассмотрении невооруженным глазом и иметь размер частиц не более 160 мкм, если не указано иное в фармакопейной статье или нормативной документации.
2. Размер частиц.
Размер частиц порошков для наружного применения определяют ситовым анализом в соответствии с требованиями ОФС «Ситовой анализ» или другим валидированным методом.
3. Количественное определение.
Для количественного определения берут навеску не менее 10 г порошка.
Если не указано иначе в фармакопейной статье или нормативной документации, содержание определяемых веществ выражается в мг или ЕД в одной дозе для дозированных порошков или в 1 г препарата для не дозированных порошков.
Дозированные порошки должны выдерживать требования ОФС «Однородность дозирования» и ОФС «Однородность массы дозированных лекарственных форм».
Особенности испытаний отдельных лекарственных форм.
1. Порошки для местного применения и/или для приготовления растворов или суспензий для местного применения - порошки для местного применения, а также полученные из них растворы или суспензии, предназначенные для использования на открытых ранах или на поврежденной коже, должны быть стерильными.
Порошки для приготовления раствора или суспензии для парентерального применения должны быть стерильными и должны соответствовать требованиям ОФС «Лекарственные формы для парентерального применения».
Порошки для приготовления капель глазных должны соответствовать требованиям ОФС «Глазные лекарственные формы».
2. Порошки для приготовления суспензий для приема внутрь.
Для порошков, используемых для приготовления суспензий для приема внутрь, должен быть дополнительно предусмотрен контроль получаемой суспензии по показателям «размер частиц» и «седиментационная устойчивость» в соответствии с требованиями ОФС «Суспензии».
3. Порошки для ингаляций.
Испытание однородности дозирования порошков для ингаляций проводят в соответствии с требованиями ОФС «Лекарственные формы для ингаляций».
Для дозированных порошков для ингаляций дополнительно определяют содержание респирабельной фракции в одной дозе порошка в соответствии с ОФС «Аэродинамическое распределение мелкодисперсных частиц» и количество доз в соответствии с ОФС «Лекарственные формы для ингаляций» [1].
3. ТАБЛЕТКИ, ПОКРЫТЫЕ ОБОЛОЧКОЙ.
Таблетки – твердая дозированная лекарственная форма, чаще всего получаемая прессованием порошков или гранул, содержащих одно или более действующих веществ с добавлением или без вспомогательных веществ [1].
Наибольший интерес, в виду улучшения фармакологических и физических свойств, представляют собой таблетки, покрытые оболочкой.
Таблетки, покрытые оболочкой – таблетки, покрытые одним или несколькими слоями смеси различных веществ, предназначенные для приема внутрь. В зависимости от состава и способа нанесения различают дражировочное, пленочное и прессованное покрытия [1].
Покрытие таблеток оболочкой преследует следующие цели:
-
защита таблеток от механического воздействия (ударов, истирания, и.др.); -
защита от воздействий окружающей среды (света, влаги, кислорода и углекислоты воздуха); -
защита от окрашивающей способности лекарственных веществ, содержащихся в таблетках (например, таблетки активированного угля); -
защита содержащихся в таблетках лекарственных веществ от кислой реакции желудочного сока; -
защита слизистой рта, пищевода и желудка от раздражающего действия лекарственных веществ; -
маскировка неприятного вкуса и запаха содержащихся в таблетках лекарственных веществ; -
локализация терапевтического действия лекарственных веществ в определенном отделе желудочно-кишечного тракта; -
предотвращение нарушений процессов пищеварения в желудке, возможных при нейтрализации желудочного сока лекарственными веществами основного характера; -
пролонгирование терапевтического действия лекарственных веществ в таблетках; -
преодоление несовместимости различных веществ, находящихся в одной таблетке путем введения их в состав оболочки и ядра; -
улучшение товарного вида таблеток и удобства их применения [8].
3.1. Технология производства таблеток.
Технологический процесс производства таблеток складывается из следующих этапах, изображенных на рисунке 8.
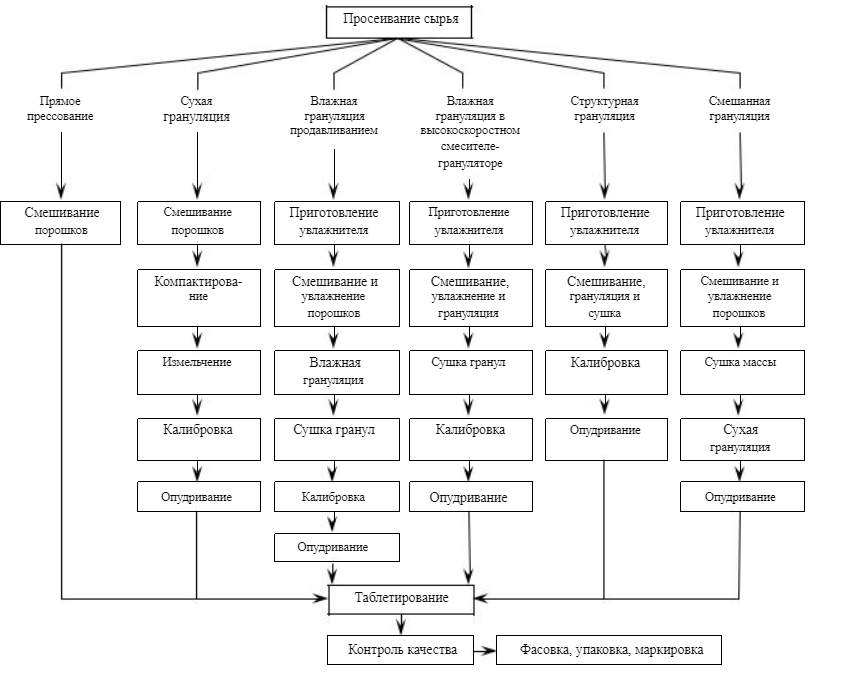
Рисунок 8. Схема технологического процесса производства таблеток.
В настоящее время существует два пути получения таблеток: путем прямого прессования и через предварительное гранулирование.
3.1.1. Метод прямого прессования.
Метод прямого прессования обладает рядом преимуществ. Он позволяет достичь высокой производительности труда, значительно сократить время технологического цикла за счет упразднения ряда операций и стадий, исключить использование нескольких позиций оборудования, уменьшить производственные площади, сократить энерго- и трудозатраты, значительно снижая себестоимость таблеток. Прямое прессование дает возможность получать таблетки из влаго-, термолабильных и несовместимых веществ. На сегодняшний день, однако, этим методом получают незначительное количество наименований таблеток.
Это объясняется тем, что большинство лекарственных веществ не обладают свойствами, обеспечивающими непосредственное их прессование. К этим свойствам относятся:
-
изодиаметрическая форма кристаллов; -
хорошая текучесть и прессуемость; -
низкая адгезионная способность к пресс-инструменту таблеточной машины.
Такими характеристиками обладает лишь небольшое число ЛВ: натрия хлорид, калия иодид, натрия и аммония бромид, уротропин, бромкамфора, ПАСК-натрий и некоторые другие.
Технология приготовления таблеток заключается в том, что ЛП тщательно смешивают с необходимым количеством вспомогательных веществ и прессуют на таблеточных машинах [8].
В современном таблеточном производстве для получения таблеток в основном используют ротационные таблеточные машины (РТM).
На фармацевтических производствах используются таблеточные машины марок IMA, Romaco Kilian (Италия), Manesty (Англия), Fette, Korsch (Германия), POZIS PRT-41 MI, PTM-24, PTM-41 и др.
Основными узлами РТM являются: ротор; корпус; привод; питатель; узел прессования; система копиров (верхний и нижний).
Таблетируемый материал загружается в бункер, из которого он равномерно распределяется на диске с помощью питателя. Излишек массы снимается лопастями ворошителя или ножом. При дальнейшем вращении матричного диска и пуансонов осуществляется прессование. В этот момент пуансоны попадают под прессующие ролики и создается двухстороннее давление. Нижний пуансон выталкивает таблетку на поверхность матрицы, с которой она снимается ножом и попадает в приемник. В отличие от ударных машин, РТМ имеют большое количество матриц и пуансонов (от 12 до 57). Матрицы вмонтированы во вращающийся матричный стол. Пуансоны верхние и нижние скользят по