ВУЗ: Не указан
Категория: Не указан
Дисциплина: Не указана
Добавлен: 03.12.2023
Просмотров: 177
Скачиваний: 1
ВНИМАНИЕ! Если данный файл нарушает Ваши авторские права, то обязательно сообщите нам.
СОДЕРЖАНИЕ
1. ХАРАКТЕРИСТИКА ТВЕРДЫХ ЛЕКАРСТВЕННЫХ ФОРМ
2.1. Классификация и характеристика порошков.
2.2. Технология производства порошков.
2.3. Производство порошков методом распылительной сушки.
2.4. Производство порошков с применением сверхкритических флюидов.
3. ТАБЛЕТКИ, ПОКРЫТЫЕ ОБОЛОЧКОЙ.
3.1. Технология производства таблеток.
3.1.1. Метод прямого прессования.
3.1.2. Таблетирование, через предварительное гранулирование.
3.2. Покрытие таблеток оболочками.
3.2.3. Дражировочное покрытие.
2.2. Технология производства порошков.
Технология производства порошков включает следующие операции:
-
Измельчение; -
Просеивание; -
Смешивание (при изготовлении сложных порошков); -
Дозирование (фасовка); -
Упаковка и маркировка.
Необходимость выполнения некоторых технологических операций зависит от рецептурной прописи, назначения и вида исходных субстанций. Так же, необходимо отметить, что производственный процесс проводиться в соответствии требований правил GMP (Надлежащей производственной практики).
2.2.1. Измельчение.
Если исходные материалы не отвечают требуемому фракционному составу, указанному в регламенте, их подвергают измельчению.
Измельчение – механический процесс деления твердых тел на части.
Совместное измельчение двух и более ингредиентов лежит в основе ряда современных технологий создания эффективных лекарственных препаратов, например за счет механоактивации или получения соединений-включения. При этом рекомендуют использовать оборудование, в котором измельчение осуществляется за счет удара и истирания. Примером такого оборудования является шаровая мельница, отличающаяся надежностью, простотой конструкции и эксплуатации [4].
Шаровая мельница (KM) – насадка к универсальному приводу ERWEKA. Универсальная шаровая мельница (КМ) позволяет быстро и качественно измельчать кристаллические вещества, а также смешивать сухие материалы до получения однородного состава (рисунок 1.)
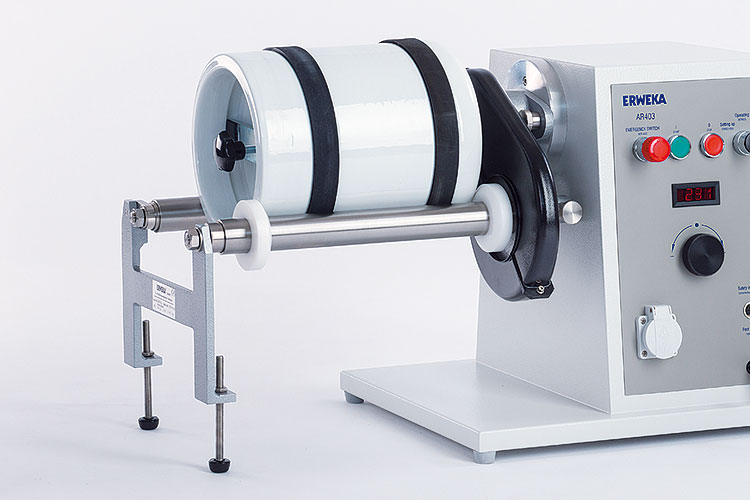
Рисунок 1. Шаровая мельница ERWEKA KM.
В шаровой мельнице измельчение происходит за счет двух основных процессов: удара и истирания, при сочетании которых достигается максимальная эффективность . Для эффективного измельчения полый барабан заполняется шарами на 30-50%. Фарфоровые шары диаметром от 30 до 50 мм обеспечивают тщательное измельчение кристаллического материала. Одновременное использование шаров различных размеров способствуют лучшему измельчению порошков, так как
большие шары обладают высокой силой удара, а маленькие заполняют пространство между большими, обеспечивая более тонкое измельчение. Барабан и измельчающие шары при необходимости можно стерилизовать [4].
2.2.2. Просеивание.
В фармацевтической технологии просеивание осуществляется через одно сито, исходный материал делится на две фракции:
-
просев (нижний продукт) – материал, прошедший сквозь сито; -
отсев (верхний продукт) – материал, не прошедший сквозь сито и оставшийся в нем [2].
Ситовые механизмы применяются двух типов: машины с плоскими ситами и барабанные просеивающие машины.
Среди машин с плоскими ситами наиболее широкое применение нашли просеивающие механизмы, называемые грохотами (рисунок 2) и вибрационные сита (рисунок 3).
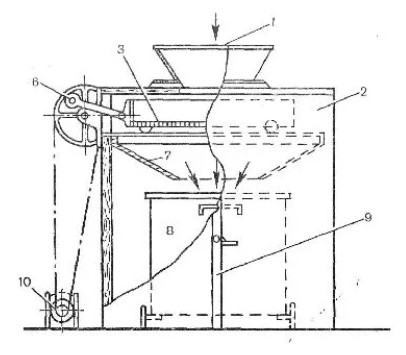
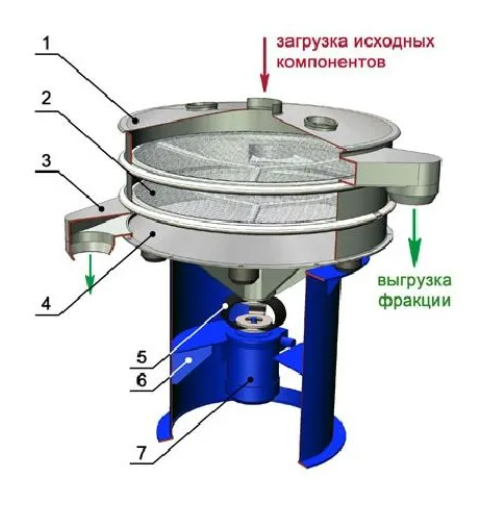
Рисунок 2. Качающееся сито. Рисунок 3. Вибрационное сито.
Барабанные просеивающие машины (бураты) представляют собой вращающиеся барабаны с ситовой поверхностью, установленные слегка под наклоном (рисунок 4).
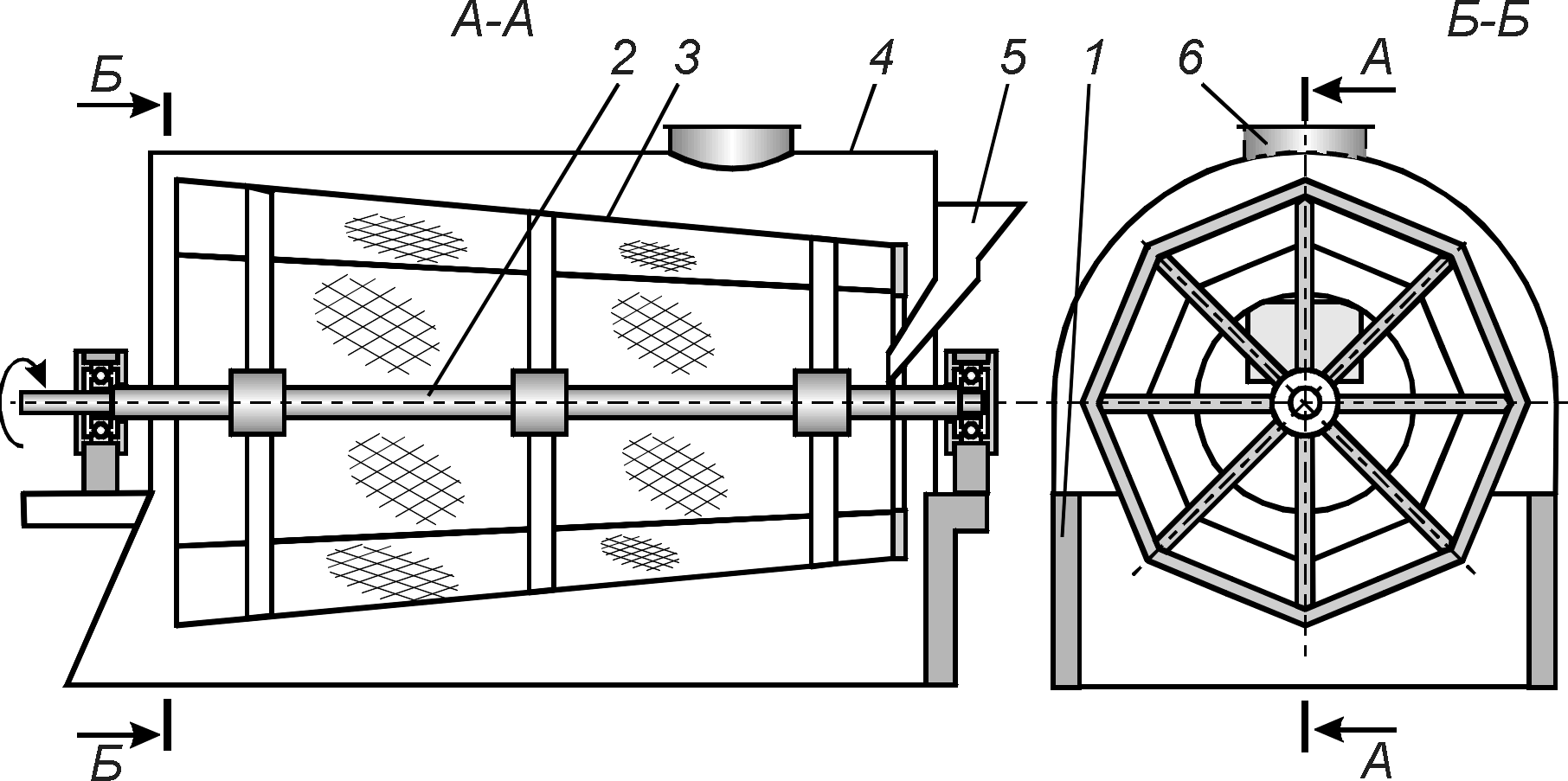
Рисунок 4. Барабанное полигональное сито.
2.2.3. Смешивание.
Смешивание – процесс получения однородной смеси из нескольких компонентов. При получении ЛФ равномерное распределение компонентов в полученной смеси обеспечивает однородность дозирования, что крайне необходимо при производстве ЛП, поэтому качество смешивания – важная характеристика производственного процесса, которая зависит от правильно подобранного оборудования, размеров частиц исходного сырья, длительности проведения процесса и др.
Для смешивания порошкообразных ингредиентов применяют смесители различной конструкции. В линейке лабораторного оборудования ERWEKA имеются несколько емкостных смесителей
, предназначенных для смешивания свободно падающих порошков и гранул: двухконусный смеситель, кубический смеситель (КВ) и.т.д [4]. Виды смесителей представлены в таблице 4.
Таблица 4. Виды смесителей для смешивания порошков.
Кубический смеситель (Cube Mixer KB) - использует вращательное движение для получения однородной смеси за короткое время. Перемешиванию способствуют три стержня из нержавеющей стали, стратегически расположенные внутри куба. | ![]() |
Двухконусный смеситель (Double Cone Mixer DKM) - позволяет смешивать сыпучие порошки и гранулы. Расположение смесителя в сочетании с регулировкой угла наклона универсального редуктора UG обеспечивает многомерный процесс перемешивания. | ![]() |
Y-образный смеситель (Mixer Y5) - для бережного смешивания твердых, хорошо текучих материалов (сыпучих материалов). Вращательное движение смесительной емкости обеспечивает получение особенно однородной смеси, и, следовательно, устройство подходит для чувствительных материалов. | ![]() |
V-образный смеситель (V-Mixer VB-3) - для бережного смешивания твердых, хорошо текучих материалов (сыпучих материалов). | ![]() |
Существенное достоинство смесителей – это простая конструкция, повторяющая аналогичное промышленное оборудование. Другое преимущество заключается в том, что смешиваемая композиция контактирует исключительно со стенками стерильно чистой и герметически замкнутой емкости. Объемы смесителей – от 3,5 до 11,8 л, что позволяет их применять как для лабораторных, так и для пилотных наработок. В целях корректной работы прибора и получения смеси с заданными характеристиками не рекомендуется заполнять смешивающий сосуд более чем на 40% от его объема [4].