ВУЗ: Не указан
Категория: Не указан
Дисциплина: Не указана
Добавлен: 10.01.2024
Просмотров: 351
Скачиваний: 1
СОДЕРЖАНИЕ
1 Регламент производства винилхлорида
1.1.1 Ректификация продуктов пиролиза в колонне С-601
1.1.2 Ректификация винилхлорида в колонне С-602
1.1.3 Отпарка хлористого водорода в колонне С-603
1.1.4 Нейтрализация и сушка винилхлорида
1.1.5 Отпарка хлористого водорода в колонне С-603
1.2 Контроль производства и нормы управления технологическим процессом
2 Изучение технологического процесса
2.1 Выбор объекта автоматизации
2.2 Математическое описание колонны
2.4Тепловой баланс колонны ректификации
2.4.1 Тепловой баланс низа колонны
2.4.2 Тепловой баланс кипятильника
2.4.3 Тепловой баланс верха колонны
2.5 Материальный баланс колонны ректификации
2.5.1 Материальный баланс низа колонны по всему веществу
2.5.2 Материальный баланс по легколетучему компоненту
2.5.3 Материальный баланс верха колонны по всему веществу
2.5.4 Материальный баланс по целевому компоненту.
2.5 Информационные схемы колонны ректификации
3 Автоматизация процесса ректификации в колонне С-602
3.1 Технологические параметры контроля и управления
3.2 Автоматическое регулирование параметров в колонне С-602
3.3 Сигнализация и контроль допустимых параметров
3.4 Блокировка технологических параметров
3.5 Структура технических средств
3.6 Подбор промышленных средств автоматизации
3.6.1 Главные условия подбора средств автоматизации среднего уровня
3.6.2 Обоснование выбора технических средств среднего уровня
3.6.4 Подбор средств автоматизации нижнего уровня
4.1 Расчёт регулирующего органа
4.1.1 Построение расходной характеристики
4.3 Рабочее место оператора АСУТП
4.4 Создание общего вида визуализации
4.4.1 Закрепление визуализации за реальными объектами
4.4.2 Создание программ сигнализации и автоматического регулирования температуры.
4.4.3 Контроль технологического процесса и управления в реальном времени
5 Расчет экономических показателей проекта автоматизации
5.1 Расчет затрат на модернизацию оборудования автоматизации
5.2 Расчет увеличения производственной мощности колонны ректификации
5.2.1 Расчёт изменения затрат по статьям себестоимости от внедрения новой системы автоматизации
5.2.3 Таблица расчета затрат на единицу продукта
5.2.4 Расчет показателей экономической эффективности проектного варианта автоматизации
5.2.5 Таблица сравнения показателей базового и проектного варианта автоматизации объекта
6.1 Характеристика и анализ вредных и опасных производственных факторов на стадии 600
6.2 Производственная санитария
6.3 Параметры микроклимата рабочей зоны в производственном помещении
6.4.1 Требования охраны труда во время работы
6.4.2 Требования охраны труда в аварийных ситуациях
Список используемых источников
Приложение А. Схема автоматизации
Приложение Б. Схема принципиальная электропитания №1
Приложение В. Схема принципиальная электропитания №2
Приложение Г. Схема принципиальная давления в колонне
Приложение Д. Схема принципиальная контроля выходной температуры продукта
Приложение Е. Схема принципиальная контроля уровня в колонне С-602.
Приложение Ж. Схема принципиальная контроля температуры на тарелках.
Приложение З. Схема принципиальная управления клапаном с ЭИМ по расходу дихлорэтана.
Приложение И. Схема принципиальная управления клапаном с ЭИМ по расходу флегмы.
Приложение К. Схема внешних проводок №1
Приложение Л. Схема внешних проводок №2
Приложение М. Схема внешних проводок №3
При условии, что в этот коллектор вместо конденсата пара подается речная вода. Речная вода очищается от механических примесей в отстойнике на стадии 100 перед подачей в коллектор.
Остальная часть конденсата от нагнетательных насосов Р-606А, В, С, в зависимости от уровня в коллекторе конденсата В-605, поддерживаемого в пределах 20-80% регулятором уровня LRSA-63325, сливается в промышленную дренажную систему. Если уровень снижается менее чем на 20% и увеличивается более чем на 80 %, на AWP срабатывает сигнал тревоги.
Температура подшипников насоса P-606A, B, C не выше 70 C контролируется прибором TR-63631,63632, TR-63633,63634, TR-63635,63636 соответственно.
Контроль качества конденсата осуществляется с помощью анализатора электропроводности ARA-63131. Если электропроводность увеличивается более чем на 30,0 мС / см2, на AРМ срабатывает сигнализация.
1.2 Контроль производства и нормы управления технологическим процессом
В таблице 1 описана основная техника и технологические нормы которые буду применяться в данной дипломной работе.
Таблица 1 – Нормы технологического режима
Название стадий процесса и места измерения параметров | Контролируемый параметр | Частота и метод контроля | Нормы и технические показатели | Способ проверки и средство контроля | Требуемая точность измерения параметров | Контролирует |
1 | 2 | 3 | 4 | 5 | 6 | 7 |
Трубопровод подачи пара в испарители Е-602А,В,С | Массовырасход,кг/ч | Визуально на мнемосхеме Архивирование Непрерывно, автоматически | 1500,0-10000,0 | Канал измерения, сигнализации и управления S7-400 FRСА-61215 шкала 0-12500 погрешность измерения ± 250 | ± 250 | Оператор ДПУ |
| Предупредительная сигнализация минимального расхода | 1500,0 | ||||
| Предупредительная сигнализация максимального расхода | 10000,0 | ||||
Конденсатор – испаритель Е-601 | Уровень, % | Визуально на мнемосхеме Архивирование Непрерывно, автоматически | 25,0-40,0 | Канал измерения и управления S7-400 LRC-61341 шкала 0-100 погрешность измерения ± 4 | ± 4 | Оператор ДПУ |
Продолжение таблицы 1 | ||||||
1 | 2 | 3 | 4 | 5 | 6 | 7 |
Емкость V-601 | Уровень, % | Визуально на мнемосхеме Архивирование Непрерывно, автоматически | 20,0-80,0 | Канал измерения и сигнализации S7-400 LRA-61346 шкала 0-100 погрешность измерения ± 4 | ± 4 | Оператор ДПУ |
Предупредительная сигнализация минимального уровня | 20,0 | |||||
Предупредительная сигнализация максимального уровня | 80,0 | |||||
Трубопровод хлористого водорода из емкости V-601 к конденсатору Е-503 | Давление, МПа (кгс/см2) | Визуально на мнемосхеме Архивирование Непрерывно, автоматически | 1,00-1,45 (10,0-14,5) | Канал измерения, сигнализаци и управления S7-400 РRСА-61491 шкала (0-16) погрешность измерения ±0,03 (±0,3) | ±0,03 (±0,3) | Оператор ДПУ |
Предупредительная сигнализация минимального давления | 1,0 (10,0) | |||||
Предупредительная сигнализация максимального давления | 1,45 (14,5) | |||||
| | | | | | |
| | | | | | |
| | | | | | |
Продолжение таблицы 1 | ||||||
1 | 2 | 3 | 4 | 5 | 6 | 7 |
| Температура, оC | Визуально на мнемосхеме Архивирование Непрерывно, автоматически | минус 31,0 –минус 19,0 | Канал измерения S7-400 ТR-61646 шкала: минус 40-плюс 60, погрешность измерения ± 2 | ±2 | Оператор ДПУ |
Трубопровод вывода кубовых продуктов из колонны С-601 в С-602 | Объемный расход, м3/ч | Визуально на мнемосхеме Архивирование Непрерывно, автоматически | не более 100,0 | Канал измерения S7-400 FR-61221 шкала 0-120 погрешность измерения ±2,4 | ±2,4 | Оператор ДПУ |
Колонна С-602 | Перепад давления, МПа (мм. вод. ст. ) | Визуально на мнемосхеме Архивирование Непрерывно, автоматически | не более 0,08 (8000,0) | Канал измерения и сигнализации S7-400 PdRA-62408 шкала (0-16000) погрешность измерения ± 0,0032 (± 320) | ± 0,0032 (± 320) | Оператор ДПУ |
Предупредительная сигнализация максимального значения | 0,08 (8000,0) | |||||
верх колонны С-602 | Давление, МПа (кгс/см2) | Визуально на мнемосхеме Архивирование Непрерывно, автоматически | 0,4-0,61 (4,0-6,1) | Канал измерения, сигнализации и управления S7-400, РRСА-62435 шкала 0-10 погрешность измерения ±0,02 (±0,2) | ±0,02 (±0,2) | Оператор ДПУ |
Предупредительная сигнализация максимальн | 0,61 (6,1) 0,8 (8,0) | |||||
Продолжение таблицы 1 | ||||||
1 | 2 | 3 | 4 | 5 | 6 | 7 |
куб колонны С-602 | Уровень, % | Визуально на мнемосхеме Архивирование Непрерывно, автоматически | 70,0-85,0 | Канал измерения, сигнализации и управления S7-400, LRCA-62302 шкала 0-100 погрешность измерения ± 4 | ± 4 | Оператор ДПУ |
| Предупредительная сигнализация минимального уровня | 70,0 | | |||
| Предупредительная сигнализация максимального уровня | 85,0 | | |||
| Уровень, % | Визуально на мнемосхеме Архивирование Непрерывно, автоматически | 70,0-85,0 | Канал измерения, сигнализации и управления S7-400 LRСА-62303 шкала 0-100 погрешность измерения ± 4 | ± 4 | |
| Предупредительная сигнализация минимального уровня | 70,0 | | |||
| Предупредительная сигнализация максимального уровня | 85,0 | | |||
| | | | | | |
| | | | | | |
Продолжение таблицы 1 | ||||||
1 | 2 | 3 | 4 | 5 | 6 | 7 |
| Давление, МПа (кг/см2) | Визуально на мнемосхеме Архивирование Непрерывно, автоматически | не более 0,69 (6,9) | Канал измерения S7-400 PR-62407 шкала: (0-10) погрешность измерения ±0,02 (±0,2) | ±0,02 (±0,2) | |
| Температура, оC | Визуально на мнемосхеме Архивирование Непрерывно, автоматически | 154,0-164,0 | Канал измерения S7-400 ТR-62602 , 62603 шкала 0-200 погрешность измерения ± 4 | ± 4 | |
Тарелка № 60 | Температура, оC | Визуально на мнемосхеме Архивирование Непрерывно, автоматически | 36,0-46,0 | Канал измерения S7-400 TR-62617 шкала 0-200 погрешность измерения ± 4 | ± 4 | Оператор ДПУ |
Тарелка № 40 | Температура, оC | Визуально на мнемосхеме Архивирование Непрерывно, автоматически | 30,0-65,0 | Канал измерения S7-400 ТR-62614 шкала 0-200 погрешность измерения ± 4 | ± 4 | Оператор ДПУ |
Тарелка № 20 | Температура, оC | Визуально на мнемосхеме Архивирование Непрерывно, автоматически | 45,0-60,0 | Канал измерения S7-400 ТR-62611 шкала 0-200 погрешность измерения ± 4 | ±4 | Оператор ДПУ |
| | | | | | |
| | | | | | |
Продолжение таблицы 1 | ||||||
1 | 2 | 3 | 4 | 5 | 6 | 7 |
Тарелка № 12 | Температура, оC | Визуально на мнемосхеме Архивирование Непрерывно, автоматически | 30,0-140,0 | Канал измерения S7-400 TR-62609 шкала 0-200 погрешность измерения ± 4 | ±4 | Оператор ДПУ |
Перепад температур между 5 и 12 тарелками | Температура, оC | Визуально на мнемосхеме Архивирование Непрерывно, автоматически | 10,0-60,0 | Канал измерения расчетный S7-400 TdR-62606 шкала 0-100 погрешность измерения ± 2 | ± 2 | Оператор ДПУ |
Тарелка № 5 | Температура, оC | Визуально на мнемосхеме Архивирование Непрерывно, автоматически | 90,0-155,0 | Канал измерения S7-400 TR-62605 шкала 0-200 погрешность измерения ± 4 | ± 4 | Оператор ДПУ |
Имея все необходимые характеристики, параметры и погрешности установок на стадии С-602 можно приступать к расчету теплового баланса и подбору оборудования.
2 Изучение технологического процесса
2.1 Выбор объекта автоматизации
Для выпускной квалификационной работы была выбрана колонна ректификации С-602. На рисунке 2.1 изображено схематическое описание всех технических объектов которые относятся именно к процессу ректификации С-602.
Выбор объекта автоматизации
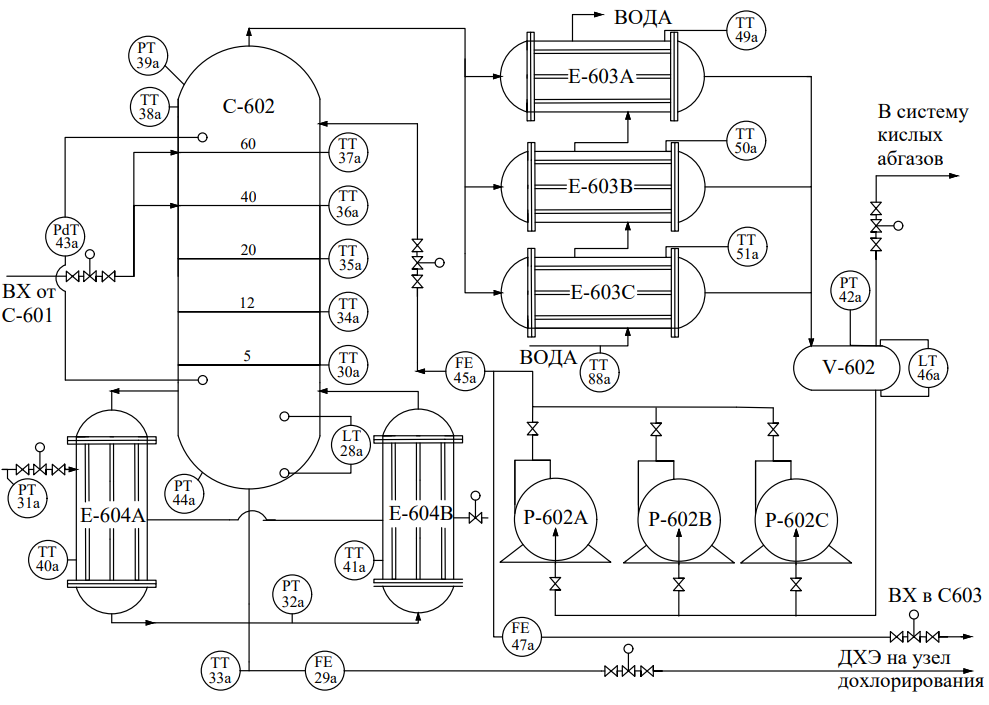
Рис 2.1 - Колонна ректификации С-602 (часть технологической схемы)
Ректификация-это процесс разделения смесей летучих жидких веществ на их составные части, в нашем случае это разделение винилхлорида и дихлорэтана.
Основными этапами ректификации являются:
1) Предварительный нагрев смеси до необходимой температуры..
2) Процесс разделения винилхлорида и дихлорэтана.
3) Процесс охлаждения хладагентом из винилхлорида (в виде пара) до требуемой температуры.
В объекте возникают такие возмущения, как изменение начальных параметров исходной смеси, а также теплоты холодоносителей, изменение свойств поверхностей теплообмена, осаждение веществ на стенках ректификационной колонны, температура окружающей среды вне колонны и др.
Температура смеси, поступающей на вход колонны, имеет большое значение для процесса ректификации. Если смесь начинает поступать в колонну при температуре ниже точки кипения, ее необходимо нагреть до этой температуры парами, поступающими со дна колонны. При этом увеличивается конденсация паров, что нарушает весь режим процесса ректификации. Поэтому температуру исходной смеси стабилизируют путем изменения расхода теплоносителя в теплообменник.
Давление пара в верхней части колонны стабилизируется путем изменения расхода пара из колонны. В этом случае исполнительное устройство размещено не на трубе шлема, соединяющей верхнюю часть дистилляционной колонны с дефлегматором, а на линии хладагента, поступающего в дефлегматор. Это связано с тем, что при дросселированние пара в трубке шлема дефлегматор начинает работать в режиме переменного давления, а это отрицательно сказывается на процессе конденсации.
Процесс, происходящий в установке: когда смесь поступает в колонну, происходит процесс кипения, в то время как этанол в виде пара отделяется от смеси при требуемой температуре и подается по трубопроводу в дефлегматор, где он охлаждается. После этого часть сливают как готовый продукт, а часть как неполный продукт возвращают в колонну для дальнейшей дистилляции. Также в колонне по другому трубопроводу через теплообменник и часть кубического остатка через котел подается в колонну для повторения процесса ректификации.
2.2 Математическое описание колонны
Схема колонны ректификации для математического описания рабочих линий процесса описана на рисунке 2.2.
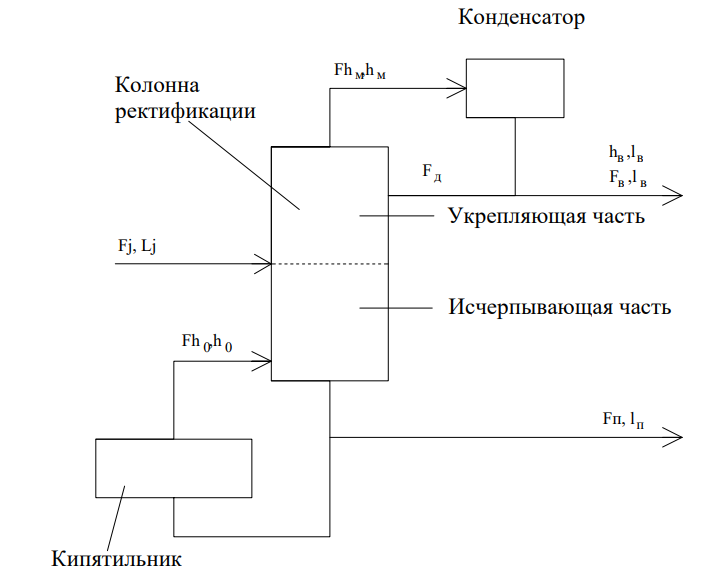
Рис.2.2 Схема колонны ректификации
Обозначения параметров процесса:



Расчет рабочего флегмового числа.

где


Рабочее флегмовое число находят из соотношений:

Или

Где

Уравнение рабочей линии верхней (укрепляющей) части колонны.
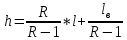
где h, l - составы паровой и жидкой фаз верха колонны
, молярные доли; xд - состав дистиллята.
Обозначим
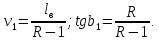
Уравнение рабочей линии нижней (исчерпывающей) части колонны.
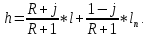
Где

Обозначим:
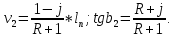
На рисунке 2.3 описана структурная схема установки на основе расчётов выше.
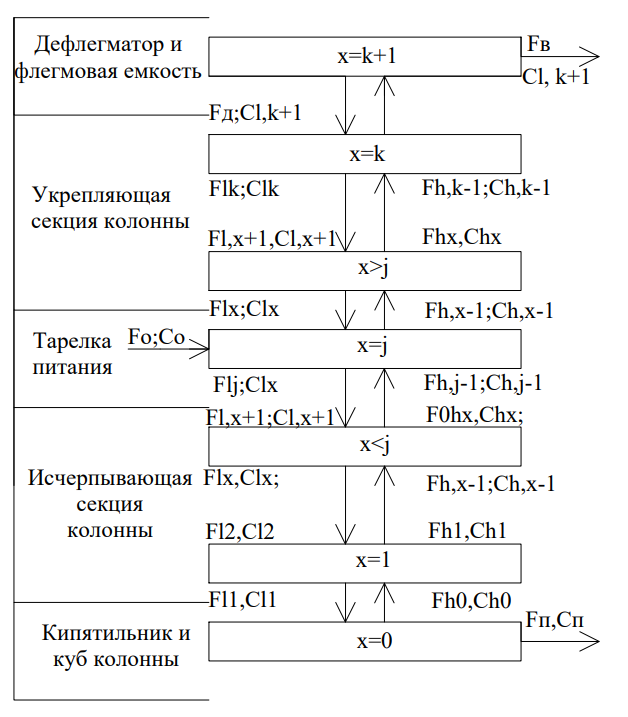
Рис 2.3 Структурная схема ректификационной установки
На рисунке 2.4 очерчено математическое описание нижней части колонны.
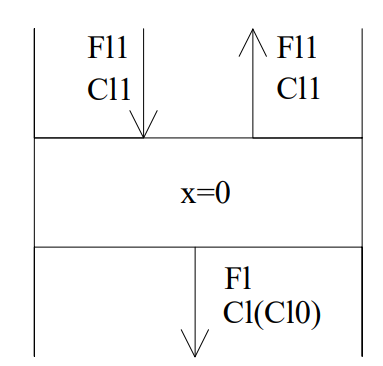
Рис 2.4 Математическое описание низа колонны
На рисунке 2.5 очерчено математическое описание верхней части колонны.
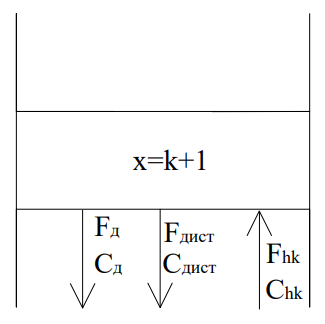
Рис 2.5Математическое описание верха колонны.
На основе посчитанного математического описания можно приступить к расчёту теплового баланса колонны.