ВУЗ: Не указан
Категория: Не указан
Дисциплина: Не указана
Добавлен: 09.11.2023
Просмотров: 450
Скачиваний: 2
СОДЕРЖАНИЕ
2.2 Производственная программа выпуска деталей. Тип производства
2.3 Анализ технологичности конструкции детали
2.4 Выбор и обоснование метода получения заготовки
2.5 Определение конструкторского и технологического кода детали
2.6 Разработка технологического процесса изготовления детали
3.1 Исходные данные для расчета
3.2 Расчет капитальных вложений
3.3 Расчет производственной площадки
3.4 Расчёт потребности в основных материалах и затрат на них
3.5 Расчет кол-ва промышленно – производственного персонала
3.5 Расчёт плановых фондов заработной платы (ФЗП)
3.6 Расчёт плановых фондов оплаты труда основных рабочих
3.7 Расчет себестоимости по статьям калькуляции единицы продукции
3.9 Технико-экономические показатели деятельности предприятия
4.1 Цели и задачи охраны труда
4.2 Положение о проведении обучения, инструктажей и обучение безопасным приемам труда
2.7 Контроль качества детали
В условиях производства с достаточно стабильным технологическим процессом может широко применяться статистический контроль. Статистический скользящий контроль на рабочих местах является формой контроля, обеспечивающей своевременное активное вмешательство в ход производства в случае начавшейся разладки станка.
Профилактика брака в условиях применения статистического активного контроля позволяет снизить процент брака при меньших затратах труда на технический контроль по сравнению со сплошным контролем продукции. Однако и такого рода статистический контроль является все же довольно трудоемким. Поэтому на многих машиностроительных заводах применяется выборочный контроль, не гарантирующий, однако, высокого качества выпускаемой продукции.
В связи с этим заслуживает внимания опыт ряда зарубежных машиностроительных заводов, применявших метод статистического стационарного контроля обработанных деталей. Детали, поступившие на такого рода контроль, рассыпаются ровным слоем на столе контролера, где нанесены квадратные деления (клетки). Для контроля берется определенное количество деталей из каждой клетки.
С учетом типа производства, точности размеров поверхности и его шероховатости был проведен анализ по выбору необходимых мерительных инструментов для всех обрабатываемых поверхностей, и приведена таблица.
2.7.1 Общие данные о контроле качества
Измерение – это нахождение физической величины опытным путем с помощью специальных физических средств.
Контроль состоит из нахождения физической величины и сравнения ее с допустимым значением.
Средство измерений – техническое средство, используемое при измерениях и имеющее нормированные метрологические свойства.
Измерения, при которых искомую величину находят непосредственно из опытных данных, называют прямыми. Если искомую величину находят на основании известной зависимости между этой величиной и величинами, полученными прямыми измерениями, то измерения называют косвенными. Точность косвенных измерений зависит от точности прямых измерений и точности используемой зависимости.
Погрешность измерений – отклонение результата измерения от действительного значения. При этом за действительное значение принимают значение измеряемой величины, определяемая погрешность измерения.
Результаты измерения признаются достоверными, если погрешность измерения не превышает установленной величины допустимой погрешности измерения.
2.7.2 Сведения об используемых средствах измерения
Для измерения и контроля обработанных поверхностей детали вал ведомый используют следующие средства измерения и контроля:
– Штангенциркуль ШЦЦ –II-320-1000-0,5;
– Штангенциркуль ШЦЦ-II-350-0,5;
– Угломер модель 1005 (мод.127);
– Калибр-кольцо для контроля прямобочных шлицевых соединений;
– Калибр-скоба Ø90k6
Расчет размеров калибр-скобы для вала Ø90 с полем допуска k6.
По ГОСТ 24853-81 предельные отклонения составляют +0,025 и +0,003 мм.
Следовательно:
dmax = 90,025мм;
dmin = 90.003 мм.
По ГОСТ 24853-81 допуски и другие данные для расчета калибров составляют:
H1 = 0,006 мм;
z1 = 0,005 мм;
y1 = 0,004 мм;
Hp = 0,0025 мм.
Расчет наименьшего размера проходной новой калибр-скобы:
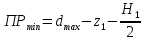
где




ПРmin = 90,025 – 0,005 –

Размер калибра ПР, проставляемый на чертеже, при допуске на изготовление равен 30,017+0,006. Исполнительные размеры: наименьший 90,017 мм; наибольший 90,023 мм.
Наибольший размер изношенной калибр-скобы при допуске на износ y
1=0,004 мм равен:
ПРmax = dmax + y1,(17)
где ПРmax – Наибольший размер изношенной калибр-скобы;
dmax– Наибольший предельный размер;
y1 – допустимый выход размера изношенного проходного калибра для вала за границу поля допуска изделия.
ПРmax = 90,025 + 0,004 = 90,029 мм.
Наименьший размер непроходной калибр-скобы рассчитывается по формуле:
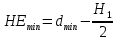
где



НЕmin = 90,003 –

Размер калибра НЕ, проставляемый на чертеже 90+0,006. Исполнительные размеры: наименьший 90 мм; наибольший 90,006 мм.
3 ЭКОНОМИЧЕСКИЙ РАЗДЕЛ
3.1 Исходные данные для расчета
Таблица 19 – Штучное время по операциям
Номер операции | Наименование операции | Штучное время Тшт, мин |
005 | Контрольная | – |
010 | Фрезерноцентровальная | 16,18 |
015 | Контрольная | – |
020 | Токарная | 66,6 |
025 | Контрольная | – |
030 | Шлицефрезерная | 31.25 |
035 | Контрольная | – |
040 | Шлифование (90) | 5,62 |
045 | Шлифование (шлицы) | 4,24 |
050 | Слесарная | 8,1 |
055 | Контрольная | – |
Общее штучное время: | 132 |
3.2 Расчет капитальных вложений
Капитальные вложения - это реальные инвестиции (вложения) в основной капитал (основные фонды), в том числе затраты на новое строительство, на расширение, реконструкцию и техническое перевооружение действующих предприятий, приобретение машин, оборудования, проектно-изыскательские работы и другие затраты, а также затраты на жилищное и культурно-бытовое строительство.
3.2.1. Расчёт потребного количества единиц оборудования
Потребное количество единиц оборудования определяется по формуле:
Срасч =
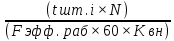
где Срасч – потребное количество единиц оборудования, шт;
tшт.i– норма штучного времени на конкретную операцию, мин;
Fэфф.раб – эффективный фонд времени работы единицы оборудования, мин;
N – годовая производственная программа выпуска деталей, шт/год;
Kвн – коэффициент выполнения нормы = 1;
Эффективный фонд рабочего времени рассчитывается по формуле:
Fэфф. обор =D × C × H × (1-

где Fэфф.раб– эффективный фонд времени работы единицы оборудования, час;
D – количество рабочих дней в году, шт;
С – количество смен, шт;
Н – длительность одной смены, час;
В - процент плановых потерь на переналадку и планово-предупредительный ремонт, %.
Fэфф. обор = 247 × 1 ×8 × (1-

Расчет потребного количества центровально-фрезерных станков модели МР-73:
Срасч =
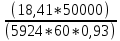
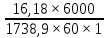
Расчет потребного количества токарных станков модели 16К20:
Срасч =
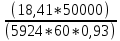
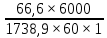
Расчет потребного количества шлицефрезерных станков модели 5А352П:
Срасч =
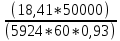
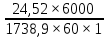
Расчет потребного количества шлицешлифовальных станков модели 3451 :
Срасч =
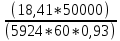
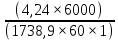
Расчет потребного количества круглошлифовальных станков модели 3132:
Срасч =
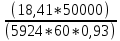
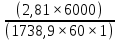
Расчет потребного количества верстаков:
Срасч =
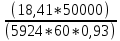
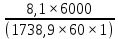
Принятое количество оборудования для всех токарных операций будет равняться 4. Для фрезерной операции количество оборудования равняется 3. Для шлифовальной операции количество оборудования будет равняться 2. Для слесарных и разметочных работ количество верстаков – 1.