Файл: Мордовского государственного университета им. Н. П. Огарёва.doc
ВУЗ: Не указан
Категория: Не указан
Дисциплина: Не указана
Добавлен: 11.12.2023
Просмотров: 195
Скачиваний: 1
ВНИМАНИЕ! Если данный файл нарушает Ваши авторские права, то обязательно сообщите нам.
Примечание. При наличии у детали других элементов (отверстий, шпоночных пазов, резьб и т.д.) их обработку необходимо производить в установленной технологической последовательности до термической обработки.
Технология изготовления деталей с зубчатым зацеплением.
Выбор схемы обработки зубчатого колеса должен производиться на основании тщательного анализа конструкции колеса и технических требований на его изготовление и возможностей конкретного производства. Обычно изготовление зубчатых колес производится в два этапа: первый этап – операции по обработке поверхностей зубчатого колеса до зубообразования, второй – операции по обработке и отделке зубьев (табл. 3.12, 3.13).
Таблица 3.12 - Технологическая схема изготовления детали «цилиндрическое зубчатое колесо»
Номер операции | Наименование и краткое содержание операции, технологические базы | Станок |
005 | Токарная Зенкерование (растачивание) центрального отверстия. Обтачивание поверхностей наружного контура и торца. Технологическая база – наружный диаметр венца колеса и второй торец. | Токарный многошпиндельный полуавтомат |
010 | Токарная Зенкерование (растачивание) центрального отверстия. Обтачивание поверхностей наружного контура. Технологическая база – наружный диаметр венца колеса и торец после обтачивания на первой операции. | Тоже |
015 | Протяжная Протягивание базового отверстия. Технологическая база – наружный диаметр венца и торец. | Протяжной |
020 | Токарная Обработка наружного контура колеса. Технологическая база – шлицевое | Токарный многорезцовый |
025 | Контрольная Промежуточный контроль. | |
030 | Зубофрезерная Фрезерование зубьев колеса. Технологическая база – шлицевое отверстие и торец. | Зубофрезерный полуавтомат |
035 | Зубозакругляющая (при необходимости). Закругление зубьев с другой стороны. Технологическая база – шлицевое отверстие и торец. | Зубозакругляющий |
040 | Зубозакругляющая. Закругление зубьев с другой стороны. Технологическая база – шлицевое отверстие и торец. | Тоже |
045 | Шевингование Шевингование зубьев колеса. Технологическая база – шлицевое отверстие и торец | Шевинговальный автомат |
050 | Моечная | |
Продолжение табл. 3.12
Номер операции | Наименование и краткое содержание операции, технологические базы | Станок |
055 | Контрольная | |
060 | Термическая | |
065 | Внутришлифовальная Шлифование базового отверстия. Технологическая база – эвольвента зубьев и торец. | Внутришлифовальный автомат |
070 | Моечная | |
075 | Контрольная | |
Таблица 3.13 - Технологическая схема изготовления детали «вал-шестерня»
Номер операции | Наименование и краткое содержание операции, технологические базы | Станок |
005 | Фрезерно-центровочная Фрезерование торцов и сверление центровочных отверстий с двух сторон. Технологическая база – наружные поверхности двух шеек и торец ступени зубчатого венца. | Фрезерно-центровальный |
010 | Токарная Черновое обтачивание поверхностей шеек с одной стороны и подрезание торцовых поверхностей ступеней вала. Технологическая база – центровые отверстия вала | Токарный многорезцовый или многошпиндельный полуавтомат |
015 | Токарная Черновое обтачивание поверхностей шеек вала с другой стороны, а также подрезка торцовых поверх-ностей вала с другой стороны. Технологическая база – центровые отверстия вала | То же |
020 | Токарная Чистовое обтачивание поверхностей шеек вала под шлифование и окончательная подрезка торцов ступеней вала. Технологическая база – центровые отверстия вала | Токарный многорезцовый, гидрокопировальный, многошпиндельный полуавтомат |
025 | Контроль промежуточный | |
030 | Зубофрезерная Фрезерование зубьев зубчатого колеса. Технологическая база – центровые отверстия. | Зубофреезерный |
035 | Зубозакругляющая Закругление зубьев с одной стороны венца. Технологическая база – центровые отверстия. | Зубозакругляющий |
040 | Зубозакругляющая Закругление зубьев с другой стороны венца. Технологическая база – центровые отверстия | То же |
45 | Термическая | |
050 | Зубошевенгование или зубошлифование | Шевинговальный |
055 | Моечная | |
060 | Контроль окончательный | |
3.3.4. Определение промежуточных припусков, допусков и размеров
Припуск – слой металла, удаляемый с поверхности заготовки в целях достижения заданных свойств обрабатываемой поверхности детали.
Припуск на обработку поверхностей детали может быть назначен по соответствующим справочным таблицам (статистический метод) или на основе расчетно-аналитического метода определения припусков [7].
При статистическом методе припуски назначаются независимо от технологического процесса обработки деталей и условии его осуществления и поэтому в общем случае являются завышенными.
Расчетно-аналитический метод определения припусков на обработку, разработанный проф. В.М. Кованом, базируется на анализе факторов, влияющих на припуски предшествующего и выполняемого переходов технологического процесса. Данный метод предусматривает расчет припусков по всем последовательно выполняемым технологическим переходам обработки данной поверхности детали (промежуточные припуски), их суммирование для определения общего припуска на обработку поверхности и расчет промежуточных размеров, определяющих положение поверхности, и размеров заготовки. Расчетной величиной является минимальный припуск на обработку, достаточный для устранения на выполняемом переходе погрешностей обработки и дефектов поверхностного слоя, полученных на предшествующем переходе, и компенсации погрешностей, возникающих на выполняемом переходе.
После расчета промежуточных размеров определяют допуски на эти размеры, соответствующие экономической точности данной операции. Промежуточные размеры и допуски на них определяют для каждой обрабатываемой поверхности детали.
Черновые операции рекомендуется выполнять с более низкими техническими требованиями на изготовление (12 – 14 квалитет), получистовые – на один-два квалитета ниже и окончательные операции выполняются по требованиям рабочего чертежа детали.
Шероховатость обрабатываемых поверхностей зависит от степени точности и назначается по справочным таблицам 5 – 7 (приложения А).
При выполнение курсовой работы на 1-2 поверхности, заданные руководителем, производится определение припусков расчетно-аналитическим методом, для остальных поверхностей определяются статистическим методом.
3.3.5. Расчетно-аналитический метод определения припусков
Минимальный односторонний припуск определяется зависимостью:

двусторонний припуск

где
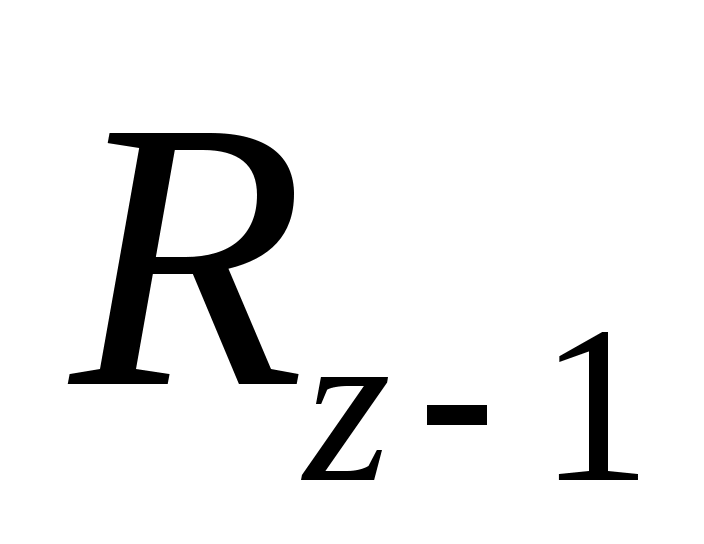
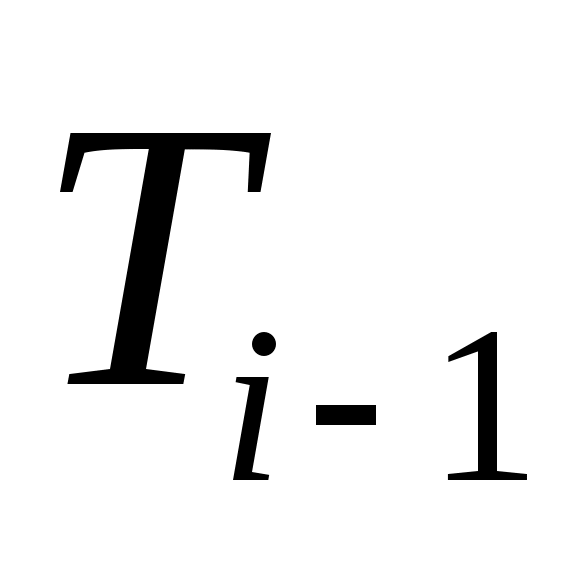
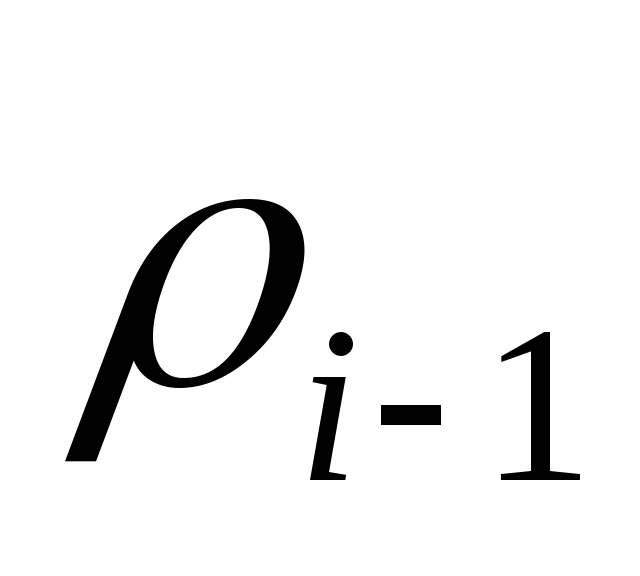
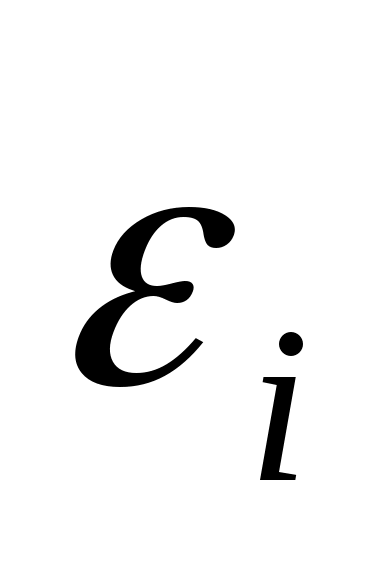
Максимальный припуск на обработку поверхности заготовки:
- для плоских поверхностей

- для поверхностей типа тел вращения

где
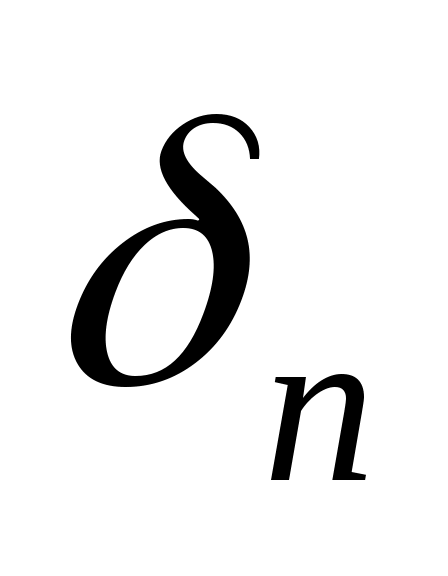
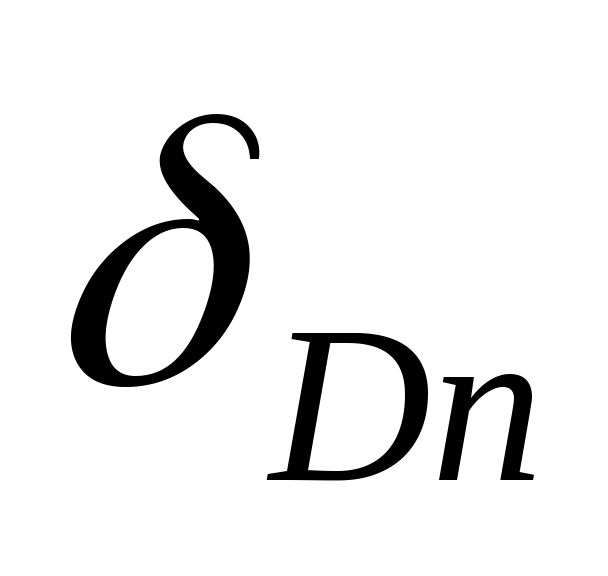
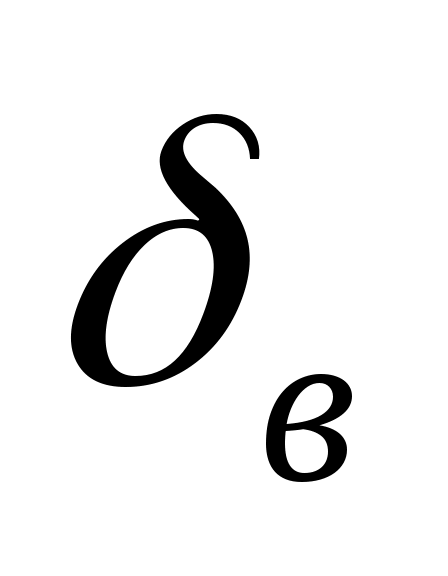
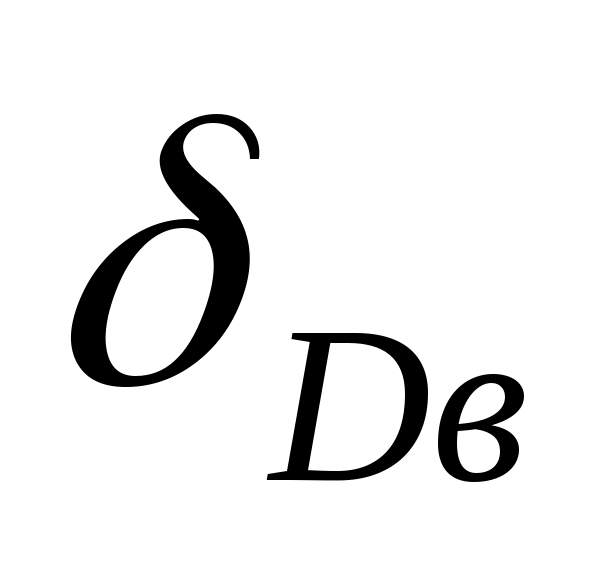
Допуски и шероховатость поверхности на окончательных технологических переходах (операциях) принимают по рабочему чертежу.
Для удобства определения промежуточных припусков перед их расчетом исходные и расчетные данные по каждой операции на конкретную обрабатываемую поверхность в технологической последовательности заносят в таблицу 3.14.
Таблицу рекомендуется заполнять в такой последовательности:
- в графу «Вид заготовки и технологическая операция» записывают вид заготовки и операции, установленные на данную обрабатываемую поверхность в технологической последовательности;
- в графу «Точность заготовки и обрабатываемой поверхности» записывают степень точности выбранной заготовки и квалитета на промежуточные размеры без предельных отклонений
;
- в графу «Элементы припуска» заносят величину микронеровностей и глубину дефектного поверхностного слоя на заготовку и на все операции в технологической последовательности в зависимости от метода обработки, а величину погрешностей установки заготовки на выполняемой операции определяют по таблице или производят расчет по формулам;
- графу «Допуски на размер» заполняют значениями допусков на заготовку и промежуточные размеры согласно степени точности заготовки и квалитета установленных на размер по каждой операции.
Остальные значения промежуточных припусков и размеров заносят в таблицу после расчетов.
Таблица 3.14 - Расчет припусков и промежуточных размеров по технологическим операциям (пример)
Вид заготовки и технологичес-кая операция | Точность заготовки и обрабаты-ваемой поверхности | Допуски на размер, мм | Элементы припуска, мкм | Промежуточные размеры заготовки, мм | Промежуточ-ные припуски, мм | |||||
Rz | T | ![]() | ![]() | Dmax | Dmin | Zmax | Zmin | |||
Прокат | | | | | | | | | | |
Мехобработка | | | | | | | | | | |
Термообработка | | | | | | | | | | |
Шлифовальная | | | | | | | | | | |