Файл: И. И. Лаптева, М. А. Колесников неразрушающий контроль деталей вагонов рекомендовано Методическим советом двгупс в качестве учебного пособия Хабаровск Издательство двгупс 2012.docx
ВУЗ: Не указан
Категория: Не указан
Дисциплина: Не указана
Добавлен: 11.01.2024
Просмотров: 656
Скачиваний: 6
СОДЕРЖАНИЕ
1. ВИДЫ И МЕТОДЫ НЕРАЗРУШАЮЩЕГО КОНТРОЛЯ
2.1. Феррозондовый метод контроля:основные понятия и технология
2.2. Технология контроля деталей рамы тележки грузового вагона модели 18-100 (18-493)
2.4. Магнитопорошковый контроль
3. ВИХРЕТОКОВЫЙ МЕТОД КОНТРОЛЯ
4. ДЕФЕКТОСКОПИЯ ПРОНИКАЮЩИМИ ЖИДКОСТЯМИ
5. УЛЬТРАЗВУКОВАЯ ДЕФЕКТОСКОПИЯ
5.2. Факторы, влияющие на эффективность УЗД
5.4. Принципиальное устройство ультразвукового дефектоскопа
5.5. Способы ввода ультразвука в деталь
5.6. Методы ультразвукового контроля
5.7. Средства настройки дефектоскопа
5.8. Контроль оси на прозвучиваемость (УД2-12)
5.10. Ультразвуковая дефектоскопия колёс
6. АКУСТИКО-ЭМИССИОННЫЙ МЕТОД КОНТРОЛЯ
7. Интроскопический метод контроля
Тестовые задания по дисциплине «Основы технической диагностики»
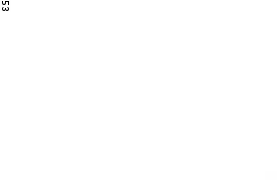
Примечание. * Для тележки КВЗ-5 не выполняется.
Технологический процесс вихретоковой дефектоскопии выполняют в следующем порядке:
-
Подготовка дефектоскопа, его настройка с помощью стандартного образца на определенный уровень чувствительности. -
Подготовка детали (очистка, осмотр, отбраковка негодных). -
Сканирование зон контроля детали. Вертикальная ось ВТП должна располагаться перпендикулярно контролируемой поверхности. Отклонение допускается до 30°. Скорость сканирования не более 10 см/с. -
На подозрительных местах выполняется более тщательный контроль.

4. ДЕФЕКТОСКОПИЯ ПРОНИКАЮЩИМИ ЖИДКОСТЯМИ
Различные жидкости (керосин, дизельное топливо и др.) имеют различную проникающую способность, т. е. способность заполнять полости дефектов, открытых с поверхности.
Технологический процесс осуществляется в следующем порядке.
-
Очистка поверхностей, подлежащих контролю. -
Нанесение на поверхность проникающей жидкости (смачивание). -
Удаление излишка проникающей жидкости протиркой ветошью. -
Нанесение проявителя (порошки – мел, тальк, суспензии – раствор извести). -
Выдержка во времени и осмотр.
Если на поверхности детали была трещина, то проявитель впитает в себя проникающую жидкость, находящуюся в дефекте и изменит свой цвет.
Промышленностью производятся проникающие жидкости марки К (красного цвета) и проявитель марки М (белого цвета). Область применения 50 °С.
Классификация капиллярных методов контроля основана на светоколорических особенностях индикаторных следов. По этому признаку они подразделяются на три основных метода: цветной, люминесцентный и люминесцентно-цветной.
Люминесцентный метод основан на способности некоторых веществ (керосин, ЛЮМАГПОР-5) проникать в поверхностные дефекты и светиться после облучения УФ-лучами в затемненном помещении.
При цветном методе дефекты выявляются по цветному индикаторному следу над дефектом, так как краситель, входящий в состав проникающей жидкости, обладает избирательным отражением части видимого света.
Люминесцентно-цветной метод является комбинацией цветного и люминесцентного методов.
Чувствительность методов определяют по размеру наименьших выявляемых реальных и искусственно-инициированных дефектов (ширина раскрытия, глубина, длина полости), которые устанавливают пять классов (табл. 8).
Таблица 8
Классы чувствительности
Класс чувствительности | 1 | 2 | 3 | 4 | Технологический |
Ширина раскрытия, мкм | Менее 1 | От 1 до 10 | От 10 до 100 | От 100 до 500 | Не нормируется |
Не следует стремиться к более высоким классам, так как это требует более дорогостоящих материалов, увеличивает время контроля.
В вагонном хозяйстве методы контроля проникающими веществами применяют для контроля гребней колес после их наплавки и обточки, котлов цистерн и элементов тормозной системы, запасных резервуаров автотормозов, котлов водяного и парового отопления.

5. УЛЬТРАЗВУКОВАЯ ДЕФЕКТОСКОПИЯ
5.1. Общие положения
В зависимости от частоты колебаний различают колебания низкой частоты (менее 16 Гц) – инфразвук, звуковые колебания (16–20000 Гц), колебания высокой частоты (более 20000 Гц) – ультразвук (УЗ).
В ультразвуковой дефектоскопии (УЗД) используется частота от 0,5 до 10 МГц.
При распространении УЗ-волн в среде различают два явления:
1) направленность распространения волн в среде;
2) колебания частиц среды относительно своего положения равновесия.
В зависимости от направленности распространения УЗ-волны подразделяются:
-
на продольные – направление смещения частиц вещества совпадает с направлением распространения волн. Продольные волны могут возбуждаться в твердой, жидкой и газообразной среде; -
поперечные – направление смещения колеблющихся частиц А происходит перпендикулярно направлению волны. Такие волны могут возбуждаться только в твердых средах. Продольные и поперечные волны в твердых средах распространяются прямолинейно;
-
поверхностные – распространяются по поверхности твердых тел на глубину до двух длин волн. Могут распространяться по криволинейной поверхности. В газообразных и жидких средах не возбуждаются.
Скорость распространения УЗ-волны
С = f, (8)
где – длина волны; f – частота колебаний, Гц.
Скорости распространения УЗ-волн в различных средах приведены в табл. 9.
Длина волны влияет на чувствительность ультразвуковой дефектоскопии. Чувствительность – минимальные размеры дефекта, которые можно обнаружить. Если дефект меньше длины волны, то волна огибает этот дефект, и он не может быть обнаружен.
Таблица 9
Скорости распространения волн
Вещество | Скорость продольной волны, м/с | Скорость поперечной волны, м/с | Скорость поверхностной волны, м/с |
Сталь Ст3 | 5930 | 3270 | 3041 |
Алюминий | 6200 | 3080 | 2800 |
Вода | 1497 | – | – |
Трансформаторное масло | 1390 | – | – |
УЗ-волны характеризуются количеством энергии, переносимой за 1 секунду через 1 см2 площади, перпендикулярной к направлению распространения этой волны – это интенсивность I:
, (9)
где U – амплитуда смещения частиц среды в волне; – плотность
среды.
По мере распространения волны интенсивность уменьшается. Чем крупнее структура материала детали, тем больше величина рассеивания энергии. На этом принципе основан контроль осей на прозвучиваемость (выявление крупнозернистой структуры).
УЗД основана на использовании физических явлений прямого и обратного пьезоэффекта.
Прямой пьезоэффект заключается в том, что если пьезопластину, вырезанную, например, из кристалла кварца, подвергнуть сжатию, то на ее гранях возникнут электрические заряды. Возникший потенциал используется для определения места распространения и величины дефекта.
Обратный пьезоэффект – если к граням пьезопластины подвести переменное напряжение, то пьезопластина с определенной частотой начнет колебаться. Эти механические колебания и используются для ввода ультразвука в деталь.
5.2. Факторы, влияющие на эффективность УЗД
Распространение УЗ-волн в среде сопровождается потерей энергии. Эти потери увеличиваются:
1) с ростом частоты ультразвука;
2) увеличением температуры детали (ослабляются её упругие свойства, увеличивается пластичность);
3) увеличением зернистости материала детали, особенно если средний диаметр зерен материала изделия больше длины УЗ-волн, происходит отражение их от граней кристаллов;
4) если размеры шероховатости поверхности, через которую вводится ультразвук, соизмеримы с длиной волны (увеличивается отражение и преломление УЗ-волны);
5) при наличии на поверхности детали ржавчины и отслоившейся окалины (необходимо их удаление. Наиболее эффективный способ – дробеструйная очистка).
5.3. Технические средства УЗД
При УЗД колесных пар применяются следующие технические средства:
-
УЗ-дефектоскопы УД-12, УДС-2-32; УДС-1-22; Поиск 24; -
УЗ-пьезоэлектрические преобразователи (ПЭП); -
регистратор результатов ультразвукового контроля колёс УР-1; -
регистратор результатов ультразвукового контроля осей УР-2; -
устройство сканирования для колес УСК-3; -
контрольные оси КО РУ-1, КО РУ-1Ш; -
контрольные образцы.
5.4. Принципиальное устройство
ультразвукового дефектоскопа
5.4.1. Общие сведения
Дефектоскопы предназначены для ультразвукового контроля узлов и деталей технических средств железнодорожного транспорта (осей вагонных и локомотивных колесных пар, ободьев, дисков, гребней цельнокатаных колес, сварных соединений) с целью выявления дефектов. Принципиальная схема дефектоскопа приведена на рис. 36.
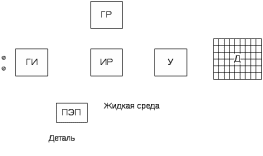
Рис. 36. Схема ультразвукового дефектоскопа
На рис. 36 следующие обозначения:
ГИ – генератор импульсов – для получения высокочастотных электрических колебаний и их подачи на ГР, ИР и ПЭП;
ГР – генератор развертки, служит для развертки электронного луча на экране ЭЛТ;
ИР – индикатор расхождения – для выявления в определенном масштабе места расположения дефекта на экране ЭЛТ