Файл: Геологическая характеристика костомукшского месторождения.docx
ВУЗ: Не указан
Категория: Не указан
Дисциплина: Не указана
Добавлен: 22.11.2023
Просмотров: 885
Скачиваний: 4
СОДЕРЖАНИЕ
ГЕОЛОГИЧЕСКАЯ ХАРАКТЕРИСТИКА КОСТОМУКШСКОГО МЕСТОРОЖДЕНИЯ
1.1. Краткая характеристика района
1.4. Гидрогеологическая характеристика месторождения
1.5. Инженерно-геологическая характеристика месторождения
1.6. Попутные полезные ископаемые и компоненты
2.1. Современное состояние и перспектива развития горных работ
2.2. Текущий и перспективный планы горных работ
2.3. Производительность и режим работы
2.4. Вскрытие и система разработки карьера
2.4.1. Расчет ширины рабочей площадки
2.5. Подготовка горных пород к выемке
2.5.2. Требования к буровзрывным работам
2.5.3.2. Выбор способа бурения и бурового оборудования
2.5.3.3. Расчёт производительности и количества буровых станков
2.5.4. Расчет параметров скважинных зарядов
2.5.4.3. Расстояние между скважинами в ряду
2.5.4.4. Требования к крупности дробления
2.5.4.5 Способ взрывания и параметры короткозамедленного взрывания
2.5.4.6. Тип и удельный расход ВВ
2.6. Выемочно-погрузочные работы
2.6.1. Погрузка взорванной скальной горной массы в карьере
2.6.2. Расчет параметров забоя
2.6.3. Расчет производительности и технического парка экскаваторов для вскрышных работ
2.6.4. Расчет производительности и технического парка экскаваторов для добычных работ
2.6.5. Общее количество экскаваторов
2.7. Технологический транспорт
2.7.1. Автомобильный транспорт
2.7.1.1. Расчет автомобильного транспорта для вскрышных пород
2.7.1.2. Расчет автомобильного транспорта для руды
2.7.2. Железнодорожный транспорт
2.8. Назначение и структурная схема рудо-контрольных станций
2.8.1. Схема работы программы управления грузопотоком руды в карьере
2.11.1. Расчет водоотливной установки
3. ПЕРЕРАБОТКА ПОЛЕЗНОГО ИСКОПАЕМОГО
4.1. Задача диспетчеризации на горном предприятии
4.2. Назначение и цели внедрения системы управления
4.3. Анализ существующих систем
4.4. Общие сведенья о системе Dispatch
4.5.Техническая характеристика БелАЗ-75131
4.8 ЭКСПЛУАТАЦИОННЫЕ РАСЧЕТЫ ПРОЕКТНОГО ВАРИАНТА
5. ДОПОЛНИТЕЛЬНЫЕ РАЗДЕЛЫ ДИПЛОМНОГО ПРОЕКТА
5.2. Электроснабжение участка карьера
5.4. Техника безопасности, противопожарная профилактика, аэрология карьера
6.1. Обоснование эффективности внедрения
3. ПЕРЕРАБОТКА ПОЛЕЗНОГО ИСКОПАЕМОГО
Рудная масса из внутрикарьерных перегрузочных пунктов грузится в железнодорожный транспорт и доставляется в приёмный бункер в корпусе крупного дробления обогатительной фабрики. Размер максимального куска не более 1200 мм, содержание Fe в руде не менее 24%.
Дробление ведется в три стадии:
1 – дробилками ККД-1500-180 до крупности 350-0мм;
2 – дробилками КСД-3000Т с грохочением на грохотах ГИТ-71Н с крупностью после дробления 100-0мм;
3 – дробилками КМД-3000Т, работающими в замкнутом цикле и грохотами ГИТ-71Н с крупностью после дробления 18-0мм.
Технологическая схема переработки и обогащения представлена на схеме 1.
Компоновка технологического оборудования корпуса крупного дробления позволяет с помощью четырех пластинчатых питателей подавать дробленую руду из двух дробилок ККД-1500/180 на любой из двух ленточных конвейеров и таким образом непрерывно обеспечивать рудой корпус среднего и мелкого дробления. Благодаря применению высокопроизводительных дробилок КСД-3000Т и КМД-3000Т при трех стадиальной схеме дробления на крупной дробильной фабрике по переработке железной руды получена в замкнутом цикле дробления конечная крупность материала -18 мм.
Технологическая схема обогащения состоит из трех стадий измельчения, трех стадий мокрой магнитной сепарации, четырех стадий классификации, тонкого грохочения и трех стадий дешламации.
К основному технологическому оборудованию относятся стержневые мельницы МСЦ-3850-5500, шаровые мельницы МШЦ-4500-6000, магнитные сепараторы ПБМ-ПП-90/250, гидроциклоны ГЦ-710 и ГЦ-500, магнитные дешламаторы МД-9, сгустители диаметром 30м, грохоты тонкого грохочения нового поколения Derik.
Хвосты магнитной сепарации и сливы дешламаторов попадают в пульпонасосную, откуда с помощью грунтовых насосов ГРТ-8000-71 по пульповодам диаметром 1200мм перекачиваются в хвостохранилище. Емкость хранилища – 410 млн. куб. м, площадь 25 кв.км.
Концентрат направляется в корпус сгущения, где на радиальных сгустителях диаметром 30м сгущается до плотности 50% твердого и подается в корпус окомкования.
Технологическая цепь фабрики по производству окатышей разделяется на три стадии: фильтрация, окомкования и обжиг.
Концентрат поступает в два перемешивателя типа МП-3,15. После фильтрации кек подается в отделение бункерования и дозирования, где дозируется известняком и бентонитом в заданном соотношении.
Окомкование шихты осуществляется в барабанных окомкователях 3,6x10, работающих в замкнутом цикле с грохотами типа ГСТ-71 СОК.
Готовые по крупности окатыши класса +8мм подаются на обжиговую машину ОК-520-536, где они последовательно проходят зоны сушки, подогрева, обжига, рекуперации и охлаждения. Максимальная температура обжига 1350о С.
Высокотемпературный окислительный обжиг позволяет на 90-95% удалить серу из окатышей и получит их высокую прочность.
Обожженные окатыши сортируются по классу крупности +5мм. Мелочь направляется в силосный склад, откуда отгружается потребителям на агломерацию.
Готовый продукт – офлюсованные и неофлюсованные окатыши, отправляются на склад или на погрузочные бункера для отправки их на металлургические заводы.
Годовая переработка руды составляет 24 млн.т, производство коцентрата 9,3 млн.т в год, производство окатышей 8,84 млн.т в год.
Т
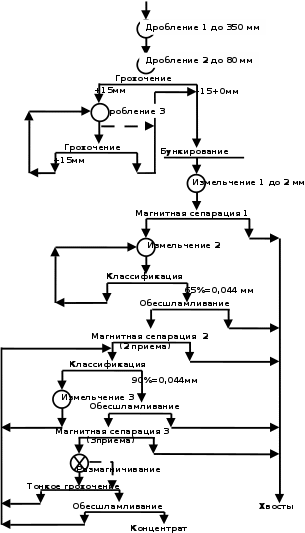
4. СПЕЦИАЛЬНАЯ ЧАСТЬ
Опыт внедрения автоматизированной системы управления
горнотранспортным комплексом.
Система диспетчеризации «Dispatch», разработанная компанией «Modular Mining Systems»
4.1. Задача диспетчеризации на горном предприятии
Диспетчеризация горного производства (от англ. Dispatch - отправлять по назначению, быстро выполнять) — централизация оперативного контроля и координация управления производственными процессами с целью обеспечения согласованной работы звеньев одного или группы предприятий для достижения оптимальных технико-экономических показателей, выполнения трафиков работ и производственной программы.
Основные функции диспетчеризации:
-
контроль и управление технологическими процессами; -
контроль и оперативное распределение материальных и энергетических ресурсов, транспортных средств; -
учёт работы машин и механизмов и др.
В силу специфичности технологического процесса, территориальной разбросанности отдельных участков работ на горнодобывающих предприятиях решающее значение приобретает оперативное управление деятельностью отдельных участков и предприятия в целом.
При этом диспетчеризация обеспечивает равномерную загрузку всех звеньев предприятия, непрерывность, ритмичность и экономичность выполнения всех процессов основного производственного цикла, бесперебойность работы вспомогательных и обслуживающих участков.
Диспетчеризация позволяет регулировать процесс производства, ритм которого нарушается вследствие изменения состава добываемого сырья, производимой продукции, корректив, вносимых в методы и технологию добычи сырья, изготовления продукции, разного уровня выполнения производственных программ участками предприятия, перебоев, связанных с ремонтом оборудования, нарушением графика поставки материалов и т.п.
Диспетчеризация является необходимым средством оперативного руководства сложным комплексом технологических процессов и транспортных систем.
Исходя из того, что на предприятии ОАО «Карельский Окатыш» большегрузные автосамосвалы полностью зарекомендовали себя как самый удобный и маневренный способ для вывозки горной массы, было принято решение автоматизировать систему управления горно-транспортным комплексом за счёт внедрения системы диспетчеризации «Dispatch» компании «Modular Mining Systems».
4.2. Назначение и цели внедрения системы управления
Автоматизированная система управления горнотранспортным комплексом предназначена для:
-
управления выемочно-погрузочным и автомобильным транспортом, -
контроля и управления объемом и качеством руды, -
мониторинга управления эксплуатацией оборудования, -
сбора статистических данных.
Основными целями создания системы являются:
-
повышение эффективности использования оборудования горнотранспортного комплекса и увеличение его производительности; -
обеспечение экономии ресурсов при достижении необходимых объемов производства; -
снижения расходов топлива, шин, оптимизация загрузки транспортных средств, -
повышение трудовой и технологической дисциплины; -
организация планового ремонта и обслуживания транспортного оборудования.
4.3. Анализ существующих систем
На выбор предлагается множество систем предназначенных для оптимизации работы горнотранспортного комплекса, но учитывая требования к нововведению на выбор предложено несколько систем удовлетворяющие цели и задачи, поставленные перед выбором для решения ряда проблем данного предприятия.
1) Система «Карат» разработана Центральным научно-исследовательским институтом комплексной автоматизации (ЦНИИКА) и предназначена для решения следующих задач горного производства:
-
Оперативного планирования объёмов добычи руды экскаваторами в режиме усреднения её качества; -
Оптимального планирования транспортных средств и распределения их по пунктам погрузки разгрузки;
• Сбора первичной информации, её обработки и выдачи результатов расчёта оперативных показателей работы экскаваторно-автомобильного комплекса для анализа, выработки решений и планирования работы на следующие смены.
Система осуществляет ряд функций по управлению и контролю технологических процессов в карьере:
-
Распределение потока технологического транспорта по пунктам погрузки для выполнения сменного плана горных работ и обеспечения требуемого содержания полезного компонента в рудах, поставляемых на обогатительную фабрику; -
Выбор пункта погрузки и маршрута следования каждого автосамосвала с целью уменьшения суммарных простоев погрузочного и транспортного оборудования; -
Учёт работы экскаваторов и автосамосвалов; -
Учёт объёмов горной массы по пунктам разгрузки и со всего карьер в целом.
Система позволяет опознавать номера автосамосвалов на контрольных пунктах, взвешивать их по ходу, информировать о перевозимом объёме горной массы водителей автосамосвалов и оператора, контролировать автосамосвал при сходе с линии. При резких изменениях производственной ситуации (например, выход из строя экскаваторов, перегрузочных пунктов, обогатительных фабрик, изменения содержания руды в забоях и т.д.) производится перезакрепление автосамосвалов. В системе «Карат» указанные процессы осуществляются автоматически с помощью ЭВМ, без вмешательства диспетчера. Такая система была внедрена на карьере «Мир».
Система «Карат-М» отличилась модернизацией, её основная функция состоит в оперативном управлении изменением потока транспортных единиц. В результате диспетчер получает возможность непосредственно воздействовать не только на отдельные автосамосвалы, но и через них на экскаваторы, а тем самым - на качественные и количественные параметры исходящего потока руды, на скорость подвигания добычных и вскрышных забоев.
«Карат-М» отличается от системы «Карат» тем, что система работает в так называемом «диалоговом режиме», причём информация о состоянии экскаваторов, а также положении на пунктах разгрузки передаётся машинистами и операторами непосредственно на пункт управления диспетчеру по радио или телефонной связи.
Внедрение такой системы позволило снизить простои автотранспорта в ожидании погрузки в среднем на 15-20 %, простои экскаватора в ожидании транспорта на 20 %, повысить однородность качества руды, поступающей на обогатительную фабрику, увеличить коэффициент использовании грузоподъёмности автотранспорта на 17%, а также повысить культуру производства.
В то же время «Карат-М» и аналогичные ей системы не позволяли осуществлять контроль над многими важными эксплуатационными характеристиками работы автосамосвалами, что приводило к завышенным затратам на горюче-смазочные материалы (ГСМ), автомобильные шины, ремонты и техническое обслуживание. В настоящее время из-за устаревшей базы системы такого типа не используются.
2) Среди отечественных производителей более совершенными системами, прошедшими опытно-промышленную эксплуатацию, являются «Комплекс-АТ» и «Гермес», относящиеся к классу информационно-управляющих систем, которые реализуют как информационно-вычислительные функции, так и управляющие и вычислительные.