Файл: И. И. Лаптева, М. А. Колесников неразрушающий контроль деталей вагонов рекомендовано Методическим советом двгупс в качестве учебного пособия Хабаровск Издательство двгупс 2012.docx
ВУЗ: Не указан
Категория: Не указан
Дисциплина: Не указана
Добавлен: 11.01.2024
Просмотров: 650
Скачиваний: 6
СОДЕРЖАНИЕ
1. ВИДЫ И МЕТОДЫ НЕРАЗРУШАЮЩЕГО КОНТРОЛЯ
2.1. Феррозондовый метод контроля:основные понятия и технология
2.2. Технология контроля деталей рамы тележки грузового вагона модели 18-100 (18-493)
2.4. Магнитопорошковый контроль
3. ВИХРЕТОКОВЫЙ МЕТОД КОНТРОЛЯ
4. ДЕФЕКТОСКОПИЯ ПРОНИКАЮЩИМИ ЖИДКОСТЯМИ
5. УЛЬТРАЗВУКОВАЯ ДЕФЕКТОСКОПИЯ
5.2. Факторы, влияющие на эффективность УЗД
5.4. Принципиальное устройство ультразвукового дефектоскопа
5.5. Способы ввода ультразвука в деталь
5.6. Методы ультразвукового контроля
5.7. Средства настройки дефектоскопа
5.8. Контроль оси на прозвучиваемость (УД2-12)
5.10. Ультразвуковая дефектоскопия колёс
6. АКУСТИКО-ЭМИССИОННЫЙ МЕТОД КОНТРОЛЯ
7. Интроскопический метод контроля
Тестовые задания по дисциплине «Основы технической диагностики»
Проверку качества магнитных индикаторов с помощью стандартных образцов предприятия выполняют по способности выявления искусственно созданных в них дефектов (табл. 6).
Таблица 6
Типы стандартных образцов
предприятия с искусственными дефектами
Наименование СОП | Номер типа СОП; регистрационный номер | Направление искусственных дефектов на детали |
Внутреннее кольцо подшипника | СОП МП 32.01.000-01, МТ 036.2001 | Поперечные и продольные |
Наружное кольцо подшипника | СОП МП 32.02.000-01, МТ 037.2001 | То же |
Ролик | СОП МП 32.03.000-01, МТ 038.2001 | » |
Стопорная планка | СОП МП 32.05.000-01, МТ 040.2001 | Поперечные |
Фрагмент оси колесной пары (шейка, средняя и подступичная части) | СОП МП 32.04.000-01, МТ 039.2001 | Поперечные (при применении СОП в составе оси колесной пары в сборе). Поперечные и продольные (при применении СОП в составе свободной оси) |
Пластина | СОП МП 32.07.000-01 МТ 042.2001 | Поперечные |
Валик | СОП МП 32.08.000-01 МТ 043.2001 | То же |
Зубчатое колесо (венец) | СОП МП 32.06.018-01 | Вдоль межзубных впадин |
Шестерня | СОП МП 32.06.018-01 | То же |
Для этого СОП намагничивают с помощью штатного дефектоскопа, используемого для намагничивания контролируемой детали, до значения напряженности магнитного поля, указанного в паспорте на СОП. На очищенную и обезжиренную рабочую поверхность СОП наносят магнитный индикатор. Получаемый индикаторный рисунок сравнивают с дефектограммой, показанной в паспорте на СОП.
Магнитный порошок считают годным, если полученный индикаторный рисунок по виду и длине совпадает с индикаторным рисунком дефектограммы.
В этом контексте отметим не менее важное функциональное назначение стандартных образцов предприятия, а именно: проверку технологии и оценку чувствительности МПК объектов конкретного типа с учетом особенностей их геометрии и (или) свойств материала, а
также влияния режимов намагничивания, квалификации персонала НК, выбора средств НК и т. д. Для этого СОП выполняют в виде цельного образца объекта контроля или его фрагмента с нормированными или искусственными дефектами.
В настоящее время на ремонтных предприятиях железнодорожного транспорта для настройки дефектоскопов и проверки технологии контроля различными методами конкретных объектов на рабочих местах широко используют так называемые контрольные (испытательные) образцы, которые, по существу, являются СОП. Указанные образцы изготавливают или отбирают (для магнитопорошкового контроля). Поскольку в отрасли отсутствуют нормативные документы, устанавливающие порядок разработки и аттестации СОП, то единственным критерием отбора СОП с естественным дефектом является признак: дефект не выявляется при осмотре образца невооруженным глазом.
На СОП с естественными и искусственными дефектами обязательно изготавливается дефектограмма и размещается на рабочем столе. Дефектограмма представляет собой отпечаток индикаторного рисунка дефекта и выполняется путем фотографирования, с помощью липкой ленты, с применением клеевой суспензии. Наиболее распространенным является изготовление дефектограммы с помощью липкой ленты. Деталь намагничивают, образуя валик дефекта, если он обнаружен. При МПК с применением «сухого» способа нанесения порошка липкую ленту накладывают на валик дефекта и снимают отпечаток дефекта. Если контроль проводится с помощью суспензии, то ожидают ее высыхания. Полученную дефектограмму помещают между пластинками оргстекла. При использовании СОП с естественными дефектами наличие дефектограммы на рабочем месте обязательно.
2.4.3. Осмотр деталей
При осмотре детали обнаруживают и анализируют осаждение магнитного индикатора с целью определения характера дефекта и принятия решения о пригодности детали к дальнейшей эксплуатации. Индикаторный рисунок из осевшего порошка на дефектах различного происхождения неодинаков. Его размеры и форма зависят от характера, величины и глубины залегания дефектов, что иногда дает возможность по форме индикаторного рисунка установить происхождение дефекта. Для облегчения расшифровки индикаторных рисунков на рабочих местах изготавливают и вывешивают дефектограммы характерных дефектов, в том числе и мнимых, выявленных при контроле конкретных деталей.
Основные требования к операции осмотра деталей:
-
осмотр детали проводят при комбинированном освещении: общем и местном, при этом освещенность контролируемой поверхности должна быть не менее 1000 лк, для местного освещения применяют переносные светильники с непрозрачным отражателем, обеспечивающим рассеяние света и защиту глаз дефектоскописта от слепящего воздействия источника света; -
не допускается попадания прямых солнечных лучей света в глаза; -
при осмотре деталей необходимо применять лупы пяти- – семикратного увеличения; -
при контроле магнитной суспензией осмотр необходимо начинать через 20–30 с после нанесения индикатора для обеспечения формирования валика порошка.
Если ставится задача обнаружить дефекты малого размера, то размеры неровностей поверхности не должны превышать ожидаемых размеров дефекта. Наивысшая чувствительность МПК достигается при чистоте обработки поверхности, соответствующей 6–7-му классу шероховатости поверхности [1]. Очевидно, что увеличение шероховатости приводит к снижению чувствительности. В этом случае выявление дефектов с раскрытием 2–3 мкм оказывается невозможным уже при 5-м классе обработки. Казалось бы, на более чистой поверхности выявлять дефекты легче, однако здесь вступает в силу фактор бликов, из-за которых шлифованные поверхности, начиная с 9-го класса, трудно осматривать. Поэтому такие поверхности рекомендуется [1] осматривать в рассеянном свете или покрывать очень тонким слоем краски.
2.4.4. Расшифровка индикаторных рисунков дефекта
рассмотрим особенности дефектов, которые необходимо учитывать при расшифровке магнитных индикаций.
Трещины усталости возникают в процессе эксплуатации и обнаруживаются, как правило, в деталях, испытывающих в работе многократные знакопеременные нагрузки. Причинами их появления могут быть конструктивные недостатки, например, наличие концентраторов напряжений – резких переходов в сечениях, несоблюдение требований чертежа при производстве или ремонте (надрезы или глубокие риски), наличие на детали дефектов металлургического происхождения (волосовин, шлаковых включений, флокенов), возникновение дефектов при обработке детали (шлифовочных, ковочных, закалочных и сварочных трещин).
Трещины усталости являются чрезвычайно опасными, так как, возникнув, они постепенно развиваются и углубляются внутрь детали по ее сечению, пока ослабление последнего не приведет к завершающему хрупкому разрушению детали.
Трещины усталости независимо от их происхождения выявляются по резко очерченному, плотному, четкому валику порошка, формирующемуся по всей длине трещины.
дефекты сварки. Сварка является одним из самых распространенных технологических процессов в различных отраслях промышленности. В настоящее время применяют более ста видов сварки, которые по виду вводимой энергии делят на термические, термомеханические, механические.
Т
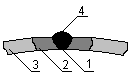
Рис. 27. образование
сварного шва
ермические виды сварки включают в себя все способы сварки плавлением, осуществляемые без приложения давления. Термомеханические и механические способы сварки осуществляют только с приложением давления.
Соединение, выполненное сваркой плавлением (рис. 27), содержит шов 1, зону термического влияния 2, основной материал 3, в котором при сварке не происходит никаких структурных изменений, и валик усиления 4. Зона термического влияния начинается непосредственно у шва, где металл имеет твердо-жидкое состояние, и заканчивается участком основного металла, где температура составляет 100–500 °С.
Характерные причины возникновения трещин в сварных швах:
-
«горячие» (кристаллизационные) трещины зарождаются в процессе первичной кристаллизации или после охлаждения до 1100–1200 °С, возникают в переходной зоне от шва к основному металлу, форма таких трещин – извилистые, могут быть сквозными и несквозными, причина их возникновения – несоблюдение технологии сварки; -
«холодные» трещины возникают при остывании металла ниже 200 °С в околошовной зоне и в металле шва и развиваются вдоль или поперек шва, могут быть поверхностными или внутренними, возникают через несколько часов или суток после сварки, причина их появления – неправильно выбранный присадочный материал или несоблюдение технологии сварки; -
мелкие трещины (микротрещины) в шве или надрывы в переходной зоне появляются из-за неудовлетворительного качества присадочного материала; -
непровар – отсутствие структурной связи между объемами металла в сварном шве (по кромкам, сечению и в корне шва) – появляется вследствие неполной предварительной очистки металла от шлака, краски, масла и других загрязнений.
Основные затруднения при расшифровке индикаторного рисунка связаны с тем, что при контроле сварных швов магнитный индикатор часто задерживается на неровностях швов, оседает в местах наплывов металла, а также по границам раздела двух структур металла. Чтобы избежать этого, необходимо зачищать неровности шва. Трещины в сварных швах являются опасными, так как в процессе эксплуатации могут приводить к трещинам усталости.
Дефекты, возникающие при шлифовании, из-за повышенного местного нагрева шлифуемой поверхности детали. Наиболее склонны к образованию этого вида трещин цементированные, азотированные и закаленные детали из легированных и малоуглеродистых сталей. При неправильно подобранных режимах шлифования на поверхности хромированных деталей, как правило, возникают шлифовочные трещины.
При магнитном контроле шлифовочные трещины легко отличить от других трещин: они тонки, неглубоки (от 0,0001 до 0,01 мм) и, как правило, располагаются на поверхности группами в виде сетки или тонких линий поперек направления шлифовки.
Шлифовочные трещины резко понижают усталостную прочность деталей, их ни в коем случае нельзя допускать к эксплуатации в местах концентраторов напряжений. Кольца и ролики подшипников подвижного состава, в которых в результате МПК обнаруживаются шлифовочные трещины, бракуются.
Закалочные трещины возникают главным образом при охлаждении деталей в процессе закалки в результате действия внутренних напряжений. Они могут возникать и на деталях, длительное время не подвергавшихся отпуску, уменьшающему внутренние напряжения.
Отличительным признаком закалочных трещин является неопределенность их направления на поверхности детали. При магнитном контроле они легко выявляются даже при слабом намагничивании, так как материал закаленных деталей имеет достаточно высокие значения остаточной индукции и коэрцитивной силы, а трещины – большие и почти всегда выходят на поверхность в виде ломаных, извилистых линий, идущих в различных направлениях. Четкие и рельефные рисунки осажденного порошка, получающиеся над закалочными трещинами, позволяют отличить их от других дефектов.
ковочные и штамповочные трещины возникают из-за наличия в исходном материале литейных изъянов (усадочных раковин, рыхлот) или из-за несоблюдения температурных режимов ковки или штамповки. Магнитопорошковым методом данные дефекты выявляются достаточно хорошо, как и закалочные трещины, – в виде четких рельефных линий, имеющих разнообразные направления на поверхности детали.