Файл: Учебное пособие соответствует фгос во по специальности 23. 05. 04 Эксплуатация железных дорог.docx
ВУЗ: Не указан
Категория: Не указан
Дисциплина: Не указана
Добавлен: 30.11.2023
Просмотров: 486
Скачиваний: 5
СОДЕРЖАНИЕ
2. ТЕРМИНАЛЬНО-ЛОГИСТИЧЕСКИЕ ЦЕНТРЫ
2.1. Инфраструктура терминально-логистических центров
2.2. Классификация терминально-логистических центров
3. СКЛАДСКИЕ КОМПЛЕКСЫ. ЛОГИСТИКА СКЛАДИРОВАНИЯ
3.1. Роль складов в логистических системах
3.2. Классификация складов и особенности складских объектов разных типов
3.3. Основные функции складов в логистической системе
3.4. Устройство современного склада как технической системы
3.6. Обработка грузов на складе
3.7. Проектирование технического оснащения склада
4. УСТРОЙСТВО И ТЕХНОЛОГИЯ РАБОТЫ КОНТЕЙНЕРНЫХ ТЕРМИНАЛОВ
4.1. Основные функции контейнерных терминалов
4.2. Характеристика терминала как объекта в логистической цепи
4.3. Оборудование контейнерных терминалов
4.4. Схемы терминальных операций с контейнерами
4.5. Проектирование контейнерных терминалов
5. ВОЗМОЖНЫЕ ВАРИАНТЫ КОМПОНОВКИ ТЕРМИНАЛЬНО-ЛОГИСТИЧЕСКИХ ЦЕНТРОВ
5.1. Типовые технологические решения терминально-логистических центров
5.2. Критерии выбора мест расположения терминально-логистических центров
5.3. Структурно-планировочные требования к инфраструктуре терминально-логистических центров
5.5. Интегрированная таможенная инфраструктура
5.6. Современные таможенные технологии
5.8. Экономическая эффективность создания терминально-логистических центров
4.3. Оборудование контейнерных терминалов
4.3.1. Автопогрузчики
Оборудование контейнерных терминалов можно разделить на две группы:
– основное технологическое оборудование для переработки, перегрузок и складирования контейнеров (краны, погрузчики, грузозахватные устройства и т. д.);
– оборудование вспомогательных служб и сооружений контейнерного терминала (электротехническое, сантехническое, ремонтное, охранное, устройства связи, сигнализации, пожаротушения и т. п.).
На сухопутных контейнерных терминалах (железнодорожно-автомобильных или только автомобильных) контейнеры разгружают с подвижного состава железнодорожного и автомобильного транспорта или загружают на него при помощи различных кранов (стреловых, козловых, мостовых) или автопогрузчиков. Это же оборудование применяют для перестановки контейнеров на участке хранения, сортировки и для погрузки их на железнодорожный или автомобильный транспорт.
Для переработки крупнотоннажных контейнеров зарубежные предприятия («Кальмар», Швеция; «Линде», Германия; «Валмет», Финляндия; «Хайстер», Англия; «Белотти», Италия; «Мицубиси», Япония и др.) изготовляют различные специальные автопогрузчики (рис. 4.5, табл. 4.1). Такие автопогрузчики оборудованы боковым выдвижным грузоподъемником, оснащенным специальным быстросъемным захватом. Захват (спредер) обычно имеет гидравлический привод поворотных кулачков. Некоторые модели таких автопогрузчиков оборудованы передвижной (в поперечном направлении) кабиной водителя для улучшения обзора места работы. В связи со значительной нагрузкой от колес рассматриваемые автопогрузчики должны применяться на площадках с прочным бетонированным покрытием [8].
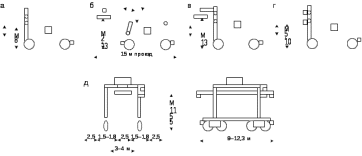
Рис. 4.5. Автопогрузчики зарубежного производства для переработки крупнотоннажных контейнеров: а – фронтальный с вилочным грузозахватом;
б – с выдвижной крановой стрелой (рич-стакер); в – с фронтальным верхним грузозахватом, который берет контейнер не сверху или снизу, а сбоку и применяется для перегрузки порожних контейнеров, складируя их до пяти ярусов по высоте; г
– с фронтальным боковым грузозахватом; д – портальный
Таблица 4.1
Характеристика автопогрузчиков зарубежного производства
для переработки крупнотоннажных контейнеров на терминалах
Параметр | Автопогрузчик | ||
с фронтальным грузозахватом | с выдвижной крановой стрелой (рич-стакер) | портальный | |
Грузоподъемность, т | 30–40 | 40–55 | 30,5–40 |
Высота подъема, м | 9–13,4 | 12,5 | 5,5–11,7 |
Ширина проездов, м: – для штабелирования – пересекающихся под углом 90 С | 12–16 10 | 10–15 12 | 6–7 20 |
Габаритные размеры, м: – длина – ширина – высота | 10,4 4,15 6,5–9,6 | 10,7 4,5 4,8–14 | 9–12,3 4,3–4,9 9–17,5 |
Число ярусов штабелирования груженых контейнеров по высоте: – в первом от проезда ряду – во втором ряду – в третьем ряду | 4 – – | 5 4 3 | 3–5 – – |
Число ярусов штабелирования порожних контейнеров по высоте: – в первом от проезда ряду – во втором ряду – в третьем ряду | 5 – – | 5 4 3 | 3–5 – – |
Производительность перегрузки контейнеров, тыс. конт.: – за час – за сутки – за год | 8–15 150–300 50–100 | 10–20 200–400 70–140 | 12–15 240–300 80–100 |
Давление на покрытие площадки, т/м2 | 60–85 | 65–90 | 12–20 |
Собственная масса, т | 50–55 | 55 | 50 |
Срок службы, годы | 10 | 10 | 12 |
Расход топлива, л/ч | 15–20 | 15–20 | 12–15 |
Автопогрузчики рич-стакеры (рис. 4.6) находят все более широкое распространение на зарубежных контейнерных терминалах
, вытесняя краны. Причиной этого являются их преимущества: отсутствие стационарных подкрановых путей и сети электроснабжения; маневренность и неограниченная зона действия; короткие сроки ввода терминала в действие; простота перепланировки и реконструкции терминала.
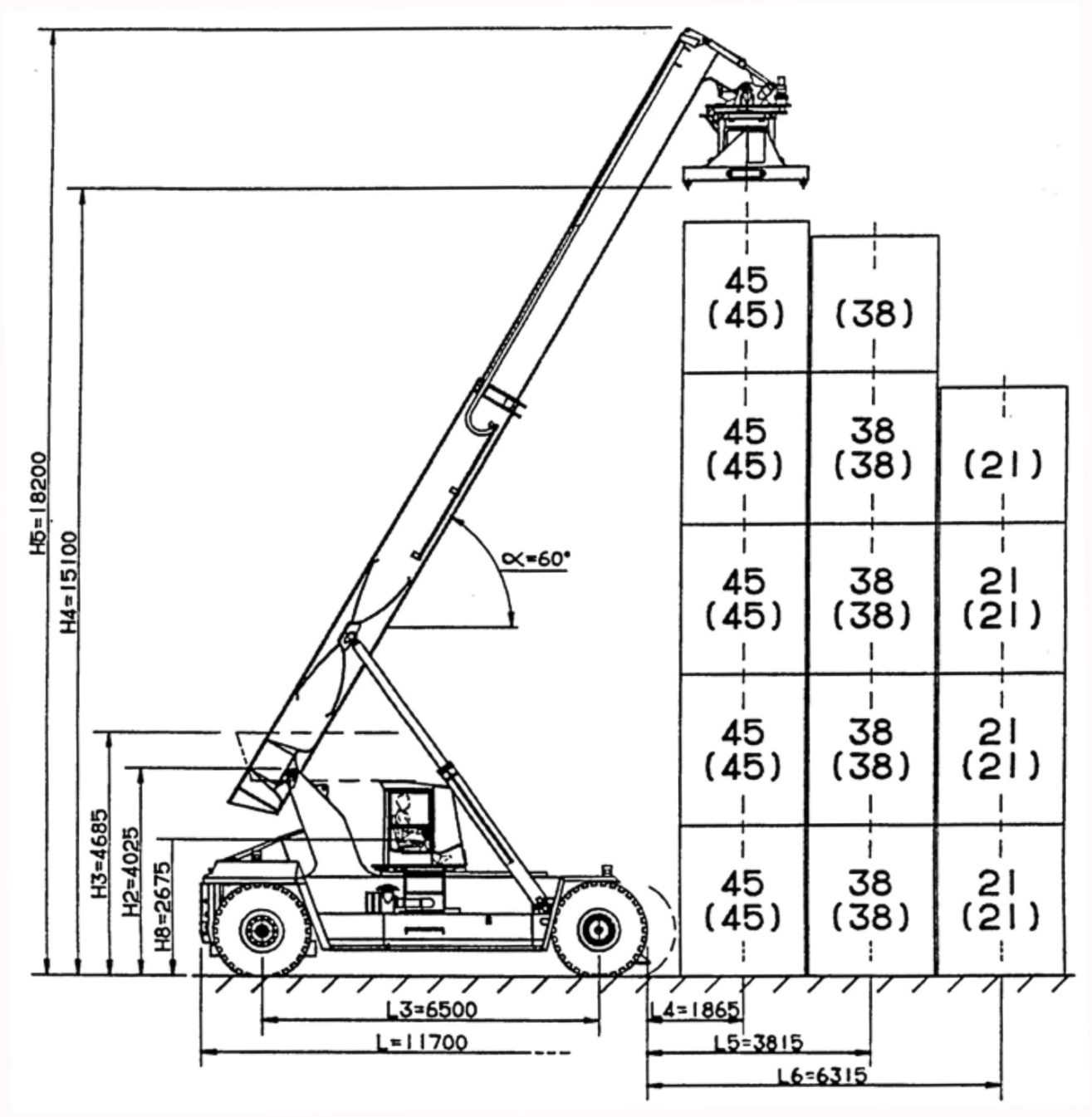
Рис. 4.6. Автопогрузчик рич-стакеры зарубежного производства
(reach-stacker – штабелер с выдвижным грузозахватом)
Недостатки автопогрузчиков: высокая стоимость (до 400 тыс. долл. США и более); большой расход дизельного топлива; значительные сосредоточенные нагрузки и высокая стоимость покрытия контейнерной площадки (около 30 долл./м2); сложность и высокая стоимость эксплуатации, технического обслуживания и ремонта. Автопогрузчики иногда применяют на контейнерных терминалах в различных сочетаниях с крановым оборудованием. Российская промышленность пока такие погрузчики не производит.
Как вспомогательное средство перемещения контейнеров внутри терминалов автопогрузчики широко используются в морских и речных портах, где в качестве основного перегрузочного средства по схеме «судно-берег» («судно-вагон») и обратно применяются портальные крюковые краны и причальные береговые перегружатели.
4.3.2. Мостовые краны
На современных контейнерных терминалах применяют также другие безрельсовые перегрузочные машины – портальные мостовые краны на пневмоходу (рис. 4.7). Контейнерные краны на пневмоходу имеют грузоподъемность 30–50 т, пролет моста в свету 7550–12 100 мм (что позволяет разместить в пролете два-три контейнера и автопроезд), высоту подъема грузозахвата 6300–12 800 мм (что позволяет штабелировать контейнеры на 2–4 яруса по высоте) и могут загружать и разгружать с железнодорожных платформ и автомобилей контейнеры и автопоезда. Скорости движения крана 134 м/мин, тележки – 52 м/мин, подъема-опускания – 9–17 м/мин, давление колеса на площадку – 48 т (480 кН).
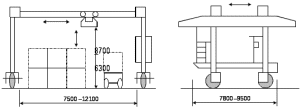
Рис. 4.7. Схема мостового портального контейнерного крана
на пневмоходу
Портальные складские перегружатели перемещаются по территории контейнерного терминала на пневматическом ходу или по рельсам и производят выгрузку-погрузку контейнеров на суда контейнерных линий или погрузку контейнеров на железнодорожные контейнерные платформы на тыловом фронте терминала. Такая схема наиболее применима для контейнерных терминалов, осуществляющих большой объем экспортной отгрузки контейнеров на морские суда, поскольку непредсказуемость момента выборки импортного контейнера, выгруженного в штабель с судна контейнерной линии, не позволяет оптимально использовать всю высоту штабеля (см. рис. 4.7).
При переработке контейнеров на терминалах возникает необходимость транспортирования их внутри терминала с одних технологических участков на другие (например, с разгрузочного участка в зону хранения или из зоны хранения на таможенный досмотр и т. п.). При больших грузопотоках эти операции целесообразно выполнять с применением специализированного транспортного оборудования автопоездами с платформами-трейлерами, которые могут транспортироваться специальными терминальными автотягачами, универсальными автотягачами или колесными тракторами, оснащенными специальными захватно-зацепными устройствами. Применяют также портальные автопогрузчики (см. рис. 4.5, д), которые могут не только транспортировать, но и штабелировать контейнеры. Портальные автоконтейнеровозы могут образовывать штабель высотой в 3–4 яруса и доставлять контейнеры между причальными, складскими зонами и зоной таможенного досмотра контейнеров. С их помощью производится также перегрузка контейнеров на магистральные погрузчики, доставляющие контейнеры в зону их погрузки на автотранспорт, осуществляющий вывоз и ввоз контейнеров из порта.
При разгрузке судов типа Ро-Ро грузы выгружают не кранами вверх через трюмные люки, а горизонтально через открывающиеся проемы в борту судна. Поскольку проемы в борту судна для горизонтальной разгрузки нецелесообразно делать очень большими, для въезда и выезда с грузами применяют специальные низкие платформы-трейлеры (высотой 600–800 мм) в сочетании с автотягачами или специальные автопогрузчики с пониженной собственной высотой.
4.3.3. Рамные трейлеры
Рамные трейлеры (Skeletal Trailers), – одно- и двухосные, грузоподъемностью от 35 до 70 тонн (рис. 4.8) предназначены для перевозки внутри контейнерных терминалов стандартных морских контейнеров: 20, 40 и 45 ДФЭ. Перемещение трейлеров выполняется портовым тягачем посредством фиксации опорного пальца (king pin) к так называемому пятому колесу тягача и в рабочих условиях не занимает больше 1 минуты времени.

Рис. 4.8. Рамные трейлеры
Мультитрейлерные поезда (Multi