Файл: Учебное пособие соответствует фгос во по специальности 23. 05. 04 Эксплуатация железных дорог.docx
ВУЗ: Не указан
Категория: Не указан
Дисциплина: Не указана
Добавлен: 30.11.2023
Просмотров: 517
Скачиваний: 5
СОДЕРЖАНИЕ
2. ТЕРМИНАЛЬНО-ЛОГИСТИЧЕСКИЕ ЦЕНТРЫ
2.1. Инфраструктура терминально-логистических центров
2.2. Классификация терминально-логистических центров
3. СКЛАДСКИЕ КОМПЛЕКСЫ. ЛОГИСТИКА СКЛАДИРОВАНИЯ
3.1. Роль складов в логистических системах
3.2. Классификация складов и особенности складских объектов разных типов
3.3. Основные функции складов в логистической системе
3.4. Устройство современного склада как технической системы
3.6. Обработка грузов на складе
3.7. Проектирование технического оснащения склада
4. УСТРОЙСТВО И ТЕХНОЛОГИЯ РАБОТЫ КОНТЕЙНЕРНЫХ ТЕРМИНАЛОВ
4.1. Основные функции контейнерных терминалов
4.2. Характеристика терминала как объекта в логистической цепи
4.3. Оборудование контейнерных терминалов
4.4. Схемы терминальных операций с контейнерами
4.5. Проектирование контейнерных терминалов
5. ВОЗМОЖНЫЕ ВАРИАНТЫ КОМПОНОВКИ ТЕРМИНАЛЬНО-ЛОГИСТИЧЕСКИХ ЦЕНТРОВ
5.1. Типовые технологические решения терминально-логистических центров
5.2. Критерии выбора мест расположения терминально-логистических центров
5.3. Структурно-планировочные требования к инфраструктуре терминально-логистических центров
5.5. Интегрированная таможенная инфраструктура
5.6. Современные таможенные технологии
5.8. Экономическая эффективность создания терминально-логистических центров
Вешала. Механизированные вешала используют для хранения верхней одежды на плечиках и некоторых товаров, требующих хранения в подвешенном состоянии.
Бункеры. Бункерные устройства – емкости прямоугольной, круглой или конической формы для хранения навалочных и сыпучих грузов. Сверху у них имеются загрузочные устройства, снизу – высыпные люки с затворами. Применяются деревянные, железобетонные и металлические бункеры емкостью до 100 м3 и более.
Закрома – сформированные вертикальными перегородками открытые емкости для насыпки навалочных грузов. Обычно устраивают деревянные и железобетонные закрома в закрытых или открытых складах.
Резервуары (цистерны, баки, бочки) используют для хранения наливных грузов. Резервуары изготавливают из стали и железобетона. Их оборудуют люками для выполнения замеров, чистки и ремонта, а также приспособлениями для слива, налива и для выпуска воздуха. Удобны для хранения, погрузки, разгрузки и перевозки наливных грузов специализированные контейнеры массой брутто 30, 20, 10, 5 и 1,25 т.
3.7.4. Механизмы транспортировки
Для того чтобы правильно выбрать оборудование, нужно учитывать ряд условий:
– качество полов;
– расстояние между стеллажами (лучше, если оно планируется исходя из характеристик оборудования);
– высоту подъема груза;
– массу поднимаемого груза;
– массу груза на максимальной высоте подъема.
В механизированных системах применяется множество разновидностей подъемно-транспортного оборудования (рис. 3.6) [12].
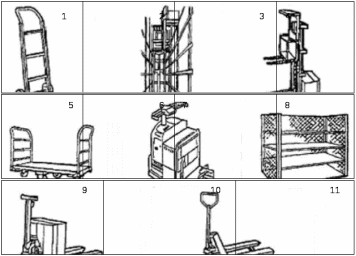
Рис. 3.6. Образцы механического подъемно-транспортного оборудования: 1 – двухколесная ручная тележка; 2 – аутригерный стеллажный штабелер с вращающейся платформой; 3 – стеллажный подъемник-подборник; 4 – стеллажный подъемник с выносным плечом; 5 – напольная опрокидывающаяся тележка; 6 – буксировщик-тягач; 7 – передвижная конструкция стеллажного типа; 8 – тяжелый стеллажный подъемник; 9 – самоходный погрузчик поддонов; 10 – ручной погрузчик
поддонов; 11 – грузовая автоплатформа
Самоходные тележки
не пользуются такой популярностью, как гидравлические, их используют, когда необходимо перемещать груз на достаточно большие расстояния.
Ручные гидравлические штабелеры хороши, когда нет большого объема работ, также их можно использовать как вспомогательное оборудование. Грузоподъемность гидравлических ручных штабелеров, как правило, не превышает 1000 кг, а высота подъема – 3 м.
Штабелеры с электроподъемом эффективно применять на небольших складах, если с их помощью не требуется перемешать грузы на большие расстояния и высота стеллажей составляет не более 3,5 м. Грузоподъемность штабелеров с электроподъемом не превышает 1200 кг.
Самоходные штабелеры с электроподъемом бывают грузоподъемностью до 3 т и с высотой подъема до 5,5 м. Самоходные штабелеры с электроподъемом широко используются в России, так как они просты в обслуживании и эксплуатации, но при этом позволяют выполнять большой объем работ.
Ричтраки (высокоподъемные штабелеры с выдвигающейся кареткой) – это мощные и бесшумные машины грузоподъемностью до 3,5 т и высотой подъема до 11,5 м. Бывают специализированные ричтраки с колесами увеличенного диаметра и шинами суперэластик для работы на неровной поверхности.
Двухколесные ручные тележки выпускают в трех вариантах: изготовленные из комбинированных материалов (дерево и сталь), полностью стальные или сделанные из алюминиевых сплавов. Грузоподъемностью до 2000 фунтов (чуть более 900 кг). Встречается несколько разновидностей конструкций.
Аутригерные стеллажные штабелеры с вращающейся платформой поднимают оператора на ту же высоту, что и перемещаемый поддон. Эти механизмы используются для подъема поддонов в очень узких проходах между двусторонними стеллажами на высоту до 40 футов (12 м).
Стеллажные подъемники-подборщики служат для подъема оператора на платформе, оборудованной вилочным устройством. С его помощью оператор подбирает упаковки или ящики с полки стеллажа и переносит их на поддон или передвижную конструкцию стеллажного типа;
Стеллажные подъемники с выносным плечом применяют в узких проходах для загрузки поддонов на стеллажи или снятия их со
стеллажей. Некоторые оборудованы пантографами и позволяют загружать поддоны на двойную глубину стеллажей.
Напольные опрокидывающиеся тележки отличаются чрезвычайной маневренностью даже при перемещении длинных упаковок или навалочных грузов благодаря тому, что балансируют на двух расположенных по центру колесах и одном или двух малых колесиках, расположенных с каждого края.
Буксировщики-тягачи – это самоходные передвижные устройства с ручным управлением, предназначенные для буксировки одного или нескольких четырехколесных полуприцепов на дальние расстояния. Могут быть использованы за пределами внутреннего складского помещения.
Передвижные конструкции стеллажного типа устанавливают на платформы самоходных погрузчиков или автотягачей для перевозки неупакованной продукции и небольших упаковок. Используют при подборке заказов.
Тяжелые стеллажные подъемники выпускаются в нескольких вариантах: с электрическими аккумуляторами или двигателями внутреннего сгорания в качестве источников питания. Существуют трех- и четырехколесные модели.
Самоходные погрузчики поддонов – многофункциональные механизмы для погрузки-разгрузки поддонов с ограниченной высотой подъема и полезной нагрузкой 3000–8000 фунтов (1360–3630 кг). Широко используются на продовольственных складах.
Ручные погрузчики поддонов остаются одним из самых популярных механизмов для перемещения единичных грузов. Грузоподъемность достигает 10 тыс. фунтов (4540 кг). Могут быть оборудованы тормозными колодками.
Грузовые автоплатформы предназначены для перемещения крупных грузов на большие расстояния. Снабжены отдельной кабиной для водителя. Могут бытьиспользованы и внутри, и за пределами складских помещений.
При использовании машин, механизмов или их систем наряду с такими показателями, как ожидаемая производительность, надежность, относительно малая стоимость, должны быть предусмотрены и такие их характеристики, которые обеспечивали бы непрерывность общего технологического процесса, хорошо вписывались бы в логистическую концепцию данной системы хранения и переработки. Кроме того, применяемые средства должны обладать высокой степенью технологической совместимости не только друг с другом, но и в общей совокупности технического парка, причем как в складском хозяйстве, так и в основном производстве. В соответствии с принципами логистики к применению каждого механизма необходимо подходить не только как к отдельному средству замены ручного труда, но и как к базовому элементу для перехода к комплексной механизации и автоматизации логистических процессов.
В связи с этим в логистике получил распространение термин «гибкий складской модуль» (ГСМ). Гибкий складской модуль представляет собой единицу подъемно-транспортного или иного складского оборудования системы грузопереработки, которая обладает гибкостью и имеет микропроцессорную систему управления [8].
Гибкий складской модуль предназначен для выполнения работ по упаковке, комплектации, транспортировке товаров произвольной номенклатуры. Он автоматически осуществляет свои функции, органично встраиваясь в действующую гибкую систему складской грузопереработки.
Сама гибкая система складской грузопереработки (ГССГ) представляет собой совокупность разных сочетаний гибких складских и гибких производственных модулей, роботизированной внутрискладской транспортной сети, систем обеспечения их функционирования в автоматическом или полуавтоматическом режиме в течение заданного времени.
Гибкие системы складской грузопереработки предназначены для автоматизации технологических процессов на отдельных складах и в системах хранения-переработки, которые сами по себе рассматриваются как организационное и функциональное целое. Иными словами, речь идет о соответствующих системах в торгово-посреднических и транспортных структурах, не связанных непосредственно с процессом производства продукции (в производственных структурах формируются гибкие производственно-логистические системы – ГПЛС).
Гибкие системы складской грузопереработки наиболее эффективны при обеспечении местных потребителей продукцией в нетранзитных количествах. Они в полной мере обладают логистическим свойством – свойством адаптации к изменяющимся параметрам перерабатываемой продукции в установленных пределах. Максимальный эффект при использовании данных систем проявляется на складах с широкой и постоянно меняющейся номенклатурой перерабатываемой продукции (например, на складах запасных частей). В то же время применение гибких систем складской грузопереработки может быть экономически оправдано и на складах с узкой и относительно стабильной номенклатурой.
Роботизированная внутрискладская транспортная сеть, составляющая один из элементов гибкой системы складской грузопереработки, предназначена для внутрискладской транспортировки средствами напольного или иного автоматизированного транспорта различных грузов в установленных пределах значений их параметров с возможностью оперативной перестройки маршрутов перемещения с минимальными затратами. Наиболее полно требованиям роботизированной внутрискладской транспортной сети на современном этапе развития техники отвечают робокары. В то же время в рамках данной сети могут использоваться транспортные роботы другого типа и иное оборудование.
Транспортный робот – это специализированный робот, предназначенный для выполнения транспортных операций в рамках гибкой производственно-логистической системы, гибкой системы складской грузопереработки и других систем [8].
Транспортные роботы подразделяются:
-
на напольные:
-
рельсовые; -
безрельсовые;
-
подвесные:
-
монорельсовые; -
портальные; -
консольно-крановые.
Напольные рельсовые транспортные роботы получили широкое распространение при обслуживании роботизированных технологических комплексов. Однако затраты на изменение их трассы значительно выше, чем при использовании безрельсовых транспортных роботов, которые по указанному и ряду других аспектов более полно удовлетворяют требованиям гибкости.
Безрельсовые транспортные роботы называются робокарами.
В данную группу технических средств включают также электроробокары, робототележки и др. В настоящее время известны три основных типа транспортных роботов этой категории.
1. Несущие робокары (робототележки), оборудованные рабочим столом, рольгангами или другой специальной оснасткой в зависимости от назначения.
2. Автоматические тягачи, оборудованные тяговыми крюками, к которым присоединяются грузовые механические тележки.
3. Штабелеры, оборудованные стационарными или поворотными вилами и способные автоматически забирать и устанавливать груженые поддоны на различных уровнях. На вилах таких штабелеров обычно размещаются по два поддона.
На большинстве робокаров, занятых на транспортно-перемещающих операциях, в качестве силовых установок используют тяговые электродвигатели с питанием от аккумуляторных батарей. Иногда применяют другие силовые установки. Для управления этими видами транспортных роботов используются оптические, индуктивные, инфракрасные, лазерные и другие системы маршрутослежения.
Часто при автоматизации логистических операций в системах хранения и переработки используются различные манипуляторы, которые могут функционировать как самостоятельно, так и в комплексе с транспортным роботом.